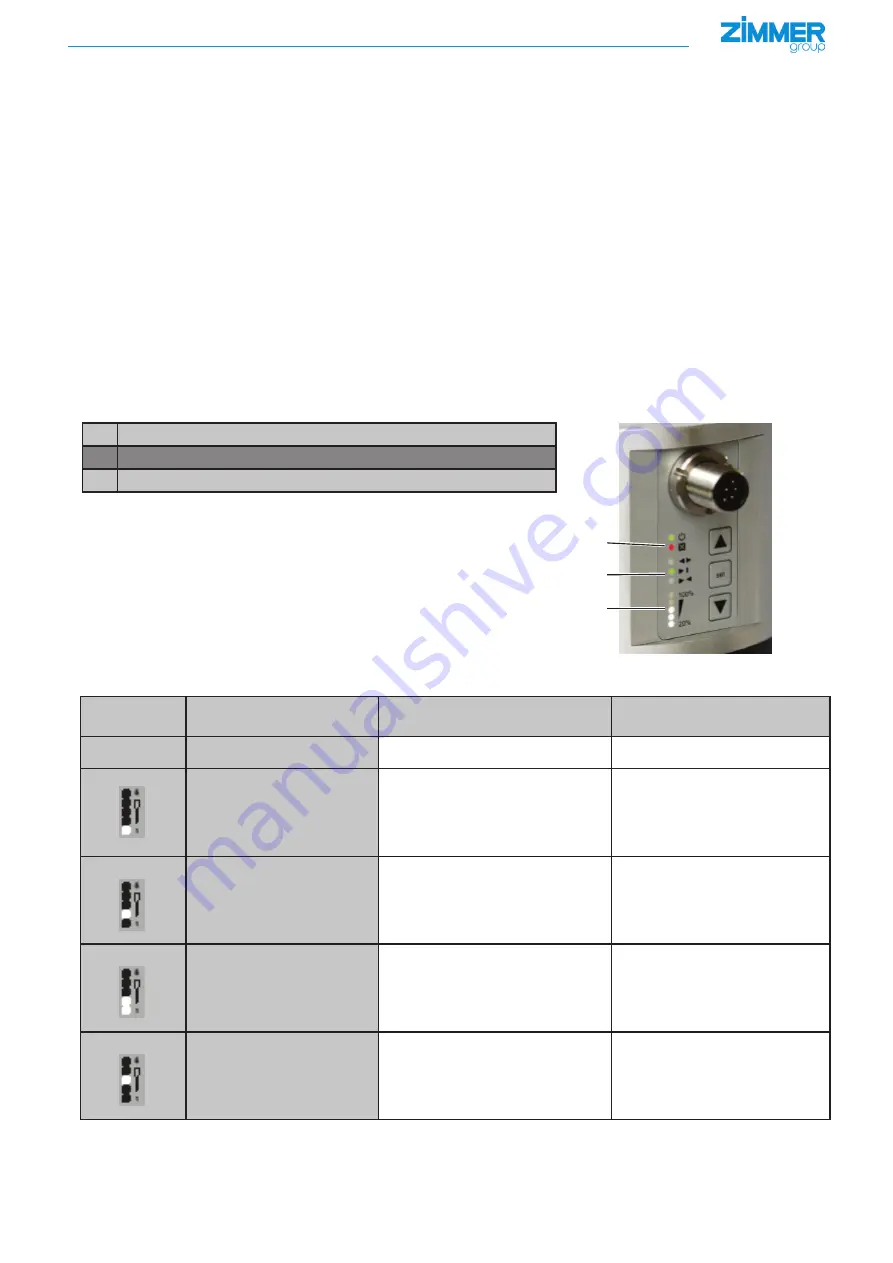
Zimmer GmbH
●
Im Salmenkopf 5
●
77866 Rheinau, Germany
●
Phone: +49 7844 9138-0
●
Fax: +49 7844 9138-80
●
www.zimmer-group.de
DDOC00198/t
EN/2015-10-07
15
INSTALLATION AND OPERATING INSTRUCTIONS:
ELECTRIC GRIPPER GEP/GED5000 SERIES
9. Maintenance
9.1
Maintenance intervals
The gripper does not require maintenance.
The operational life of up to 30 million cycles may become reduced under the following circumstances:
• Dirty environment
• Improper use
• Unapproved performance data and parameters for use
• Use of sealing air
9.2
Disassembling the gripper
We recommend using the Zimmer Group Repair Service for repairs.
Unauthorized dismantling and reassembly of the gripper can result in complications as in some cases, special mounting equipment
is required. In addition, the warranty is void if the gripper is opened.
10. Remedy
10.1
Error diagnosis
The red error LED indicates that an error has occurred. The main menu must be selected to see the error code. The five lower LEDs
represent the current error code in binary form.
In the following example,
error code 7
is active:
The error is acknowledged via a new DIR signal.
1
2
3
1
"Error" LED display
2
Position display
3
Error code display
10.2
Display troubleshooting
Error code
Error
Possible cause
•
Measure
0
No error
1
Motor has slight overcurrent in
several consecutively following
cycles
• Gripper is difficult to move
• Travel path of the gripper is
impeded
• Object being gripped or gripper
jaws are elastic
• Check the gripper's freedom of
movement
• Check the object being gripped
and gripper jaws
2
Motor has strong excess
current
• Gripper is blocked
• Internal error
• Restore the free movement of the
gripper once again
•
Zimmer Group Service
3
Motor has excess current in
idle mode
• Internal error
•
Zimmer Group Service
4
Motor output stage
temperature above the limit
value
• Ambient temperature too high
• Gripper is overloaded
• Provide sufficient ventilation/
cooling
• Check the object to be gripped or
the gripper jaw
*) See "Glossary" section for definitions