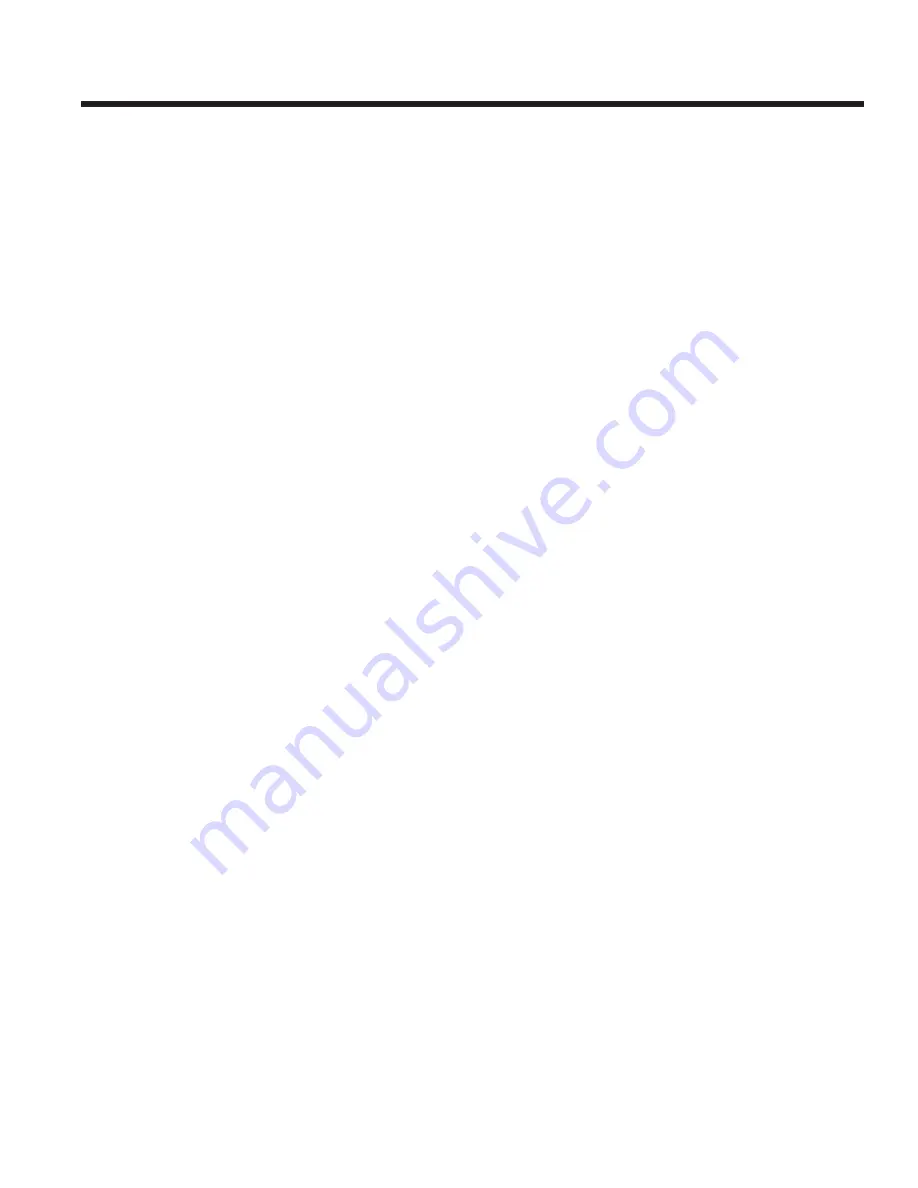
FORM 155.19-EG3 (1011)
21
JOHNSON CONTROLS
from the unit during operation using an eductor. Non-
condensibles shall be stored in a purge chamber until they
can be removed through the use of a purge pump.
The Control Panel shall include a Smart-Purge system that
will automatically sense the amount of non-condensibles
in the purge chamber and empty the tank whenever neces
-
sary. The SmartPurge system shall eliminate the need for
an operator to ever manually empty the purge chamber.
In addition, the control panel shall monitor the frequency
of purge cycles and alert the chiller operator, through a
unique control panel warning message, if the number of
purges exceeds normal levels.
Purge systems that utilize a palladium cell (for venting hy
-
drogen) on the purge chamber to prolong the time between
emptying the purge chamber shall not be acceptable,
since the vented hydrogen is the major byproduct of the
corrosion caused by a leak. If a system with a palladium
cell is offered, the purchase price must include a contract
for quarterly leak checking of the machine.
The purge pump shall be of an oil, rotary, two-stage de
-
sign. It shall be furnished complete with a 1/3 HP, 3 Phase,
ODP motor, and all required accessories including base,
pulleys, and belt guard. Purge pump shall be equipped
with stainless steel vanes.
LITHIUM‑BROMIDE AND REFRIGERANT CHARGE
The LiBr solution shall contain a corrosion in hibitor addi
-
tive, lithium-molybdate, to minimize the rate of copper and
ferrous metal corrosion on the solution side of the unit.
The corrosion inhibitor, when applied at the concentra
-
tions prescribed by the unit manufacturer, shall not cause
the inhibited lithium-bromide solution to be classified as
a hazardous waste under the Resource Conservation
and Recovery Act. Lithium-bromide solu tions containing
chromates or arsenites as corrosion inhibitors shall not be
acceptable. If systems are bid that include LiBr solutions
containing chromate or arsenate inhibitors, the purchase
price shall include a contract supplying disposal services
for removal of bromide as a result of regular service or
when the machine is being taken out of commission.
STEAM VALVE
Chiller-heater shall be furnished with a steam control
valve, linkage, and actuator motor. This assembly shall
be shipped loose for installation by others. Valve/link age/
actuator motor assembly to be sized by the unit manu
-
facturer in accordance with the specified steam pressure
and flow requirements.
The steam valve shall be a cage type valve incorporat ing
a carbon steel body and a teflon seat. Valve/link age/actua
-
tor motor assembly shall be capable of modu lating steam
flow in a linear fashion from 20% to 100% of maximum
design chiller steam input. Valve shall be equipped with
150 lb ANSI flanged connections.
The actuator motor shall be 120V/1 Ph/60Hz, and shall be
powered from the chiller’s microcomputer control panel.
The MicroComputer Control Center shall communicate
the valve position via a 4-20 mA signal.
UNIT CONTROLS
Each unit shall be furnished complete with a factory
mounted and prewired control system. Unit controls to
be furnished shall include a total of two (2) enclosures:
a Power Panel, and an MicroComputer Control Center
Panel.
Power Panel
– The Power Panel enclosure shall be
NEMA 1 and shall house the following components:
single-point wiring connection for incoming power sup ply;
non-fused disconnect switch; motor starters, com plete
with current and thermal protection, for solution pump, re
-
frigerant pump, and purge pump (current over loads only);
and a 115VAC 50/60 Hz Control Power Transformer.
MicroComputer Control Center Panel
– The Micro
-
Computer Control Center enclosure shall be NEMA 1 and
be equipped with hinged access door with lock and key.
All temperature sensors, pressure transducers, and other
control devices necessary to sense unit op erating param
-
eters to be factory-mounted and wired to panel. The ISN
Two-Stage Control Center Panel shall include a 40 char
-
acter alphanumeric display showing all system parameters
in the English language with nu meric data in English (or
metric) units (°F, PSIA or °C, KPa respectively).
The 115V/1
∅
control voltage will be supplied through
a 1 KVA power transformer located in the Power Panel
and will be factory wired to the MicroComputer Control
Center Panel.
Terminal blocks will be provided for all external safety and
control interlocks.
The operating program shall be stored in non-volatile
memory (EPROM) to eliminate chiller failure due to AC
power failure/battery discharge. In addition, pro grammed
setpoints shall be retained in lithium battery- backed RTC
memory for a minimum of 5 years.
All wiring and control interlocks between the MicroCom
-
puter Control Center Panel and the Burner Control
Panel shall be factory installed and tested prior to unit
shipment.
System Operating Information
– During normal opera
-
tion the following operating parameters shall be acces sible