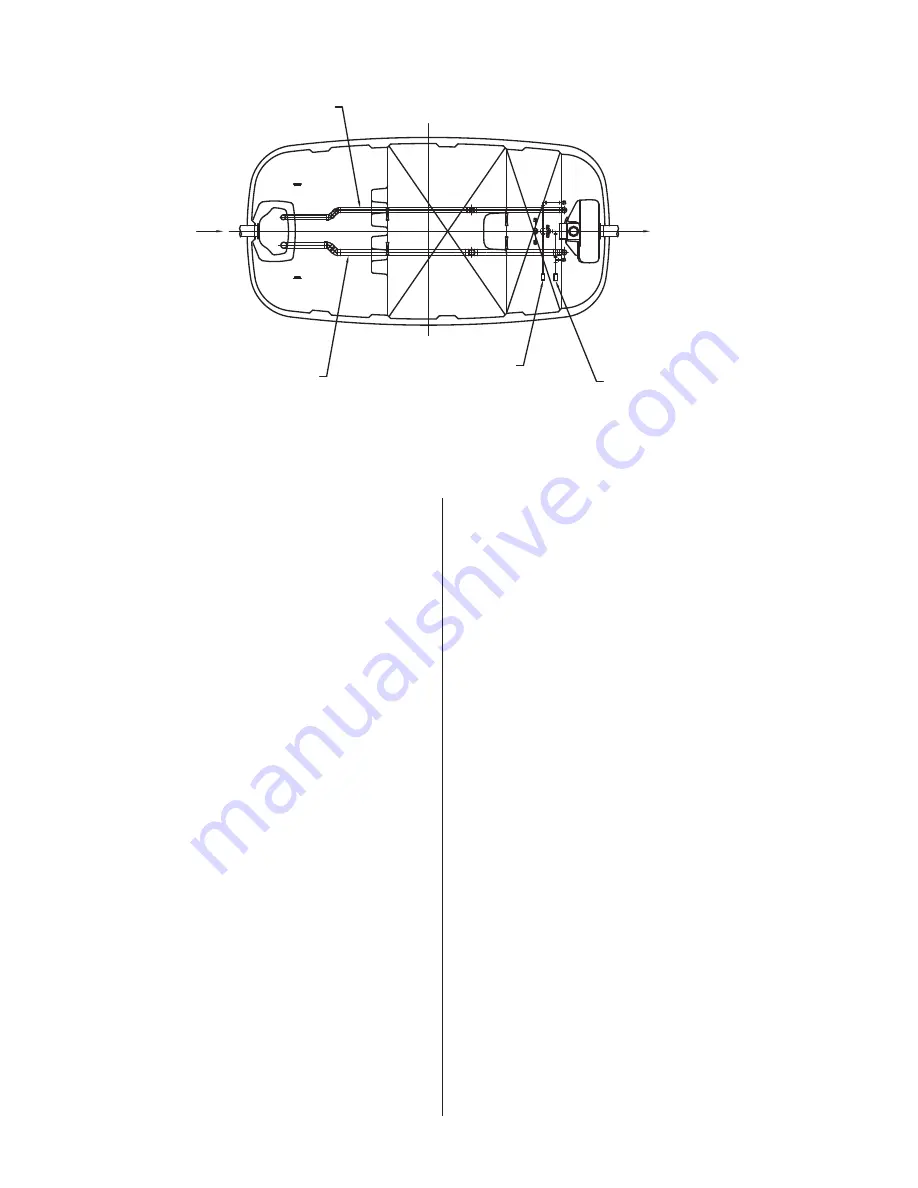
12
© Copyright 2022. All rights reserved.
The following steps are to be completed during each
6-month inspection. All information collected during the
inspection is to be recorded on the Maintenance and Service
Report (CL0059). Begin the inspection by recording the date,
arrival time, weather conditions, purpose of the visit, water
use, model number, serial number, the presence or absence
of a septic tank, and the system owner and service provider
information in the space provided on the report.
1. Are any odors present?
There should be no odor
with the lids closed, if properly sealed. With lids
removed, a septic or sewer-like odor is indicative
of poor treatment and is common immediately after
startup due to hydrogen sulfide and other gases. A
well-operating system will have a musty, earthy smell
similar to wet peat moss.
2. Is there evidence of high water?
Typically indicated
by a water level above the black wall markings and
above the “0” graduation on the partition wall stickers.
May also be indicated by debris on partition walls.
3. Is there excess foam formation?
Foam may be
present during an inspection. Brown foam indicates
bacterial buildup following startup. White foam is
due to detergent use. Neither is a problem if occurring
intermittently. Detergent-based foam will often be
accompanied by low transparency readings.
4. Is there residue build-up on piping?
Typically indicated
by gray or black residue (dried foam) on aeration
chamber piping.
5. Is there even and vigorous bubbling?
Bubbles surfacing
in the aeration chamber should be even across the
entire chamber. If uneven, cleaning steps should resolve
this issue.
REQUIRED WATER QUALITY ANALYSES
PART A: Clean Water Storage Chamber –
Collect samples
from the clean water storage chamber to be used for
the following analyses
1. Transparency
–
Measures the ability of the water to
transmit light. Using the ladle, fill the transparency
tube with a water sample collected from the clean
water storage chamber. Looking down through the
water column, slowly drain the transparency tube
using the valve on the flexible hose until you can
first distinguish between the black and white colors
on the secchi disk in the bottom of the tube. When
the secchi disk is visible, close the valve and read
the transparency (in centimeters) on the side. Dirty
water samples transmit less light and result in a lower
transparency. A transparency reading > 20 cm is
preferred and 34 cm is average. Low transparency
may be due to a lack of biological activity as in a
young system, a recirculation rate that is too high,
or a system influent high in detergent concentration.
To correct low transparency readings not caused by
detergent, decrease the recirculation rate. Detergent
based problems may require consultation with owner.
2. Scum –
Very small amounts of scum may accumulate
in the corners on the outlet end of the system. This
is normal. Scum, should not be present elsewhere
in the clean water storage chamber unless the
recirculation rate is too high or daily flow exceeds
the design capacity. If present, use ladle to transfer
to sedimentation chamber.
3. Sludge –
Test the sludge depth using the sampling
device included in the maintenance kit. The bottom
section of the sampler includes a check valve, which
opens as the unit is lowered into the liquid. When
the sampler has reached the bottom of the chamber
and the liquid level equilibrated at surface level, lift
the sampler and this action will set the check valve
and retain the sample in the tubing. Withdraw the
sampler and note the depth of settled solids within
GENERAL OBSERVATIONS
Figure 16 - Inspection details.
FUSION
®
OPERATION AND MAINTENANCE
SK2801
INLET
3/4" AIRLINE ADAPTER
RECIRCULATION
1" AIRLINE ADAPTER
BACKWASH
2" RECIRCULATION
RETURN LINE
2" BACKWASH
RETURN LINE
OUTLET
Содержание Fusion Series
Страница 17: ...17 Copyright 2022 All rights reserved ...