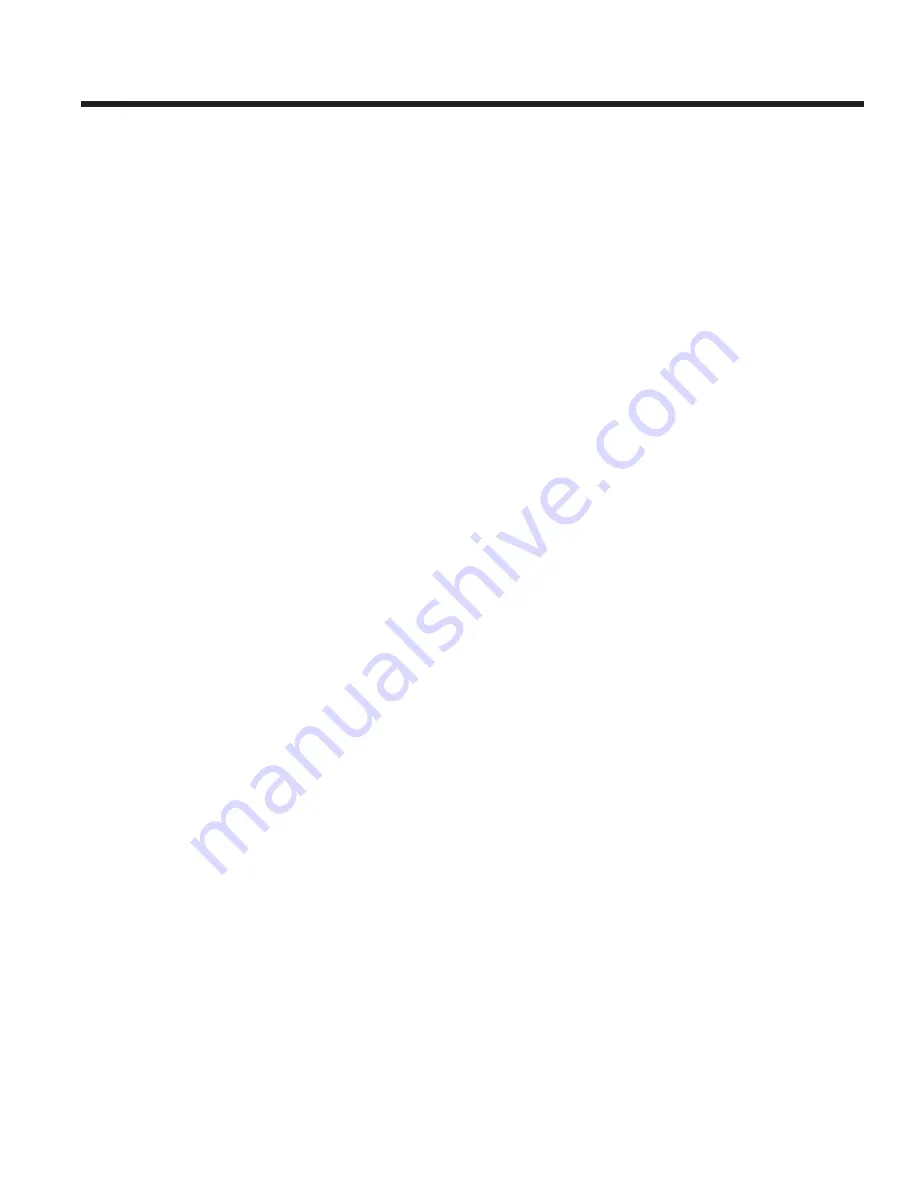
51
JOHNSON CONTROLS
FORM 160.80-EG1 (808)
All chillers shall be provided with a single oil filter hous
-
ing with isolation valves. An optional dual filter is avail
-
able which allows immediate switching from one filter
to the other, eliminating downtime during filter changes.
The off-line oil filter must be capable of being changed
during chiller operation. The chiller shall ship with a 3
micron absolute oil filter, (two filters for dual filter option)
maintaining a clean oil system and ensuring superior
compressor life.
A 1500w immersion oil heater shall be provided and
temperature actuated to effectively remove refrigerant
from the oil. power wiring to the Control Center shall be
factory installed. The oil cooler shall be refrigerant cooled
and factory piped, requiring no auxiliary water or refrig-
erant piping in the field. An oil eductor shall be provided
to automatically remove oil which may have migrated to
the evaporator and return it to the compressor. The oil
separator shall be of a horizontal design with no moving
parts, and shall provide effective oil separation before the
refrigerant enters the heat exchangers. The oil separator
shall be designed, tested and stamped in accordance
with ASMe Boiler and pressure Vessel Code, Section VIII
– Division 1 (A.D. Merkblatter or other european pressure
Vessel Code).
Motor Driveline
The compressor motor shall be an open drip-proof, squir-
rel-cage, induction type operating at 3570 RpM (2975
RpM for 50 Hz operation).
The open motor shall be provided with a D-flange, bolted
to a cast-iron adaptor mounted on the compressor to allow
the motor to be rigidly coupled to the compressor to pro-
vide factory alignment of motor and compressor shafts.
Motor drive shaft shall be directly connected to the
compressor shaft with a flexible disc coupling. Coupling
shall have all metal construction with no wearing parts
to assure long life, and no lubrication requirements to
provide low maintenance. For units utilizing remote elec-
tromechanical starters, a large steel terminal box with
gasketed front access cover shall be provided for field
connected conduit. Overload/overcurrent transformers
shall be furnished with all units. (For units furnished
with factory packaged Solid State Starters, refer to the
“Options” section.)
Evaporator
Evaporator shall be of the shell-and-tube, flooded type
designed for 300 psig (2069 Kpa) working pressure on
the refrigerant side. Shell shall be fabricated from rolled
carbon steel plate with fusion welded seams; have carbon
steel tube sheets, drilled and reamed to accommodate
the tubes; and intermediate tube supports spaced no
more than four feet apart. The refrigerant side shall be
designed, tested and stamped in accordance with ASMe
Boiler and pressure Vessel Code, Section VIII – Division
1 (A.D. Merkblatter or other european pressure Vessel
Code). when required by the refrigeration safety code,
the vessel shall have a refrigerant relief device(s) set at
300 psig (2069 KPa). Tubes shall be high-efficiency, inter
-
nally enhanced type. each tube shall be roller expanded
into the tube sheets providing a leak-proof seal, and be
individually replaceable. water velocity through the tubes
shall not exceed 12 FpS (3.6 m/s). Liquid level sight glass
shall be located on the side of the shell to aid in determin-
ing proper refrigerant charge.
water boxes shall be removable to permit tube clean-
ing and replacement. Stubout water connections having
ANSI/AwwA C-606 grooves shall be provided. water
boxes shall be designed for 150 psig (1034 Kpa) design
working pressure and be tested at 225 psig (1551 Kpa).
Vent and drain connections with plugs shall be provided
on each water box.
Condenser
Condenser shall be of the shell-and-tube type, designed
for 300 psig (2069 Kpa) working pressure on the refriger-
ant side. Shell shall be fabricated from rolled carbon steel
plate with fusion welded seams; have carbon steel tube
sheets, drilled and reamed to accommodate the tubes;
and intermediate tube supports spaced no more than four
feet apart. A refrigerant subcooler shall be provided for
improved cycle efficiency. The refrigerant side shall be
designed, tested and stamped in accordance with ASMe
Boiler and pressure Vessel Code, Section VIII – Division
1 (A.D. Merkblatter or other european pressure Vessel
Code). when required by the refrigeration safety code,
the vessel shall have a refrigerant relief device(s) set at
300 psig (2069 KPa). Tubes shall be high-efficiency, inter
-
nally enhanced type. each tube shall be roller expanded
into the tube sheets providing a leak-proof seal, and be
individually replaceable. water velocity through the tubes
shall not exceed 12 FpS.
water boxes shall be removable to permit tube clean-
ing and replacement. Stubout water connections having