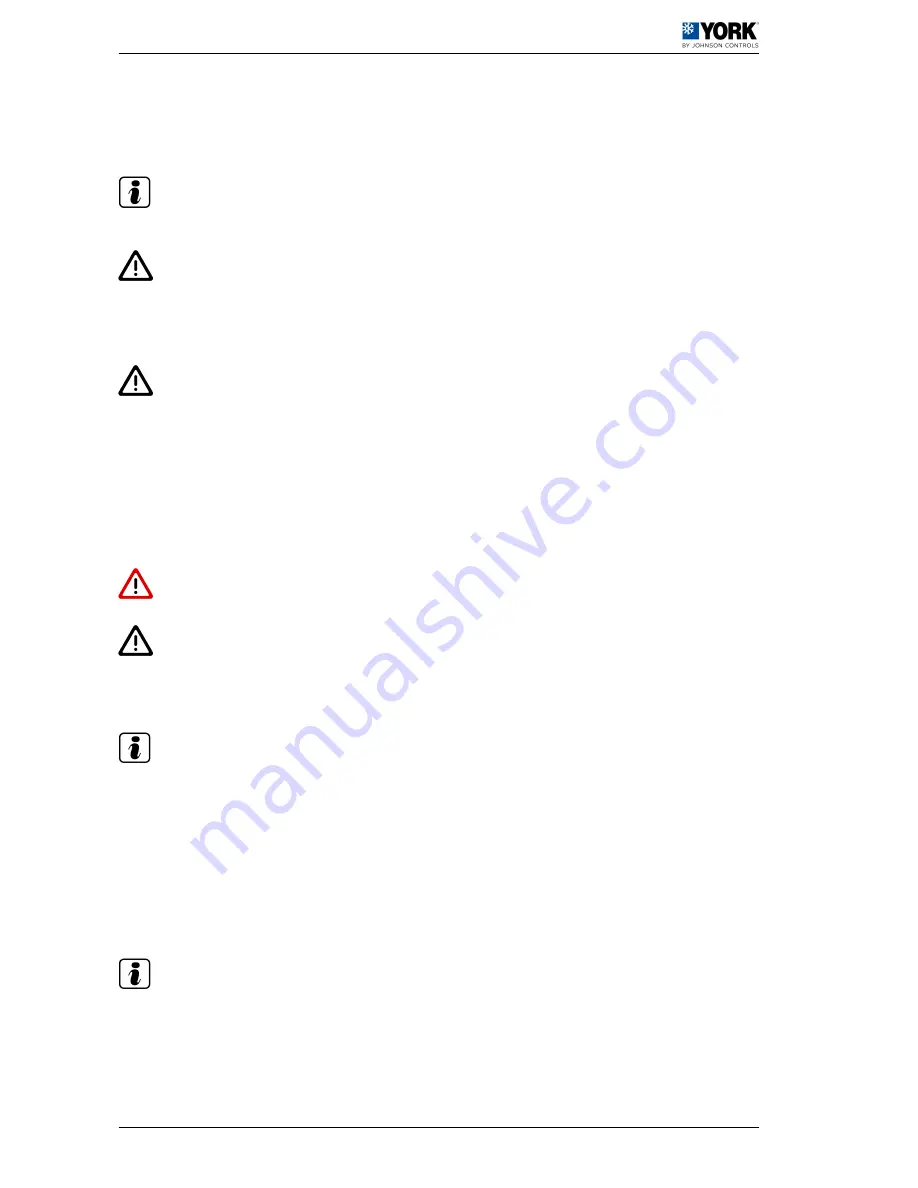
Characteristics of utility provider connections
In general, the different connections required by the unit are made following the shortest route possible.
Under no circumstances may any local or national regulations be contravened when performing the
preparatory work for service connections.
N O T E
For further information on this subject, always keep the current regulations for the country where the unit
is being installed at hand.
C A U T I O N
• Before the connection work, possible losses of flow, temperature and voltage drops, etc. that might
affect the distances between planned connection points and the unit must be taken into account.
• As a result, each connection must be sized accordingly.
Pipes to be used
C A U T I O N
Do not leave compressors or dehydrator filters exposed.
Use K or L-type cooling quality copper pipes, S/ASTMB88.
The pipes must be sealed and insulated until they are connected to the units.
Insulation of refrigerant pipes
The pipe insulation must be made of a suitable material with a minimum thickness of 8 mm to avoid
condensation and minimum temperature loss due to radiation.
Connection pipe installation
D A N G E R
Do not carry out work outdoors in the event of adverse weather conditions
C A U T I O N
Do not use stripping products on Cu ‑ Cu joints.
Use rods with a low melting point and a minimum silver content of 5% when welding the pipes. During
this process, there must be a current of dry nitrogen inside the pipe to prevent rust and scale from forming
that would damage the welding and, therefore, affect the watertightness of the circuit.
N O T E
• The connection pipes between units must be as short as possible.
• No drain traps are necessary where connecting piping specifications are met.
Vacuum and dehydrating
The presence of air and dampness in the cooling circuit must be completely eliminated to avoid:
• Damage to the compressor and other parts of the cooling circuit.
• A drop in unit performance.
• Capillary blocking due to freezing.
• Unwanted high pressure increases.
• Increased electricity consumption.
N O T E
Prior to the vacuum process, nitrogen gas can be swept through the system to remove most of the
dampness and other contaminants in the cooling circuit. The vacuum should be broken on several
occasions using nitrogen to ensure dampness is eliminated.
The vacuum is ensure in each cooling circuit as follows:
1. Connect the vacuum pump to the service valves -1- (3/8" taps) on the installation and connect the
service manometers to the valve stems (1/4" taps) in the circuit.
1
Installation manual
1.10 Instructions for installation and connection of the unit
32