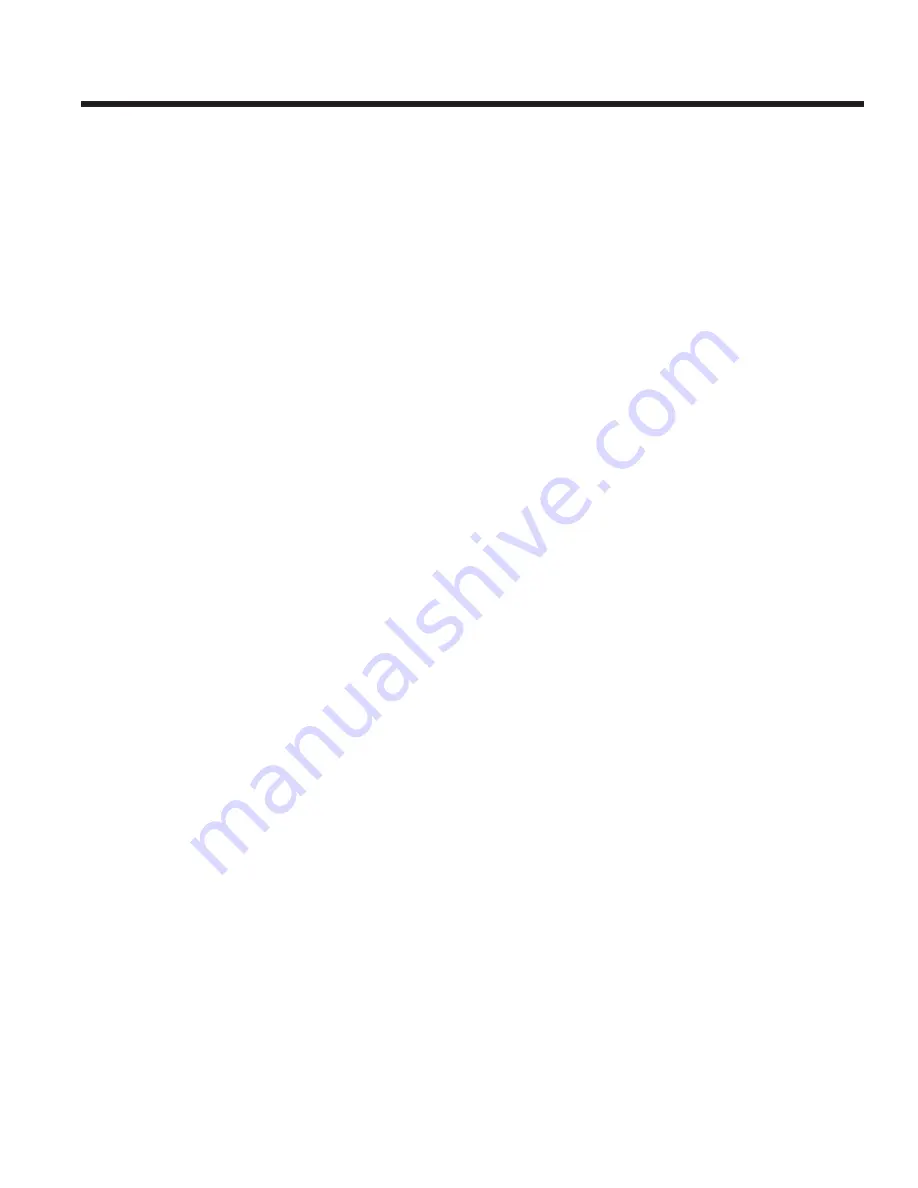
1
JOHNSON CONTROLS
FORM 160.80-EG1 (808)
Mechanical Specifications
STANDARD UNIT
General
The YORK Millennium YS Rotary Screw Chiller is com-
pletely factory-packaged, including evaporator, condenser,
sub-cooler, oil separator, compressor, motor, lubrication
system, control center and refrigerant isolation valves.
The factory package consists of a “leak tight” design. All
units ship as standard with a full charge of refrigerant
and oil. Units can also be shipped in sections (optional)
to accommodate job site requirements.
The services of a Johnson Controls factory-trained, field
service representative are incurred to supervise or perform
the final leak testing, charging, the initial start-up, and
concurrent operator instructions.
Compressor
The Frick Rotary Twin Screw Compressor is engineered
and constructed to meet the exact requirements of the
industrial refrigeration market. It utilizes state-of-the-art
technology to provide the most reliable and energy-ef-
ficient compressor available at all operating conditions.
The compressor operates at 3750 RpM for 60 Hertz and
2975 RpM for 50 Hertz. The compressor housing is made
of cast iron, precision-machined to provide minimal clear-
ance for the rotors. Compressor housing has a design
working pressure (Dwp) of 300 pSIG (2068 kpa) mini-
mum, and hydro-tested at 544 pSIG (3751 kpa).
The rotors are manufactured from forged steel and use
asymmetric profiles. The compressor incorporates a
complete anti-friction bearing design for reduced power
and increased reliability. Four separate cylindrical roller
bearings handle radial loads. Two 4-point angular contact
ball bearings handle axial loads. Together, they maintain
accurate rotor positioning at all pressure ratios, thereby
minimizing blow-by and maintaining efficiency.
A check valve is installed in the compressor discharge
housing (suction housing for S4 and S5 compressor) to
prevent compressor rotor back spin because of system
refrigerant pressure gradients during shutdown.
The open-drive compressor shaft seal consists of preci-
sion ceramic seal faces, metallic bellows, rotating member,
PTFE ‘C’-Ring static seal, and multi-port oil injection ring.
The seal cavity is maintained at intermediate pressure
with its oil discharged to the oil drain from the compressor.
Combining intermediate pressure with direct oil injection
provides cool, non-foaming lubricant to the seal assuring
a longer lifespan.
Capacity Control
Capacity control is achieved by use of a slide valve which
provides fully modulating capacity control from 100% to
10% of full load. The slide valve is actuated by oil pressure,
controlled by external solenoid valves via the OptiView
Control Center.
Oil Separator
The oil separator is a horizontal design without moving
parts. effective oil separation is achieved by gravity drop-
out of oil from the refrigerant gas as velocity decreases
upon entering the separator, and by mesh pads to provide
final gas/oil separation before gas enters the condenser.
The oil separator is designed for 345 pSIG (2378 kpa)
design working pressure, tested at 517 pSIG (3565 kpa),
and stamped in accordance with ASMe Boiler and pres-
sure Vessel Code, Section VIII - Division 1.
each vessel has a refrigerant relief device(s) set at 300
pSIG (2068 kpa). In addition to the spring-loaded, re-seat-
ing-type relief valves sized for pressure vessel volume,
each unit is equipped with a rupture disk. This rupture
disk is able to relieve the entire pumping capacity of the
compressor if electronic safeties fail, providing protec-
tion for property and personnel. This device is set for
345 pSIG (2378 kpa). Alternatively, the shell side may
be designed to european pressure Vessel Codes and
stamped in accordance with A.D. Merkblatter or other
european pressure Vessel design code. when required
by the refrigeration safety code, each vessel has a dual
refrigerant relief device(s).
Lubrication
The main unit oil reservoir is located in the oil separator.
The compressor also has an oil reservoir located at the
rotor bearings to provide lubrication during start-up, coat
down, and in the event of a power failure. During opera-
tion, system pressure differential provides proper oil flow
without the need of an auxiliary oil pump. This minimizes
energy consumption.
The chiller is shipped with a 3 Micron absolute oil filter,
ensuring a clean oil system and superior compressor
life. An external, replaceable cartridge oil filter is supplied
with manual isolation stop valves for ease of servicing.
An optional dual oil filter housing with isolation valves is
available on all units. This allows immediate switching
from one filter to the other, eliminating downtime during
filter changes. The off-line oil filter can be changed during
chiller operation.
A 500 watt (115 volt - 1-phase - 60/50Hz) immersion
oil heater is located in the oil separator reservoir, tem-
perature actuated to efficiently remove refrigerant from
the oil. Oil heater power supply is factory wired from
the control panel. A factory-piped refrigerant-cooled oil