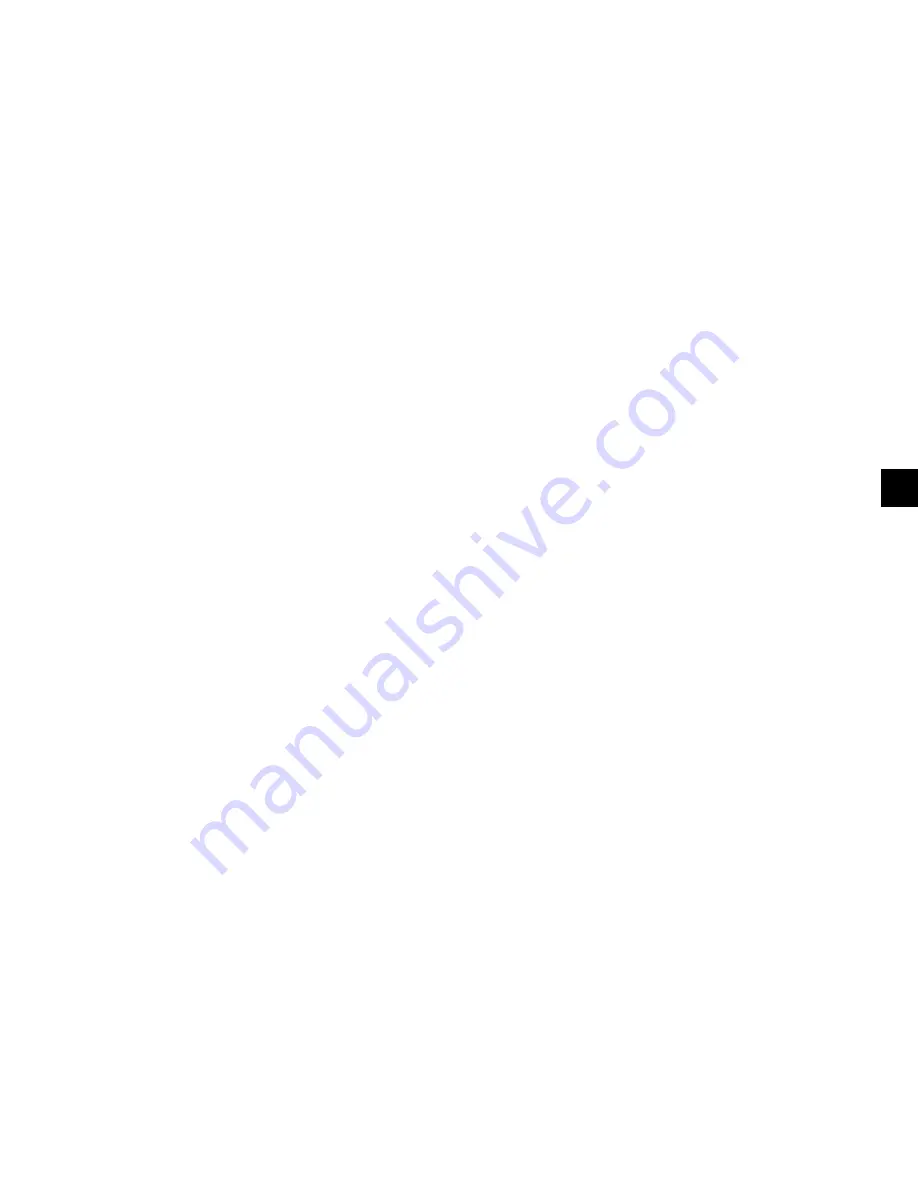
YORK INTERNATIONAL
16
FORM 160.54-O2(1102)
FORM 160.54-O2(1102)
17
YORK INTERNATIONAL
GENERAL
The YORK Model YK MaxE
TM
Centrifugal Liquid
Chiller is completely factory-packaged including evapo-
rator, condenser, compressor, motor, lubrication system,
OptiView Control Center, and all interconnecting unit
piping and wiring.
COMPRESSOR
The compressor is a single-stage centrifugal type pow-
ered by an open-drive electric motor.
The rotor assembly consists of a heat-treated alloy steel
drive shaft and impeller shaft with a cast aluminum,
fully shrouded impeller. The impeller is designed for
balanced thrust and is dynamically balanced and over-
speed tested. The inserted type journal and thrust bear-
ings are fabricated of aluminum alloy. Single helical
gears with crowned teeth are designed so that more than
one tooth is in contact at all times. Gears are integrally
assembled in the compressor rotor support and are film
lubricated. Each gear is individually mounted in its own
journal and thrust bearings.
The open-drive compressor shaft seal is a double
bellows cartridge style with ceramic internal and
atmospheric seal faces. The seal is oil-flooded at all
times and is pressure-lubricated during operation.
CAPACITY CONTROL
Prerotation vanes (PRV) modulate chiller capacity from
100% to as low as 15% of design for normal air condi-
tioning applications. Operation is by an external, electric
PRV actuator which automatically controls the vane
position to maintain a constant leaving chilled liquid
temperature.
COMPRESSOR LUBRICATION SYSTEM
(See Fig. 8)
The chiller lubrication system consists of the oil pump,
oil filter, oil cooler and all interconnecting oil piping and
passages. There are main points within the motor-com-
pressor which must be supplied with forced lubrication
as follows:
1. Compressor Drive Shaft (Low Speed)
a. Shaft seal.
b. Front and rear journal bearings – one on each
side of driving gear.
c. Low speed thrust bearing (forward and reverse).
2. Compressor Driven Shaft (High Speed)
a. Forward and reverse high speed thrust
bearing.
b. Two journal bearings.
3. Speed Increasing Gears
a. Meshing surfaces of drive and pinion gear teeth.
To provide the required amount of oil under the
necessary pressure to properly lubricate these parts,
a motor driven submersible oil pump is located in a
remote oil sump.
Upon pressing of the
COMPRESSOR START
switch on the Control Center, the oil pump is imme-
diately energized. After a 50 second pre-lube period,
the compressor motor will start. The oil pump will
continue to run during the entire operation of the
compressor, and for 150 seconds during compressor
coastdown.
The submerged oil pump takes suction from the sur-
rounding oil and discharges it to the oil cooler where
heat is rejected. The oil flows from the oil cooler to
the oil filter. The oil leaves the filter and flows to the
emergency oil reservoir where it is distributed to the
compressor bearings. The oil lubricates the compres-
sor rotating components and is returned to the oil
sump.
There is an emergency oil reservoir located at the
highest point in the lubrication system internally
in the compressor. It provides an oil supply to the
various bearings and gears in the event of a system
shutdown due to power failure. The reservoir, located
on the top of the compressor, allows the oil to be
distributed through the passages by gravity flow, thus
providing necessary lubrication during the compressor
coastdown.
3