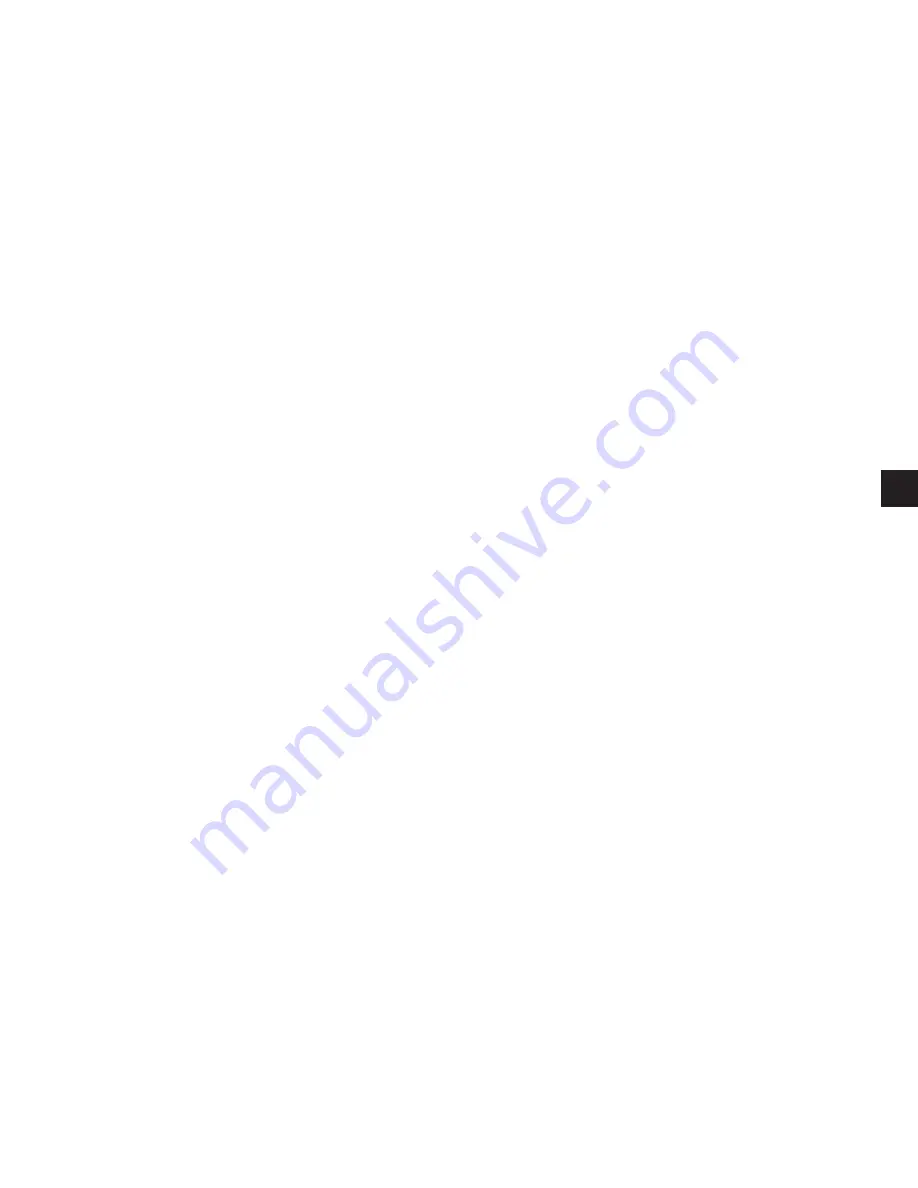
FORM 160.73-O2 (605)
19
YORK INTERNATIONAL
OIL PUMP
For normal operation, the oil pump should operate at all
times during chiller operation.
On shutdown of the system for any reason, the oil pump
operates and continues to run for 150 seconds. The sys-
tem cannot restart during that time interval.
OIL HEATER
During long idle periods, the oil in the compressor oil
reservoir tends to absorb as much refrigerant as it can
hold, depending upon the temperature of the oil and
the pressure in the reservoir. As the oil temperature is
low ered, the amount of refrigerant absorbed will be
in creased. If the quantity of refrigerant in the oil be-
comes excessive, violent oil foaming will result as the
pres sure within the system is lowered on starting. This
foam ing is caused by refrigerant boiling out of the oil
as the pres sure is lowered. If this foam reaches the oil
pump suc tion, the bearing oil pressure will fl uctuate with
pos si ble temporary loss of lubrication, causing the oil
pres sure safety cutout to actuate and stop the system.
See “Con trol Center” Form 160.54-O1.
MOTOR DRIVELINE
The compressor motor is an open-drip-proof, squirrel
cage, induction type constructed to YORK design spec-
i fi ca tions. 60 hertz motors operate at 3570 rpm. 50 hertz
motors operate at 2975 rpm.
The open motor is provided with a D-fl ange, cast iron
adapter mounted to the compressor and supported by a
motor support.
Motor drive shaft is directly connected to the com pres sor
shaft with a fl exible disc coupling. This coupling has
all metal construction with no wearing parts to as sure
long life, and no lubrication requirements to pro vide
low maintenance.
For units utilizing remote Electro-Mechanical starters,
a terminal box is provided for fi eld connected conduit.
Motor terminals are brought through the motor casing
into the terminal box. Jumpers are furnished for three-
lead type of starting. Motor terminal lugs are not fur-
nished. Overload/overcurrent transformers are fur nished
with all units.
HEAT EXCHANGERS
Evaporator and condenser shells are fabricated from
rolled carbon steel plates with fusion welded seams.
Heat exchanger tubes are internally enhanced type.
The evaporator is a shell and tube, fl ooded type heat
exchanger. A distributor trough provides uniform
dis tri bu tion of refrigerant over the entire shell length.
Stain less steel mesh elim i na tors or suction baffl es are
lo cat ed above the tube bun dle to pre vent liquid re frig -
er ant carryover into the com pres sor. A 2" liquid level
sight glass is lo cat ed on the side of the shell to aid in
de ter min ing proper re frig er ant charge. The evap o ra tor
shell con tains dual re frig er ant relief valves.
The condenser is a shell and tube type, with a dis charge
gas baffl e to prevent direct high velocity im pinge ment
on the tubes. A separate subcooler is lo cat ed in the con-
dens er to enhance performance. Dual refrigerant relief
valves are located on condenser shells with op tion al
iso la tion refrigerant isolation valves.
The removable compact water boxes are fabricated of
steel. The design working pressure is 150 PSIG (1034
kPa) and the boxes are tested at 225 PSIG (1551 kPa).
In te gral steel wa ter baf fl es provide the required pass
ar range ments. Stub-out wa ter nozzle connections with
Victaulic grooves are weld ed to the water boxes. These
nozzle connections are suitable for Victaulic cou plings,
weld ing or fl anges, and are capped for shipment. Plugged
3/4" drain and vent connections are provided in each
water box.
REFRIGERANT FLOW CONTROL
Refrigerant fl ow to the evaporator is controlled by a
variable orifi ce.
A level sensor senses the re frig er ant level in the con-
dens er and outputs an analog volt age to the Microboard
that represents this level (0% = empty; 100% = full).
Under program control, the Microboard mod u lates a
variable orifi ce to control the con dens er re frig er ant lev el
to a programmed setpoint. Oth er setpoints affect the
control sensitivity and re sponse. These set points must
be entered at chiller com mis sion ing by a qualifi ed ser-
vice technician. Only a qual i fi ed service technician may
modify these settings.
3