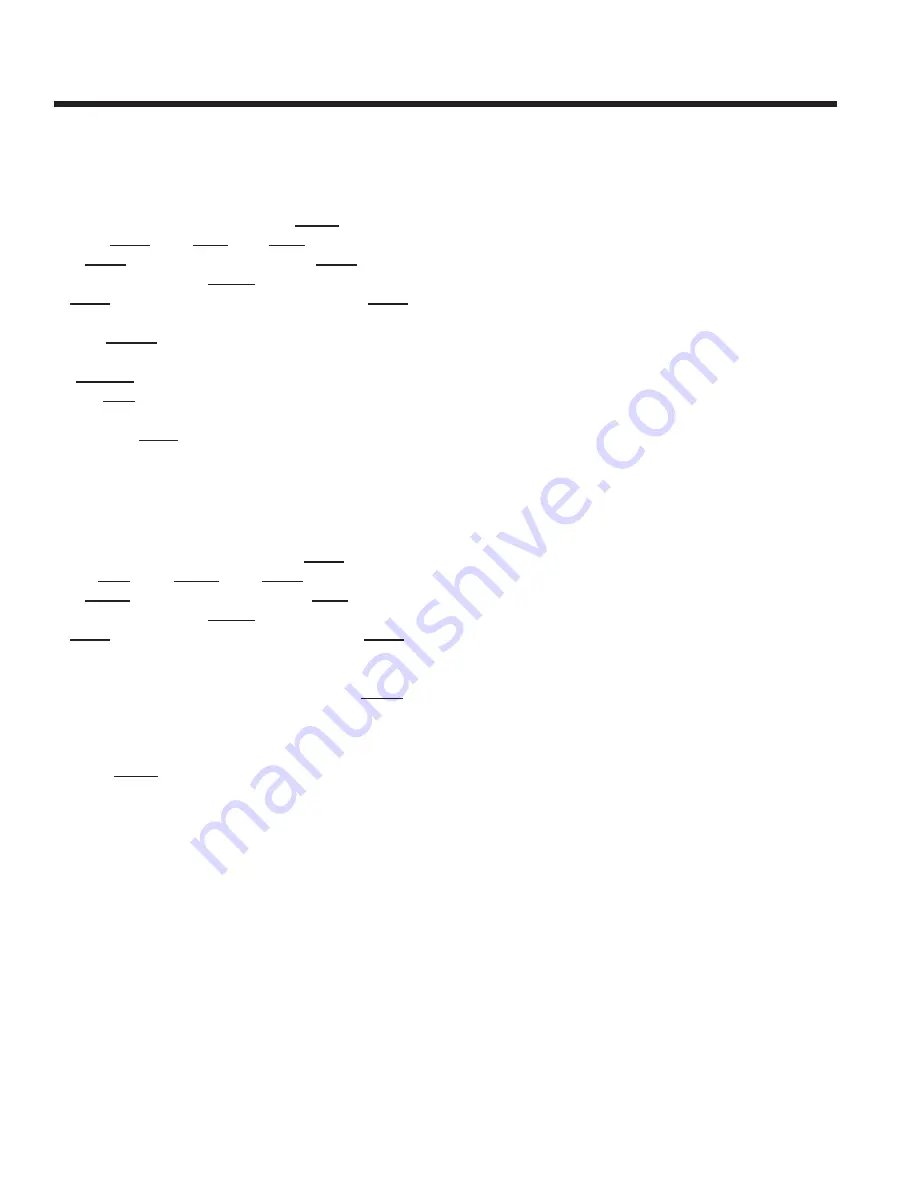
50
JOHNSON CONTROLS
GENERAL
Furnish and install where indicated on the drawings
YORK
Millennium
Rotary Screw Liquid Chilling Units(s).
each unit shall produce a capacity of tons, cooling
GpM of from °F to °F when supplied
with GpM of condenser water at °F. power
input shall not exceed kw with an IpLV (ApLV)
of . The evaporator shall be selected for ft
2
°F hr/BTU fouling factor and a maximum liquid pressure
drop of ft. water side shall be designed for 150
psig working pressure. The condenser shall be selected
for fouling factor and maximum liquid pressure
drop of ft. water side shall be designed for 150 psig
working pressure. power shall be supplied to the compres-
sor motor at volts – 3-phase – (60)(50) Hertz and
controls at 115 volts –1-phase – (60)(50) Hertz.
– (or) –
Furnish and install where indicated on the drawings
YORK
Millennium
Rotary Screw Liquid Chilling Units(s).
each unit shall produce a capacity of kw, cooling
L/S of from °C to °C when supplied
with L/S of condenser water at °C. power
input shall not exceed kw with an IpLV (ApLV)
of . The evaporator shall be selected for M
2
°C/w fouling factor and a maximum liquid pressure drop of
kpa. water side shall be designed for 1034 kpa working
pressure. The condenser shall be selected for M
2
°C/w fouling factor and maximum liquid pressure drop of
kpa. water side shall be designed for 1034 kpa working
pressure. power shall be supplied to the compressor
motor at volts – 3-phase – 50 Hertz and controls
at 115 volts – 1-phase – 50 Hertz.
Performance shall be certified or rated in accordance with
the latest edition of ARI Standard 550/590-98 as appli-
cable. Only chillers that are listed in the ARI Certification
program for water Chilling packages using the vapor
compression cycle are acceptable.
each unit shall be completely factory packaged including
evaporator, condenser, subcooler, oil separator, compres-
sor, open motor, lubrication system, OptiView Control
Center, Solid State Starter, refrigerant isolation valves
and all interconnecting piping and wiring. The factory
package shall consist of a “Leaktight” design, with no pipe
thread connections that can loosen and leak over time. All
Guide Specifications
units shall ship with a full charge of refrigerant (HCFC-22
or HFC-134a) and oil. (Alternatively, the chiller shall be
shipped with the compressor, control panel and oil sepa-
rator removed (Form 3) or also with the shells separated
(Form 7) to allow rigging into the equipment room. All units
that ship disassembled shall be assembled and factory
run tested prior to disassembly and shipment).
Compressor
The compressor shall be an open-drive, rotary-screw type.
The compressor housing shall be of cast iron, precision
machined to provide minimal clearance for the rotors. The
rotors shall be manufactured from forged steel and use
asymmetric profiles operating at a maximum speed of
(3570 RpM/60 Hz) (2975 RpM/50 Hz). The compressor
shall incorporate a complete anti-friction bearing design
to reduce power and increase reliability; four separate
cylindrical roller bearings to handle radial loads; and two
4-point angular contact ball bearings to handle axial loads.
A spring actuated positive seating check valve shall be
incorporated in the compressor housing to prevent rotor
backspin during shutdown. The open-drive compres-
sor shaft seal consists of a bellows-type spring loaded
precision lapped ceramic ring, Teflon
®
static seal, and a
precision lapped ceramic rotating collar. The seal cavity is
maintained at intermediate pressure with its oil discharged
to the oil drain from the compressor. Combining intermedi-
ate pressure with direct oil injection provides cool, non-
foaming lubricant to the seal which assures a long life.
Capacity control shall be achieved by use of a slide valve
to provide fully modulating control from 100% to 10% of
full load. The slide valve shall be actuated by oil pres-
sure, controlled by external solenoid valves through the
OptiView Control Center. The unit shall be capable of
operating with lower temperature cooling tower water dur-
ing part-load operation in accordance with ARI Standard
550/590. If the unit can not operate at the minimum load,
the manufacturer shall provide a hot-gas-bypass system
to allow operation at 10% load, and advise the minimum
load and power input of the unit at the point hot-gas-by-
pass is actuated.
Lubrication System
An adequate supply of oil shall be available to the com-
pressor at all times. During start-up and coastdown, this
shall be achieved by oil reservoirs in the compressor.
During operation, oil shall be delivered by positive system
pressure differential.