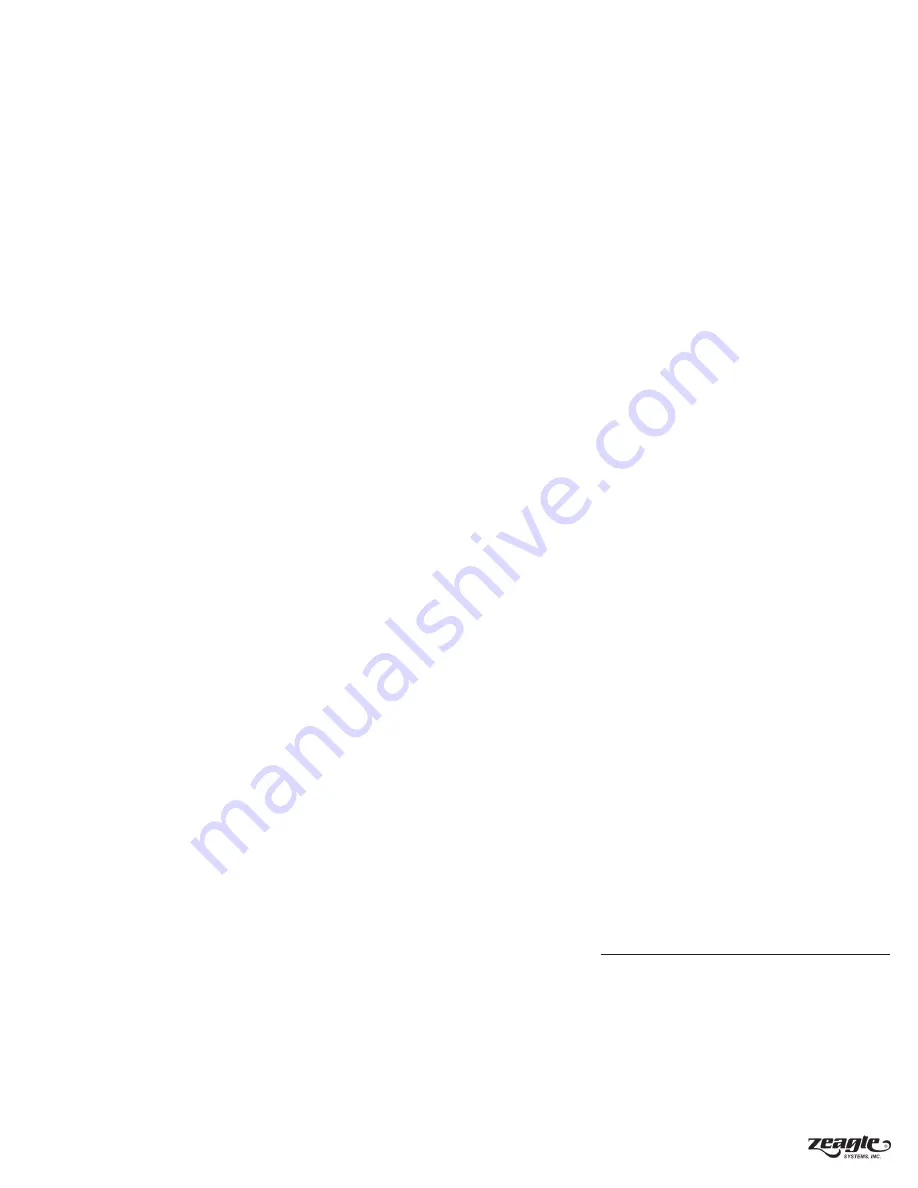
4.0 SERVICE PROCEDURES FOR THE ZEAGLE Octo-Z
4.0.1 Before you begin disassembly of the Octo-Z, attach it to a 1st stage and test it for function and leaks .
Pre-testing in this way will help the technician to pinpoint any specific problems requiring repair.
4.0.2 The work area must be clean and well lighted, with a tub of clean fresh water to test for leaks and
clean compressed air to blow sand and dirt from parts.
4.1 TOOLS & ITEMS REQUIRED FOR Octo-Z SERVICING
- Soft-jawed bench vise (bench vise with rubber, plastic, aluminum or plastic jaw inserts)
- 1/4” Nut Driver (available from hardware store)
- 3/16” Allen wrench (p/n 347-0316)
- 6” or 8” good quality adjustable wrenches for hose connections.
- Needle Nose Pliers
- Annual Service Kit p/n 345-7000
- Clean Shop Rags
- LTI Christo-Lube 111® (p/n 347-.0111) or Silicone Grease
- Intermediate Pressure Testing Gauge
4.2 ALTERNATING BI-ANNUAL SERVICE & INSPECTION PROCEDURES for the Octo-Z
It is important for the technician to understand that the Octo-Z alternates between the Bi-Annual Visual
Inspection and the Bi-Annual Service/Overhaul. On the 1st anniversary of the sale of the Octo-Z, a Visual
Inspection and Leak Test is performed (See Section 5.0). On the 2nd anniversary of the sale the Octo-Z is
disassembled, cleaned and overhauled with new service kit parts (See Section 6.0). There is a log in the
back of the Octo-Z Owner’s Manual, to keep track of which procedure is due for the regulator. If the owner
cannot remember which procedure is due and the technician has no record, then revert to the Service/
Overhaul Procedure in Section 6.0.
IMPORTANT
: The purpose of the Visual Inspection Procedure is to determine that the Octo-Z is physically
OK and is operating properly. This insures that the Octo-Z is able to give another year of good service to
the owner. During this inspection it is important to understand that ANY parts that fail due to DEFECTS
in materials or workmanship discovered during this visual inspection will be covered under the warranty.
However, if the inspection is done properly, no 345-7000 Service Kit parts will be used and therefore parts
in this Service Kit will not be replaced free of charge during the Visual Inspection Procedure, unless those
parts have FAILED due to defects in materials or workmanship.
A flat cost for the visual inspection procedure should be given to the customer before starting. It is advis-
able to establish a maximum cost point for any unexpected but needed non-warranty parts replacement that
results from the visual inspection. If this cost point is exceeded, then the customer should be notified before
proceeding.
6