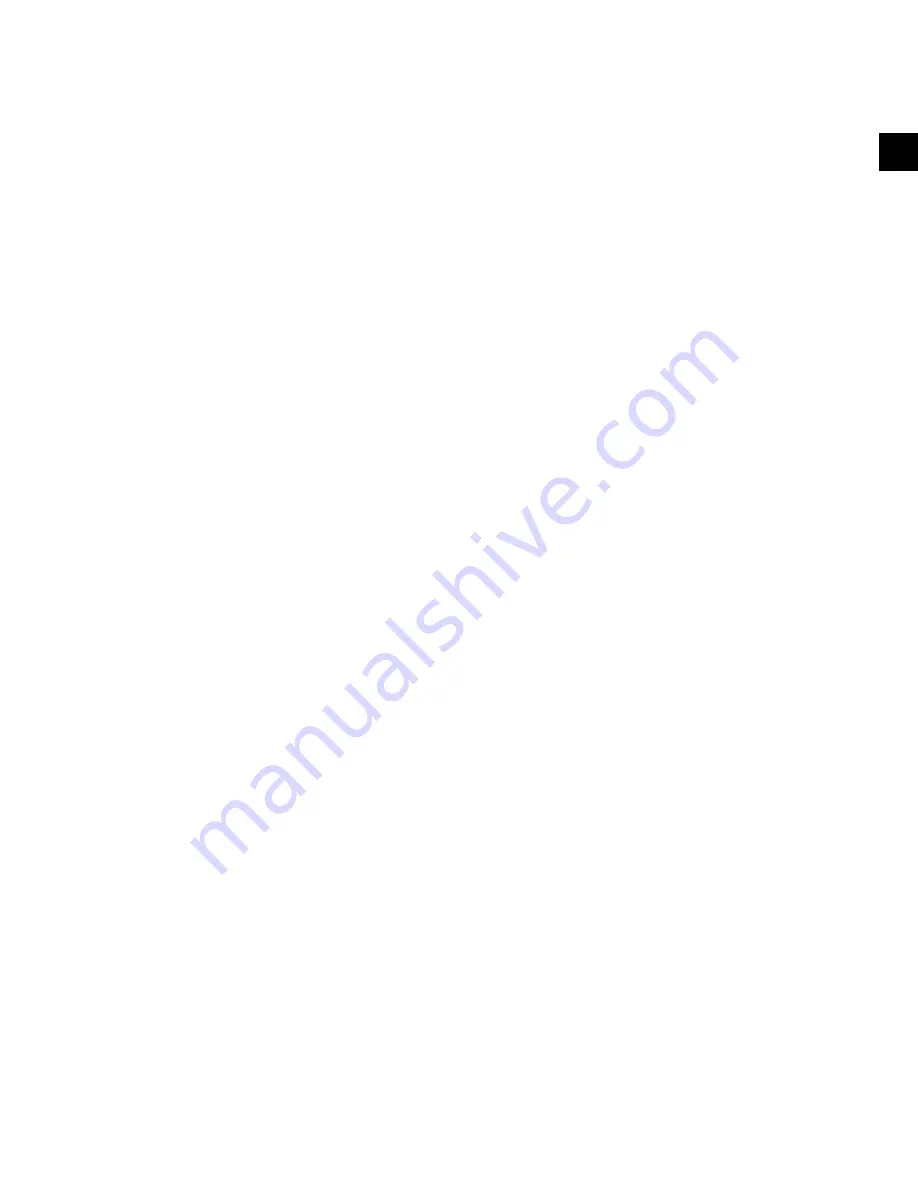
JOHNSON CONTROLS
125
SECTION 2 – OPTIVIEW CONTROL CENTER
FORM 160.69-O1
ISSUE DATE: 9/30/2012
2
compressor (using the Lockout key on the Capacity
Compressor Cycling Screen) this fault does not cause
the other compressor to shutdown or prevent it from
starting. It is displayed as a warning. This allows the
user to know that a fault exists on the locked compres-
sor. The condition must be corrected prior to the lock-
out being removed from the compressor. If it is not, the
warning condition will revert back to a cycling shut-
down as soon as the lockout is removed and will cause
the chiller to trip.
“DISCHARGE #1 – VALVE NOT CLOSED”
The chiller (both compressors) has shutdown be-
cause compressor #1 Discharge Valve did not fully
close (as indicated by the closure of the valve closed
end switch) within 40 seconds of receiving the close
command. If the chiller was running when this oc-
curred, the Pre-rotation vanes of the running compres-
sors are driven fully closed prior to shutting down the
chiller. The chiller will be allowed to restart when the
valve closed end switch closes. With software version
C.OPT.11.03.01.004 (or later), the end switch position
is not considered valid until it has been in the position
continuously for at least 3 seconds. This prevents the
possibility of initiating a fault due to switch bounce.
“DISCHARGE #2 – VALVE NOT CLOSED”
The chiller (both compressors) has shutdown be-
cause compressor #2 Discharge Valve did not fully
close (as indicated by the closure of the valve closed
end switch) within 40 seconds of receiving the close
command. If the chiller was running when this oc-
curred, the Pre-rotation vanes of the running compres-
sors are driven fully closed prior to shutting down the
chiller. The chiller will be allowed to restart when the
valve closed end switch closes. With software version
C.OPT.11.03.01.004 (or later), the end switch position
is not considered valid until it has been in the position
continuously for at least 3 seconds. This prevents the
possibility of initiating a fault due to switch bounce.
“EXPANSION I/O – SERIAL COMMUNICA-
TIONS”
The chiller (both compressors) has shutdown because
the serial communications from the I/O Boards to the
Microboard has been lost for 20 continuous seconds.
The chiller can restart when the serial communications
have been restored.
“OIL – LOW TEMPERATURE DIFFERENTIAL”
The chiller (both compressors) is prevented from start-
ing for one of the following reasons. The chiller will
automatically restart when the conditions have been
satisfied.
The chiller has been shut down for <30 minutes and
the oil temperature minus the condenser saturation
temperature is <30°F.
-OR-
The chiller has been shut down for > 30 minutes and
the oil temperature minus the condenser saturation
temperature is < 40°F.
-OR-
Following a Power failure, upon restoration of power,
the oil temperature minus the condenser saturation
temperature is < 40°F.
“OIL – LOW TEMPERATURE”
The oil temperature has decreased to < 55°F. The
chiller will automatically restart when the temperature
increases to > 55.0°F and is greater than the Condens-
er Saturated temperature by 30 or 40°F, as described
above in the "OIL – LOW TEMPERATURE DIFFER-
ENTIAL" message description.
“CONTROL PANEL – POWER FAILURE”
A Control Power failure has occurred. If the power
failure occurred while the chiller was running, it will
automatically restart when power is restored. How-
ever, if the power failure duration was < the duration
of the “Coastdown” period when power is restored,
the remainder of the “Coastdown” will be performed,
prior to the chiller starting. This message can indicate
a Cycling (auto-restart after power failure) or Safety
(manual restart after power failure) shutdown, depend-
ing upon Control Center configuration. It indicates a
cycling shutdown when displayed in orange charac-
ters; Safety shutdown when displayed in red charac-
ters. The Control Center is configured for auto-restart
or manual restart after power failure by a qualified Ser-
vice Technician following instructions in YORK Ser-
vice Manual 160.69-M1.