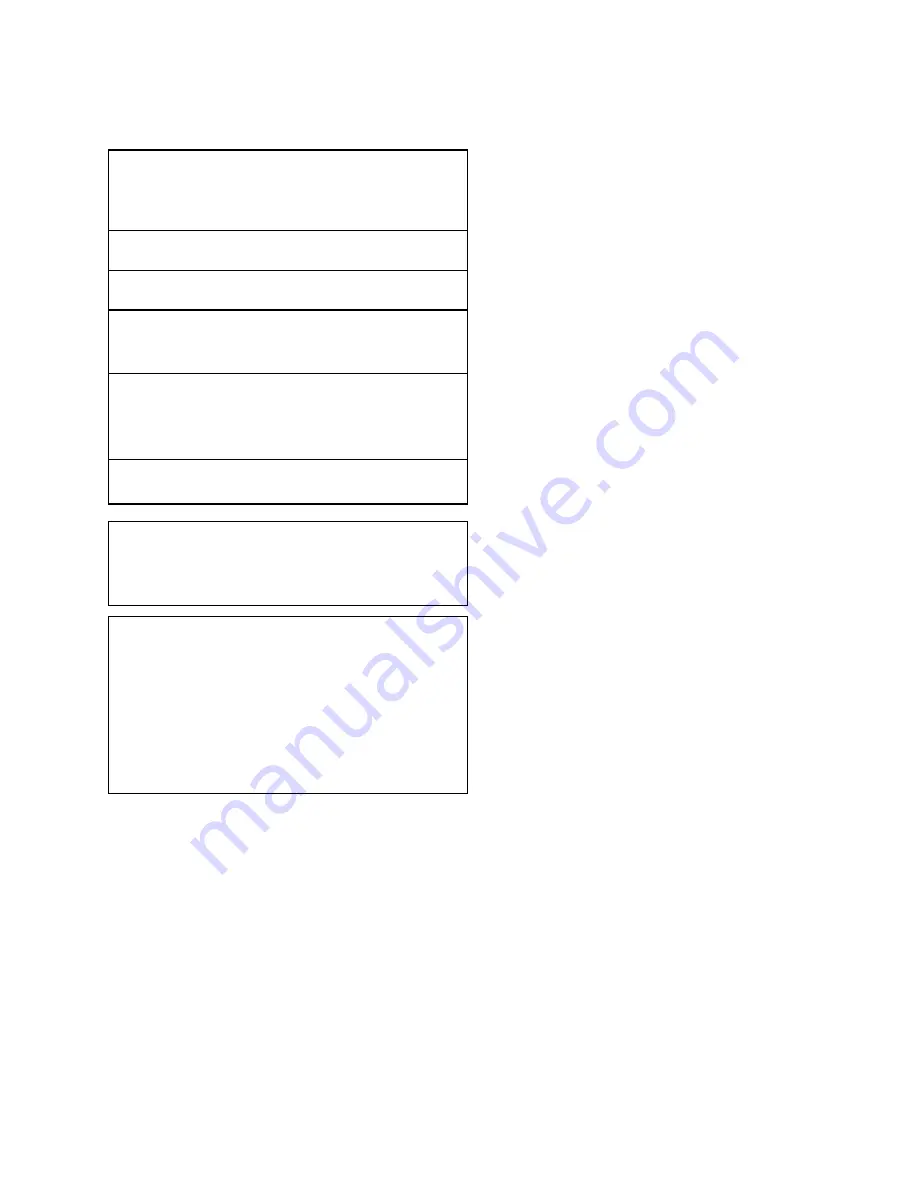
FORM 150.60-NM3
69
YORK INTERNATIONAL
Unit Checks
*
1. Inspect the unit for shipping or installation dam-
age.
*
2. Assure that all piping has been completed.
*
3. Check that the unit is properly charged and that
there are no piping leaks.
*
4. Suction and discharge stop valves and the re-
frigerant liquid stop valves are open (ccw).
CAUTION: Compressor lubrication circuit must be
primed with YORK “C” oil prior to start-up.
Priming should be done through the
Schrader fitting at the compressor oil pump.
Stroke oil pump 10 times to prime the lubri-
cation circuit.
*
5. The compressor oil level of J compressors
must be maintained between the middle of the
upper and middle of the lower sight glass at all
operating conditions. At part load operating con-
ditions, it is not abnormal for the oil level to be in
the lower sight glass. Z compressors should
maintain oil level in the sight glass under all op-
erating conditions. If it is necessary to add oil,
connect a YORK oil pump to the oil charging
valve, but do not tighten the flare nut on the deliv-
ery tubing. With the bottom (suction end) of the
pump submerged in oil to avoid the entrance of
air, operate the pump until oil drips from the flare
nut joint, allowing the air to be expelled, and
tighten the flare nut. Open the compressor oil
charging valve and pump in oil until the oil
reaches the proper level as described above.
Close the compressor oil charging valve.
*
6. Assure water pumps are on. Check and adjust
water pump flow rate and pressure drop across
cooler.
*
7. Check panel to see that it is free of foreign mate-
rial (wires, metal chips, etc.).
*
8. Visually inspect wiring (power & control). Must
meet NEC and all local codes. (See Figs. 9 &
11)
*
9. Check for proper size fuses in main and control
power circuits.
*
10. Verify that field wiring matches the 3-phase
power requirements of the compressor. See
nameplate. (See Fig. 9)
*
11. Assure 115VAC Control Power to TB1 has 30A
minimum capacity. (See Fig. 9)
*
12. Be certain all control bulbs are inserted com-
pletely in their respective wells and are coated
with heat conductive compound.
PANEL CHECKS
(POWER ON-BOTH SYSTEM SWITCHES OFF)
*
1. Apply 3-phase power and verify its value. (See
Fig. 9)
*
2. Apply 115VAC and verify its value on the termi-
nal block in the lower left of the Power Panel.
Make the measurement between terminals 5
and 2. Should be 115VAC ±10%. (See Fig. 9).
*
3. Assure crankcase heaters are on. Allow crank-
case heaters to remain on a minimum of 24
hours before start-up. This is important to as-
sure no refrigerant is in the oil at start-up!
SYSTEM START-UP CHECKLIST
CHECKING THE SYSTEM 24 HOURS PRIOR TO
INITIAL START-UP (NO POWER)
JOB NAME: ______________________________
SALES
ORDER #: _______________________________
LOCATION: ______________________________
SOLD BY: _______________________________
INSTALLING
CONTRACTOR: ___________________________
START-UP: ______________________________
TECHNICIAN/
COMPANY: ______________________________
DATE: __________________________________
CHILLER
MODEL #: _____________________________
SERIAL #: _____________________________
COMPRESSOR #1
MODEL #: _____________________________
SERIAL #: _____________________________
COMPRESSOR #2
MODEL #: _____________________________
SERIAL #: _____________________________
Содержание YCAZ88EE8
Страница 16: ...16 YORK INTERNATIONAL WIRING DIAGRAMS LD02165 FIG 5 ELEMENTARY DIAGRAM ...
Страница 17: ...FORM 150 60 NM3 17 YORK INTERNATIONAL FIG 5 ELEMENTARY DIAGRAM Cont d LD02166 ...
Страница 20: ...20 YORK INTERNATIONAL CONNECTION DIAGRAM ELECTRICAL BOX FIG 7 CONNECTION DIAGRAM LD02171 ...
Страница 21: ...FORM 150 60 NM3 21 YORK INTERNATIONAL FIG 7 CONNECTION DIAGRAM Cont d LD02172 ...