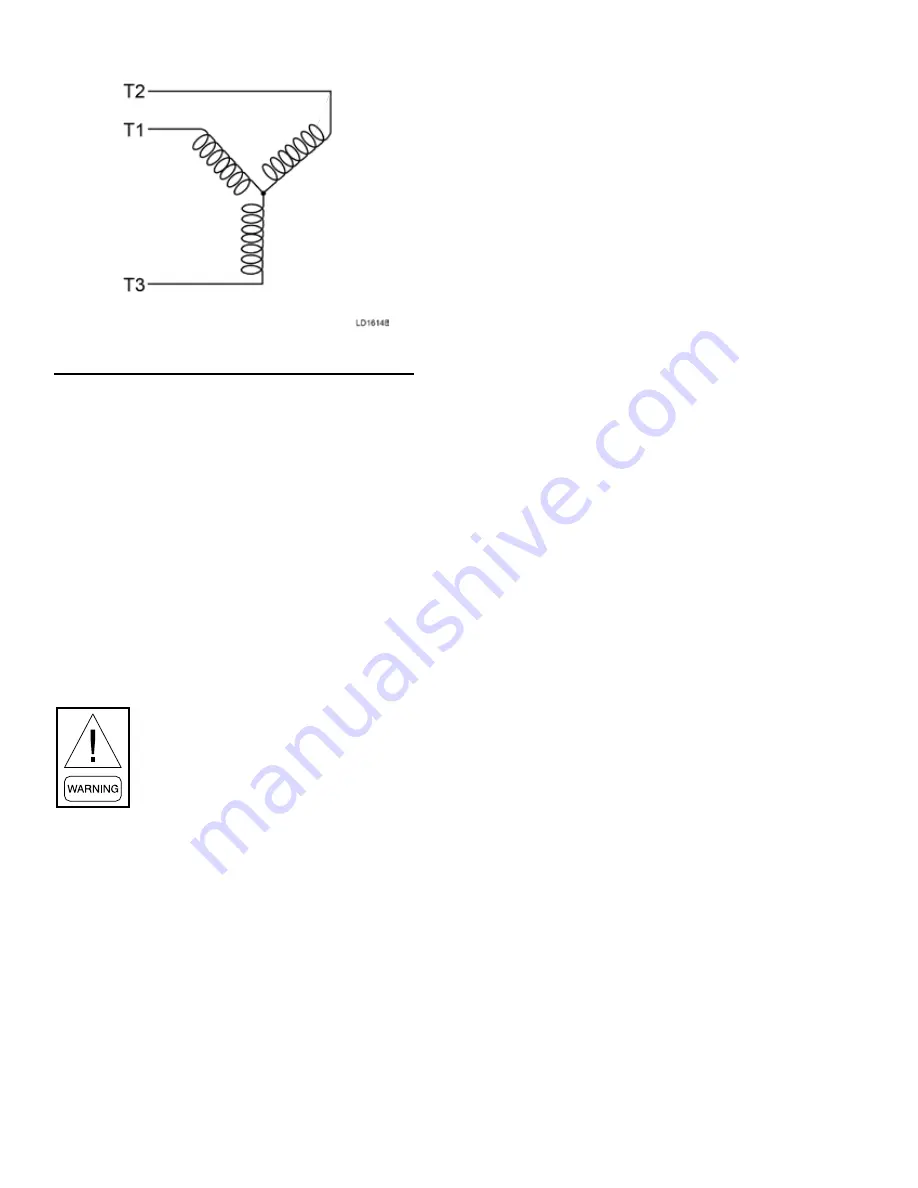
JOHNSON CONTROLS
138
FORM 201.30-ICOM1 (519)
ISSUE DATE: 05/22/2019
SECTION 7 - MAINTENANCE
FIGURE 67 -
MOTOR WINDINGS DIAGRAM
• Use a reliable battery-powered megohm tester,
which provides a consistent test voltage to test
winding resistance to ground.
• Test no greater than 500 volts.
• Always test with refrigerant or nitrogen pres-
sure in the motor.
• Never test in a vacuum.
• Values should be above 5 megohm.
• Trend readings for gross changes.
If values indicate a potential problem, remove the ex-
ternal leads from the motor, and repeat the test directly
at the motor terminals.
Never have power on the input to the
VSD, nor perform megohm testing with
the motor in a vacuum.
CHECKING SYSTEM FOR LEAKS
Leak Testing During Operation
The refrigerant side of the system is carefully pressure
tested and evacuated at the factory.
After the system is in operation under load, the high
pressure components should be carefully leak tested
with a leak detector to make sure all joints are tight. If
a leak exists, the refrigerant will be lost.
REFRIGERANT LEAK CHECKING
Check for refrigerant leaks regularly as part of a com-
prehensive maintenance program.
• Leak check the entire chiller, using a calibrated
electronic leak detector.
• If leaks are detected, use a soap solution to con-
firm leaks that were found
by the leak detector
.
• Check refrigerant relief valve piping and evapora-
tor and condenser tube rolled joints.
PRESSURE CONNECTIONS
All threaded pressure connections used on the YVWA
chillers are SAE straight thread, O-ring face seal fit-
tings or Primore Roto lock fittings.
The O-ring straight thread and face seal fittings are de-
signed and used in accordance with SAE J1926 and
J1453. When a fitting is removed, replace the O-rings.
Use only elastomeric replacement O-rings, which can
be ordered from the local Johnson Controls Field Ser-
vice Office.
Pipe sealant compounds are not required with SAE O-
ring fittings. The O-ring seal accomplishes the pressure
sealing. Lubricate the O-ring with compressor oil prior
to assembly.
All filter driers and angle shutoff valves use roto lock
fittings, which use a teflon fiber seal washer. Replace
the washers when the filter driers are changed.
If any leaks are indicated, repair them immediately.
Usually, leaks can be stopped by tightening the flare
nuts or flange bolts. However, if it is necessary to re-
pair a welded joint, the refrigerant charge must be re-
moved.
Conduct R-134a Pressure Test
With the R-134a charge removed and all known leaks
repaired, charge the system with a small amount of
R-134a mixed with dry nitrogen so that a halide torch
or electronic leak detector can be used to detect any
leaks too small to be found using the soap test.
To test with R-134a, proceed as follows:
1. With no pressure in the system, charge R-134a
gas and dry nitrogen into the system through the
charging valve to a pressure of 150 psig (10 kPa).
Содержание YVWA
Страница 14: ...JOHNSON CONTROLS 14 FORM 201 30 ICOM1 519 ISSUE DATE 05 22 2019 THIS PAGE INTENTIONALLY LEFT BLANK...
Страница 64: ...JOHNSON CONTROLS 64 FORM 201 30 ICOM1 519 ISSUE DATE 05 22 2019 THIS PAGE INTENTIONALLY LEFT BLANK...
Страница 82: ...JOHNSON CONTROLS 82 FORM 201 30 ICOM1 519 ISSUE DATE 05 22 2019 THIS PAGE INTENTIONALLY LEFT BLANK...
Страница 130: ...JOHNSON CONTROLS 130 FORM 201 30 ICOM1 519 ISSUE DATE 05 22 2019 THIS PAGE INTENTIONALLY LEFT BLANK...
Страница 146: ...JOHNSON CONTROLS 146 FORM 201 30 ICOM1 519 ISSUE DATE 05 22 2019 THIS PAGE INTENTIONALLY LEFT BLANK...
Страница 152: ...JOHNSON CONTROLS 152 FORM 201 30 ICOM1 519 ISSUE DATE 05 22 2019 THIS PAGE INTENTIONALLY LEFT BLANK...
Страница 155: ...JOHNSON CONTROLS 155 NOTES...