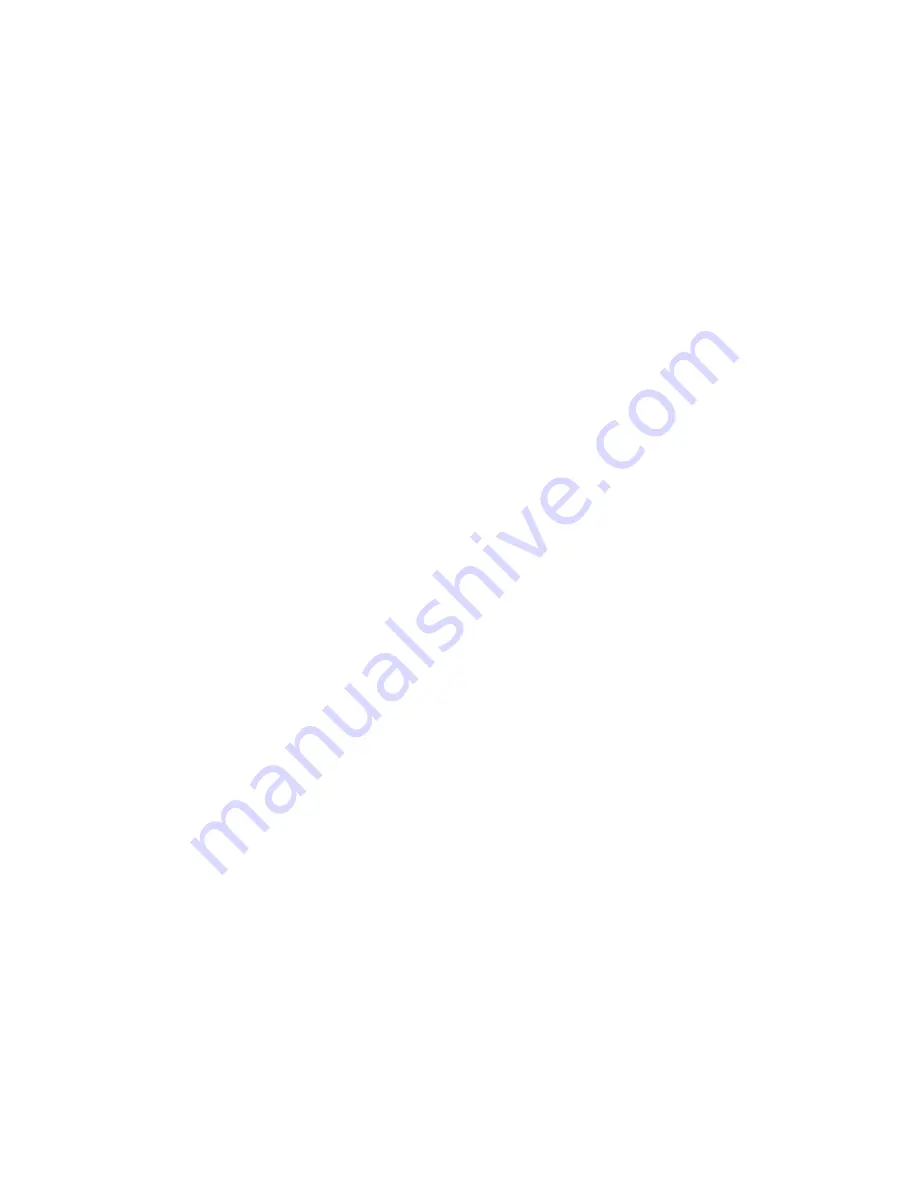
11
JOHNSON CONTROLS
FORM 150.68-ICOM1
ISSUE DATE: 10/15/2020
PRODUCT DESCRIPTION
compressors are mounted on isolator pads to reduce
transmission of vibration to the rest of the unit.
The motor terminal boxes have IP54 weather protection.
REFRIGERANT CIRCUITS
Two independent refrigerant circuits are provided on
each unit. Each circuit uses copper refrigerant pipe
formed on computer controlled bending machines to
reduce the number of brazed joints resulting in a high
integrity and reliable system.
Each circuit shall incorporate all components necessary
for the designed operation including: a suction
accumulator, a liquid receiver, a four way reversing
valve, service valves, isolation (ball/angle) valves,
pressure relief valves, a high absorption removable
core filter-drier, a sight glass with moisture indicator,
and an electronic expansion valve. Suction lines shall
be covered with closed-cell insulation.
REFRIGERANT TO WATER HEAT EXCHANGER
The 2-pass dual circuit shell and tube type direct
expansion (DX) heat exchanger has refrigerant in the
tubes and liquid flowing through the baffled shell. The
waterside (shell) design working pressure is 150 psig.
The refrigerant side (tubes) design working pressure is
650 psig. The refrigerant side is protected by pressure
relief valve(s).
The heat exchanger is equipped with a heater for frost
protection to -4°F (below this the ball valve in the
discharge line must be closed) and insulated with flexible
closed-cell foam.
Water connection to the heat exchanger is via victaulic
grooved connections. Victaulic groove to flange
converters are available as an option.
AMBIENT COILS
The ambient coils are seamless copper tubes, arranged
in staggered rows, mechanically expanded into coated
aluminium fins. Integral sub-cooling is included.
The ambient coil fans are designed for maximum
efficiency and statically and dynamically balanced
for vibration free operation. They are directly driven
by independent motors, and positioned for vertical air
discharge. The fan guards are constructed from heavy-
gauge, corrosion resistant, coated steel.
INTRODUCTION
YLPA air-to-liquid heat pumps are completely factory
assembled with all interconnecting refrigerant piping and
wiring ready for field installation. The unit is pressure
tested, evacuated, and fully factory charged with
refrigerant R-410A and oil in each of the independent
refrigerant circuits. After assembly, an operational
test is performed with water flowing through the heat
exchanger to ensure that each refrigerant circuit operates
correctly.
The unit structure is manufactured from heavy-gauge,
galvanized steel coated with baked-on powder paint
(Champagne (RAL 7006, Munsell No. 9.8YR4.36/1.2)).
YLPA units are designed and manufactured within an
EN ISO 9001 accredited organization and in conformity
with the following Standards and Codes:
• ANSI/ASHRAE Standard 15, Safety Code for
Mechanical Refrigeration.
• ANSI/NFPA Standard 70, National Electrical Code
(N.E.C.).
• ASME Boiler and Pressure Vessel Code, Section VIII
Division 1.
• ARI Standard 550/590-98, Water Chilling Packages
Using the Vapor Compression Cycle.
• ASHRAE 90.1 Energy Standard for Building Except
Low-Rise Residential Buildings.
• ARI 370 Sound Rating of Large Outdoor Refrigeration
and Air Conditioning Equipment.
In addition, the chillers conform to Underwriters
Laboratories (U.L.) for construction of chillers and
provide U.L./cU.L. Listing Label.
COMPRESSORS
The YLPA unit has suction-cooled, hermetic scroll
compressors. High efficiency is achieved through a
controlled orbit and the use of advanced scroll geometry.
The compressors incorporate a compliant scroll design
in both the axial and radial directions. All rotating parts
are statically and dynamically balanced. The compressor
motors have integral protection against overloads that
will automatically reset. Starting is direct on line, and
soft start is available as an option.
The compressors are switched On and Off by the unit
microprocessor to provide capacity control. Each
compressor is fitted with a crankcase strap heater. All
Содержание YLPA 0115SE
Страница 4: ...4 JOHNSON CONTROLS FORM 150 68 ICOM1 ISSUE DATE 10 15 2020 Page Left Intentionally Blank ...
Страница 10: ...10 JOHNSON CONTROLS FORM 150 68 ICOM1 ISSUE DATE 10 15 2020 Page Left Intentionally Blank ...
Страница 16: ...16 JOHNSON CONTROLS FORM 150 68 ICOM1 ISSUE DATE 10 15 2020 Page Left Intentionally Blank ...
Страница 26: ...26 JOHNSON CONTROLS FORM 150 68 ICOM1 ISSUE DATE 10 15 2020 Page Left Intentionally Blank ...
Страница 30: ...30 JOHNSON CONTROLS FORM 150 68 ICOM1 ISSUE DATE 10 15 2020 Page Left Intentionally Blank ...
Страница 72: ...72 JOHNSON CONTROLS FORM 150 68 ICOM1 ISSUE DATE 10 15 2020 Page Left Intentionally Blank ...
Страница 79: ...79 JOHNSON CONTROLS FORM 150 68 ICOM1 ISSUE DATE 10 15 2020 YLPA P I Diagram ...
Страница 86: ...86 JOHNSON CONTROLS FORM 150 68 ICOM1 ISSUE DATE 10 15 2020 Page Left Intentionally Blank ...
Страница 88: ...88 JOHNSON CONTROLS FORM 150 68 ICOM1 ISSUE DATE 10 15 2020 Page Left Intentionally Blank ...