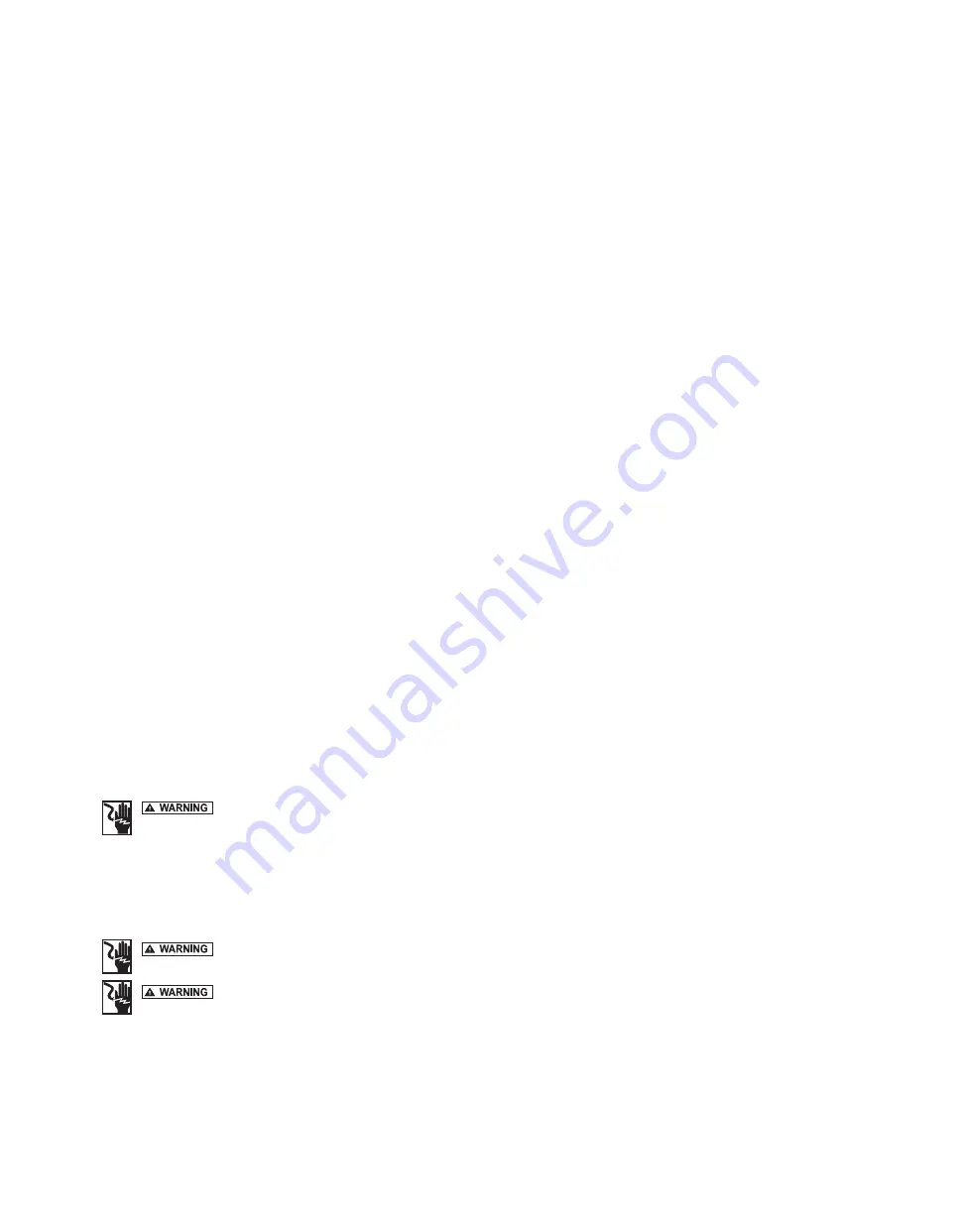
Introduction
The preassembled 24 x 24 sewage system is complete and job ready from the
factory for easy installation. Its compact design makes it perfect for low burial
depth applications. The system features a removable access port that allows
for the immediate observation of pumps and floats. Additional features include
a 41-gallon capacity, a built in anti-flotation device, and a construction cover to
keep everything clean during installation.
INSTALLATION
Preparation
Inspect your basin assembly. If the unit has been damaged in shipment or if
parts are missing, contact your distributor before installing. Carefully read all
literature to familiarize yourself with details regarding installation and use. Retain
materials for future reference. All installations must comply with all applicable
electrical and plumbing codes, including but not limited to the National Electrical
Code, local, regional and/or state plumbing codes, etc.
The clear construction cover can be reattached after reading the appropriate
materials. It will ensure the cover, cordage, etc. remains clean during installation.
Excavation
Excavate a hole for the basin in a very low traffic area in proximity to a proper
electrical outlet. The hole should be at least 8” larger in diameter than the basin
in order to leave 4” of backfill all the way around the perimeter. A minimum of 4”
of compacted subbase is also required. Backfill and subbase should be 1/8” to
3/4” pea gravel or 1/8” to 1/2” crushed stone.
Basin Placement
Ensure compacted subbase is free of any sharp rocks that could come into
direct contact with the basin. Place basin into pit and verify that it is level. It
is recommended that the top of the basin is level with the surrounding finished
floor. Once the desired positioning has been achieved, partially backfill basin to
help hold in place. Ensure enough room is left below the inlet to make the inlet
connection. Connect the 4” inlet pipe using a no-hub style connector and finish
backfilling around the basin with the specified media. Care should be taken not to
damage components or leave voids when backfilling. Finish grade of floor should
be poured in place around the top 6” of the basin assembly.
Electrical Connections
FOR YOUR PROTECTION, ALWAYS DISCONNECT PUMP
FROM ITS POWER SOURCE BEFORE HANDLING.
Single phase pumps are
supplied with a 3-prong grounded plug to help protect you against the
possibility of electrical shock.
DO NOT, UNDER ANY CIRCUMSTANCES,
REMOVE THE GROUND PIN.
The 3-prong plug must be inserted into a
mating 3-prong grounded receptacle. If the installation does not have
such a receptacle, it must be changed to the proper type, wired and
grounded in accordance with the National Electrical Code and all
applicable local codes and ordinances.
Risk of electrical shock
.
Do not remove power supply
cord and strain relief or connect conduit directly to the pump.
Installation and checking of electrical circuits and
hardware should be performed by a qualified licensed electrician.
Discharge/Vent
The 2” threaded discharge and vent ports are located and labeled on top of the
cover. Installations containing sewage pumps: 211, 212, 264, or 266 models must
not use a discharge smaller than 2”. Installations containing grinder pumps: 803,
805, or 807 must not use a discharge smaller than 1.25”. All venting needs to be
installed in accordance with any/all local and national plumbing codes.
Simplex:
Using an adapter, connect discharge pipe to the “Discharge” 2” threaded port and
connect vent pipe to the “Discharge/Vent” 2” threaded port.
Duplex:
Using an adapter, connect discharge pipes to both 2” threaded ports on top of
the cover. For the vent, use a 3” hole saw to drill a hole located at the pilot hole
indention on the cover. Install the included pipe seal and use 2” pipe for the vent.
Inspection Port
912/915 24x24 systems are equipped with an inspection port in the lid to allow for
the convenient observation and replacement of pump/alarm floats as needed.
For access, remove the safety screw located on top, turn the inspection cap
counterclockwise and lift.
Float heights are preset from the factory for optimum performance. During startup,
ensure all floats have adequate clearance and are operating appropriately.
Float tree removal:
The float tree may be easily removed for the inspection and replacement of floats.
It is held in place with compression between the lid and basin. To remove the float
tree, simply push down on the handle on top to free it from the bottom of the lid.
Lift the tree and floats upward through the inspection port. Lift the appropriate
cord seals from the top of the cover to relieve any attached cords. To reattach,
ensure cord seals have been fully inserted and lower the float tree back through
the inspection port. Reinsert the bottom of the float tree into the premolded ring
and push down on the top handle to reattach on the premolded bottom section of
the lid. Ensure floats are oriented with adequate clearance for operation.
© Copyright 2020 Zoeller Co. All rights reserved.