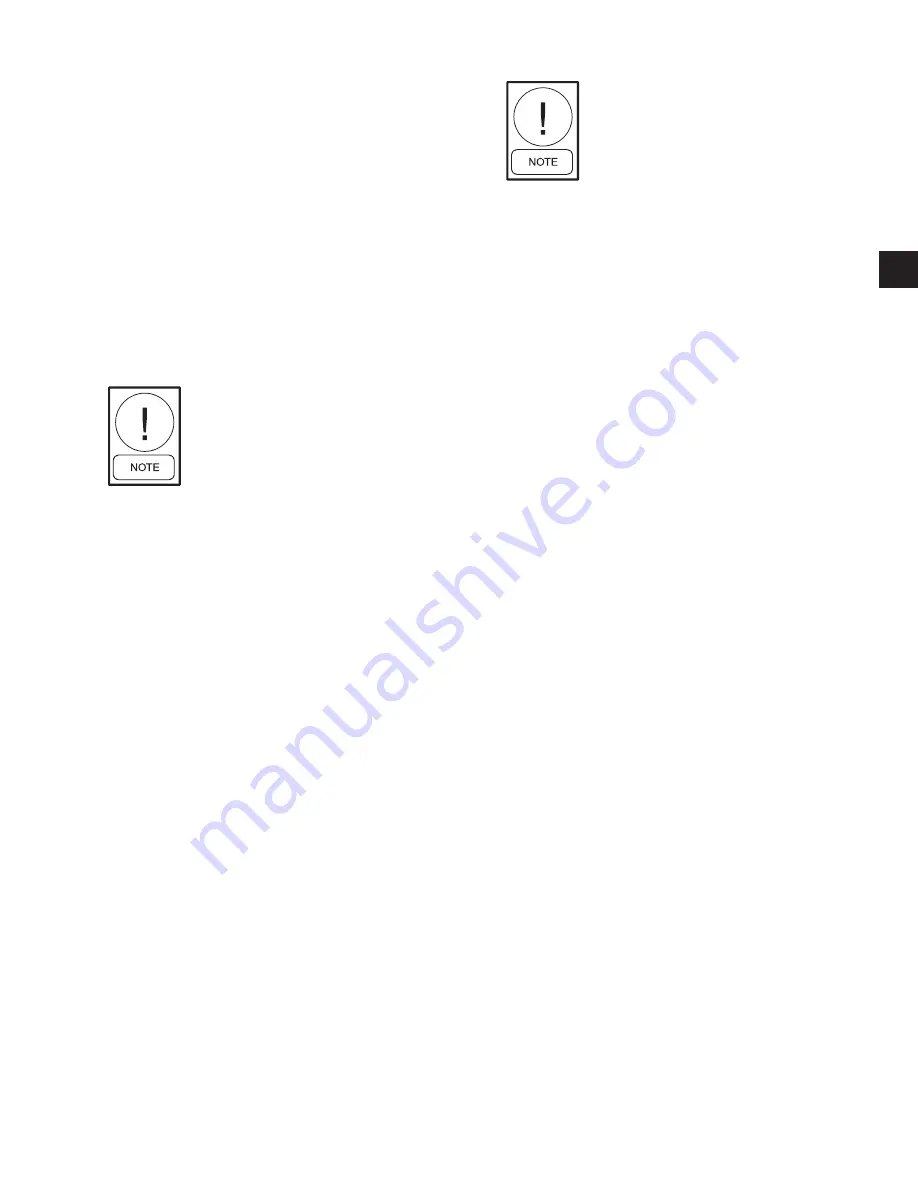
29
2
JOHNSON CONTROLS
FORM 145.05-NOM2 (807)
STATIC PRESSURE TRANSDUCER INSTALLATION
(FLEXSYS UNITS ONLY)
All FlexSys units include a factory mounted static
pressure sensor (SPS1). The unit can also have an
optional second static pressure sensor, (SPS2). The
second static pressure sensor would be used to get an
average of the static pressure in the under fl oor space.
When two static pressure sensors are used the control
can be programmed to maintain the lowest input, highest
input, or the average of the two inputs. The sensors are
factory wired and require fi eld installation of ¼” ID
sensor tubing to the selected under fl oor location. A
fi eld supplied static pressure probe and tubing must be
fi eld installed prior to the start up of the unit.
Be sure that tubing complies with local
code requirements. Flame retardant
plastic or metal tubing may be re-
quired. Carefully select the ductwork
sensing point for the pressure sensor.
Improper location of the sensing point
will result in unsatisfactory opera-
tion of the entire variable air volume
system.
Installation Instructions
1. Drill two or four holes through the unit upright
post in the vicinity of the transducer(s). Each of
the tubes should be routed through a grommet to
protect the tubing and seal the cabinet. The size
of the hole will vary based on the type of grommet
used.
2. Connect one of the tubes to the high side pressure
tap of the transducer and route the tube to the lo-
cation in the under fl oor space where you want to
maintain the specifi ed under fl oor plenum pressure.
If there is a second transducer repeat the above pro-
cedure for the second transducer selecting another
location for the second sensor.
3. Connect a second tube to low side pressure tap
of the transducer and route the tube to a location
where you want the under fl oor pressure to be refer-
enced to. This may be atmospheric or the pressure
in the condition space above the fl oor. If there is a
second transducer repeat the above procedure for
the second transducer.
To avoid confusion between “high”
and “low” tubing, it is recommended
that two different tubing colors be used
and that this information be recorded,
along with the sensing point location,
on the master building blueprints.
RETURN, OUTDOOR, SUPPLY AIR, AND MIXED AIR
SENSORS
Return Air Sensor
All units are provided with a return air sensor. The
return air sensor is connected to the Unit Control Board
and coiled up and placed in the control enclosure for
shipment.
The sensor must be mounted in a location that will give
a representative return air temperature.
Supply Air Sensor
All units are provided with a supply air sensor. The
supply air sensor is wired to the Unit Control and
mounted in the supply air section of the unit.
Mixed Air Sensor
All units are provided with a mixed air sensor. The
mixed air sensor is wired to the Unit Control and
mounted in the inlet section of the unit.
Outdoor Air Sensor
The outdoor air sensor is optional and can be ordered
with the unit. The sensor is standard when an air-side
economizer is ordered. The outside air sensor is shipped
loose in a package and is located on the fl oor of the fan
section.
The sensor must be mounted in a location that will give
a representative outdoor air temperature.
Содержание YSCD
Страница 10: ...10 JOHNSON CONTROLS FORM 145 05 NOM2 807 THIS PAGE INTENTIONALLY LEFT BLANK ...
Страница 12: ...12 JOHNSON CONTROLS FORM 145 05 NOM2 807 THIS PAGE INTENTIONALLY LEFT BLANK ...
Страница 38: ...38 JOHNSON CONTROLS FORM 145 05 NOM2 807 THIS PAGE INTENTIONALLY LEFT BLANK ...
Страница 46: ...46 JOHNSON CONTROLS FORM 145 05 NOM2 807 THIS PAGE INTENTIONALLY LEFT BLANK ...
Страница 105: ...105 JOHNSON CONTROLS FORM 145 05 NOM2 807 LD13009 8 FIG 11 WIRING DIAGRAM POWER CIRCUIT ...
Страница 106: ...106 JOHNSON CONTROLS FORM 145 05 NOM2 807 Service FIG 12 WIRING DIAGRAM MAIN CONTROL BOARD LD13010 ...
Страница 107: ...107 JOHNSON CONTROLS FORM 145 05 NOM2 807 8 FIG 13 WIRING DIAGRAM EXPANSION CONTROL BOARD LD13011 ...