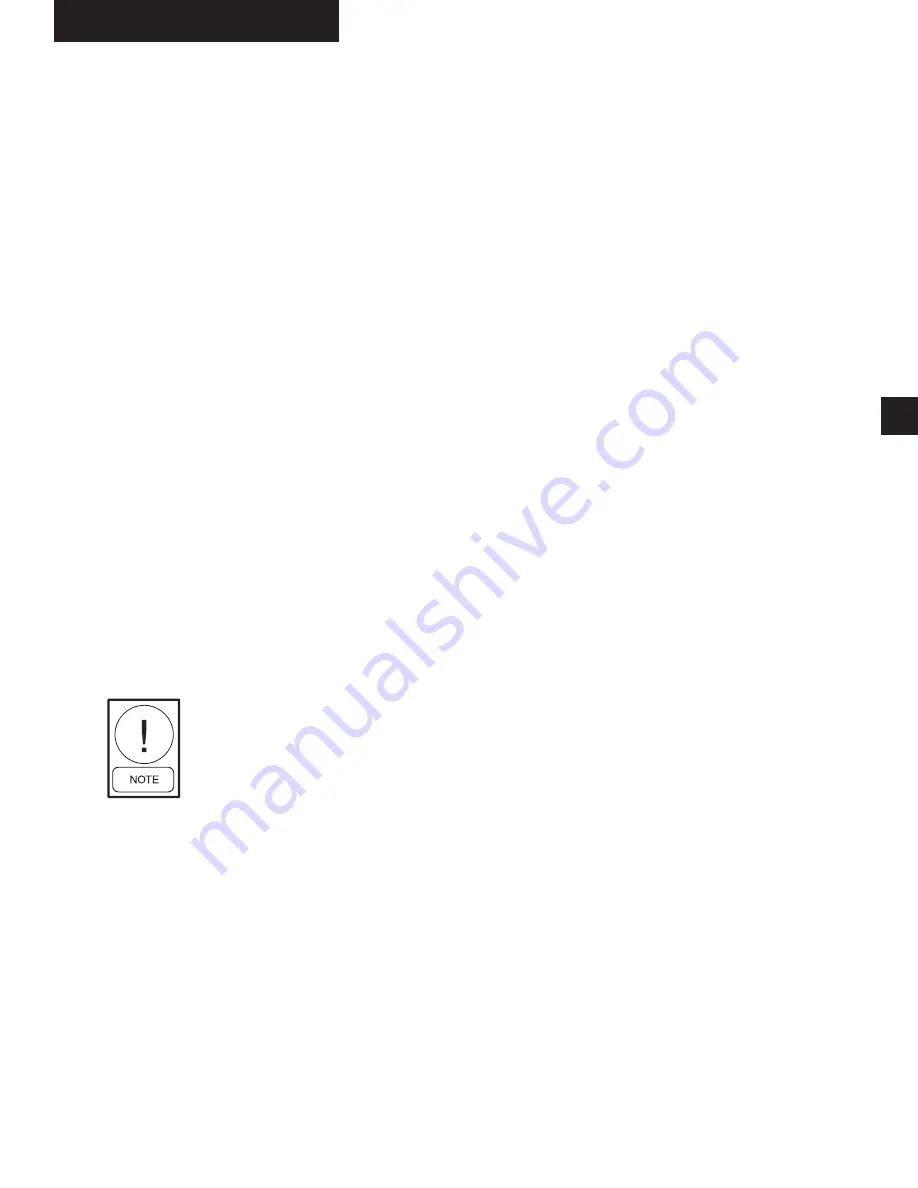
FORM 160.73-O2 (605)
13
YORK INTERNATIONAL
2
7. Check the compressor motor current on the
SYS TEM
Screen.
8. Check for any signs of dirty or fouled con dens er
tubes. (The temperature difference between water
leaving condenser and saturated con dens ing tem-
per a ture should not exceed the difference re cord ed
for a new unit by more than 4°F, 2.2°C).
Weekly
1. Check the refrigerant charge. (See “Checking The
Refrigerant Charge”, page 28.)
Monthly
1. Leak check the entire chiller.
Quarterly
1. Perform chemical analysis of oil.
Semi-Annually (or more often as required)
1. Change and inspect compressor oil fi lter element.
2. Oil return system.
a.
Change
dehydrator.
b. Check nozzle of eductor for foreign particles.
3. Check controls and safety cutouts.
Annually (more often if necessary)
If quarterly inspection indicates oil is
fi ne, replacing the oil is not necessary.
1. Drain and replace the oil in the compressor oil sump.
(See “Oil Charging Procedure” page 22.)
2. Evaporator and Condenser.
a. Inspect and clean water strainers.
b. Inspect and clean tubes as required.
c.
Inspect
end
sheets.
3. Compressor Drive Motor (See motor man u fac tur ers
maintenance and service instruction supplied with
unit)
a. Clean air passages and windings per man u fac -
tur ers instructions.
b. Meg motor windings – See Fig. 13 for details.
c. Lubricate per motor manufacturer recommenda-
tions.
4. Inspect and service electrical components as nec es sary.
5. Perform refrigerant analysis.
NEED FOR MAINTENANCE OR SERVICE
If the system is malfunctioning in any manner or the
unit is stopped by one of the safety controls, consult
the “Operation Analysis Chart”, (Table 1), pages 23
and 24 of this instruction. After consulting this chart,
if you are unable to make the proper repairs or ad just -
ments to start the compressor or the particular trou ble
con tin ues to hinder the performance of the unit, please
call the near est YORK District Offi ce. Failure to re port
con stant trou bles could damage the unit and in crease
the cost of repairs.
STOPPING THE SYSTEM
The Optiview™ Control Center can be pro grammed to
start and stop automatically (maximum, once each day)
whenever desired. Refer to Form 160.54-O1. To stop the
chiller, proceed as follows:
1. Push the
COMPRESSOR STOP/RESET
switch.
The compressor will stop au to mat i cal ly. The oil
pump will continue to run for coastdown pe ri od.
The oil pump will then stop au to mat i cal ly.
2. Stop the chilled water pump (if not wired into the
Microcomputer Control Center, in which case it will
shut off automatically si mul ta neous ly with the oil
pump.) (The actual water pump con tact op er a tion is
dependent upon the position of Microboard jump er
J54.)
3. Open the switch to the cooling tower fan motors, if
used.
4. The compressor sump oil heater is energized when
the unit is stopped.
PROLONGED SHUTDOWN
If the chiller is to be shut down for an extended period of
time (for example, over the winter season), the fol low ing
paragraphs outline the procedure to be fol lowed.
1. Test all system joints for refrigerant leaks with a
System Op er at ing Pro ce dures