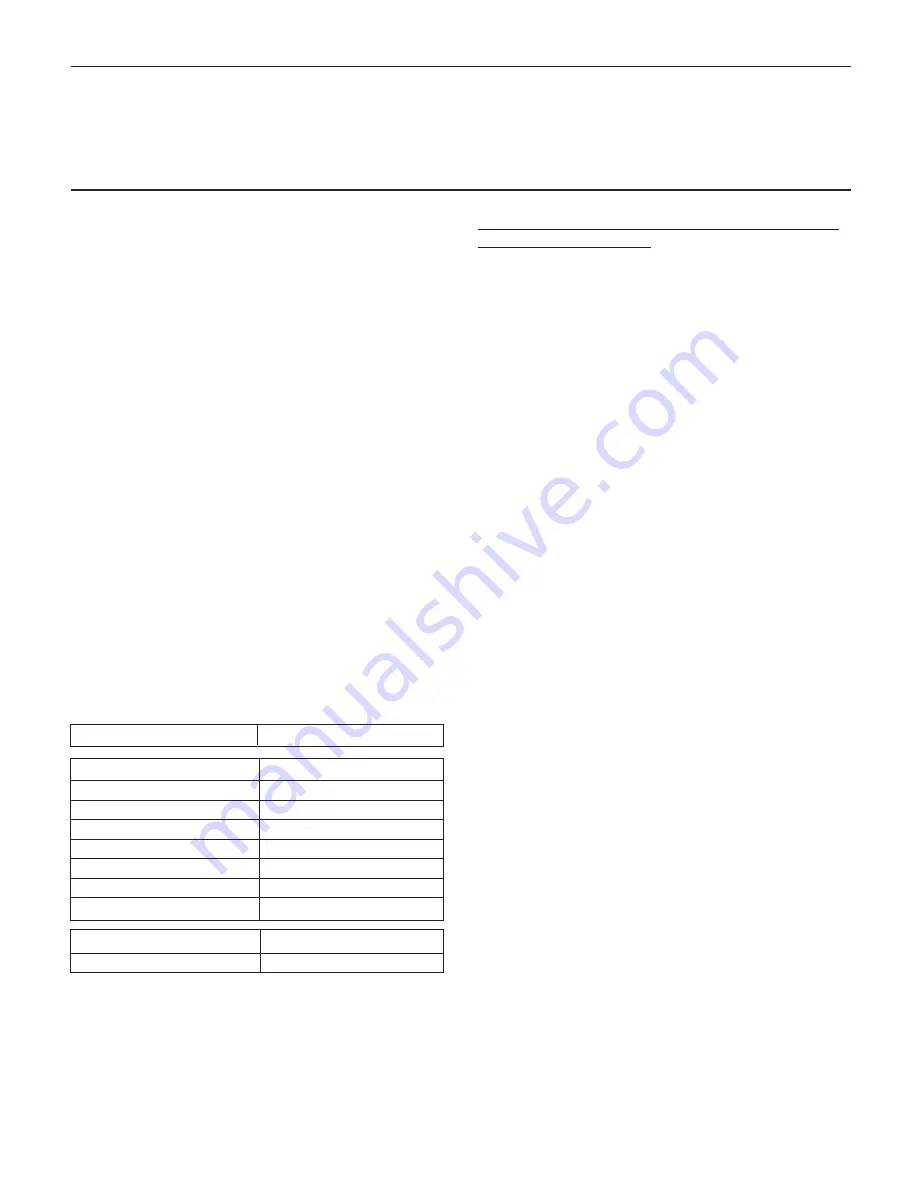
3.1 GENERAL MAINTENANCE INFORMATION
While the
A.T.S.
1200 Tourniquet has been designed and
manufactured to high industry standards, it is recommended
that regular inspection and calibration be performed to
ensure continual safe and effective operation. This section
contains information to assist in the effort as well as serve as
a guide to expediting unscheduled maintenance.
3.2 ACCESS TO PARTS
CAUTION:
Be sure that the unit is set to STANDBY and
the power plug is unplugged before disassembly. Many of
the parts on the control board are static sensitive. Take
precaution when servicing the board.
To gain access to all internal parts, remove:
a)
Rear – 5 screws
b)
Rear – 2 large pole clamp screws
c)
Bottom – 4 foot pad screws
See Illustration 4 through 8 in the back of the manual.
When opening, take care not to damage any of the wire
harnesses or pneumatic tubing. The control board is attached
to the front housing therefore the harnesses and tubing will
need to be disconnected for full disassembly. Follow the
table below to reassemble.
Table 3.1 Board Plug Designators
Component
Board Plug Location
AC Mains
P1
Overpressure Switch
P2
Speaker
P3
Pneumatic Pump
P5
Valve Harness
P6
Backup Battery
P7
Membrane Panel
P8
Factory Test Port
P9
Main Cuff Port Tube
U17
Second Cuff Port Tube
U21
To reduce the risk of damage, the tubing should be
disconnected at the plastic tee fitting and not the transducer.
NOTE: Failure to plug the electrical or pneumatic
components into the correct associated receptacle can
result in damage to the control board.
When reassembling the unit, be extremely careful not to
pinch any wiring or tubing.
3.3 PERIODIC MAINTENANCE
Test and inspect as per this section at minimum every six
months.
1.
Cleaning
The exterior of the unit may be cleaned with a cloth that
has been dampened (not dripping) with a mild detergent.
The interior of the unit may be vacuumed or blown out
as required. The exterior of the cuff hose may be cleaned
using a mild detergent solution or alcohol. The interior
of the cuff hoses should not be cleaned. Tourniquet cuffs
should be cleaned in accordance with their cuff package
inset instructions.
2.
Inspection
The unit should be inspected at regular intervals. It is
recommended that a qualified technician perform a
visual inspection at least once every six months.
Inspection points are:
a)
Obvious internal or external damage.
b)
Condition of the power cord.
c)
Condition of the power cord-retaining clip.
d)
Tightness of pneumatic fittings.
e)
Condition of internal tubing.
f)
Accumulation of dust or dirt within the unit.
g)
Mating integrity of internal connectors.
h)
Security of the EPROM and safety processor.
See Illustration 9 for location.
i)
Integrity of the pump.
j)
Security of circuit board.
k)
Security of the membrane panel.
3.
Functional and Calibration Checks
It is recommended that the functional and calibration
checks described in Section 2.4 are performed at least
once every three months.
3.4 CALIBRATION
Calibration should be performed every six months, or
after any unscheduled maintenance.
Calibration of the
A.T.S.
1200 Tourniquet allows the
output signal from the pressure transducer to be compared
against a calibrated pressure source. The difference between
the known pressure and the pressure measured by the
transducers is recorded at each of four set points (0 mm Hg,
50 mm Hg, 250 mm Hg, and 475 mm Hg). These four
calibration factors are used to correct the signal from the
pressure transducers during normal operation. The calibration
factors and a checksum are stored in non-volatile memory.
15
MAINTENANCE
SECTION 3.0
A.T.S. 1200 TOURNIQUET SYSTEM
Содержание A.T.S. 1200
Страница 1: ...Operator Service Manual A T S 1200 TOURNIQUET SYSTEM REF 60 1200 101 00...
Страница 26: ...R Power Cord S Cord Retaining Clip T Factory Test Port U Pole Clamp V Mains Fuse Block 24 2...
Страница 30: ...28 9 Control Board Layout...
Страница 32: ...30 10...
Страница 33: ...SCHEMATICS...