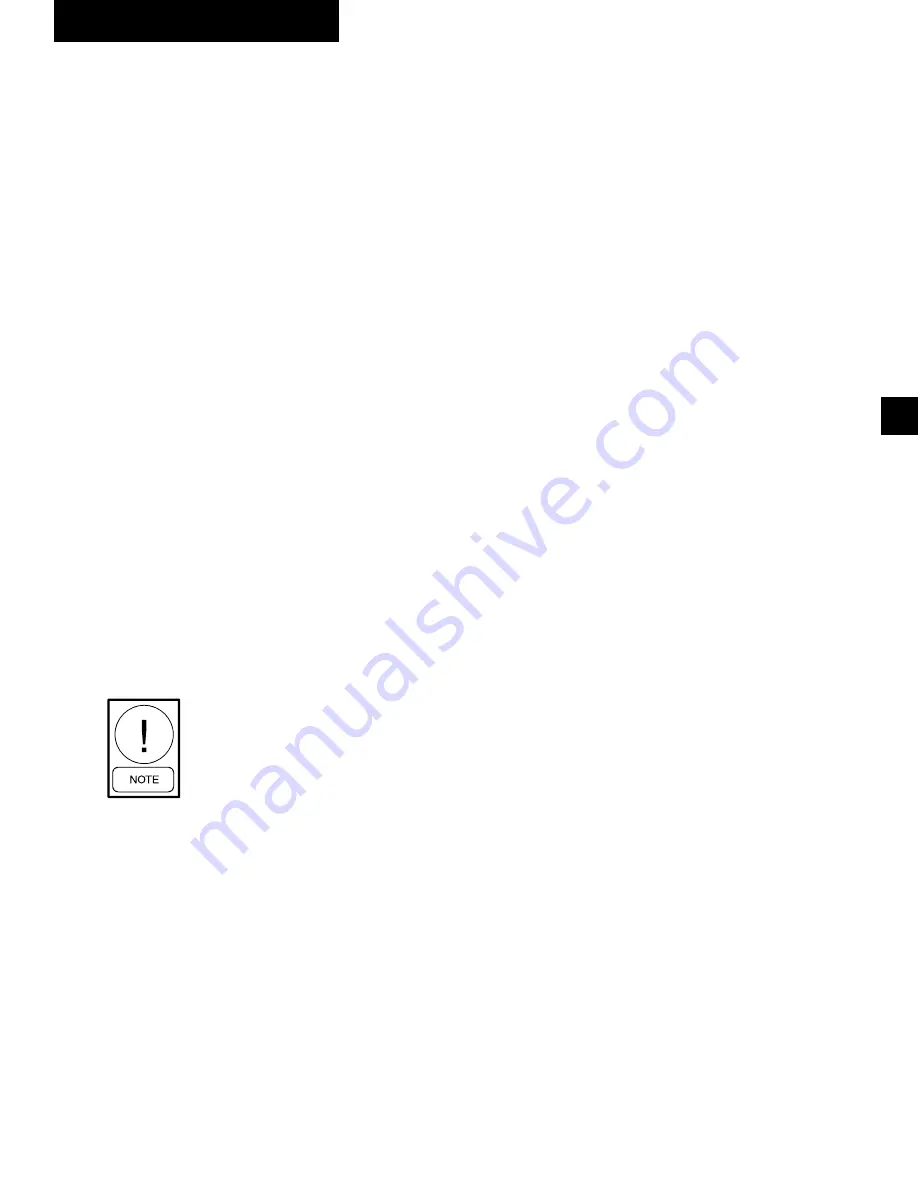
YORK INTERNATIONAL
12
FORM 160.54-O2(1102)
FORM 160.54-O2(1102)
13
YORK INTERNATIONAL
2
7. Check the compressor motor current on the
SYSTEM
Screen.
8. Check for any signs of dirty or fouled condenser
tubes. (The temperature difference between water
leaving condenser and saturated condensing tem-
perature should not exceed the difference recorded
for a new unit by more than 4°F, 2.2°C).
Weekly
1. Check the refrigerant charge. (See “Checking The
Refrigerant Charge”,page 28.)
2. Leak check the entire chiller.
Quarterly
1. Perform chemical analysis of oil.
Semi-Annually (or more often as required)
1. Change and inspect compressor oil filter element.
2. Oil return system.
a. Change dehydrator.
b. Check nozzle of eductor for foreign particles.
3. Check controls and safety cutouts.
Annually (more often if necessary)
If quarterly inspection indicates
oil is fine, replacing the oil is not
necessary.
1.Drain and replace the oil in the compressor oil
sump. (See “Oil Charging Procedure” page 22.)
2. Evaporator and Condenser.
a. Inspect and clean water strainers.
b. Inspect and clean tubes as required.
c. Inspect end sheets.
3. Compressor Drive Motor (See motor manufacturers
maintenance and service instruction supplied with
unit)
a. Clean air passages and windings per manufac-
turers instructions.
b. Meg motor windings – See Fig. 13 for details.
c. Lubricate per motor manufacturer recommenda-
tions.
4. Inspect and service electrical components as necessary.
5. Perform refrigerant analysis.
NEED FOR MAINTENANCE OR SERVICE
If the system is malfunctioning in any manner or the
unit is stopped by one of the safety controls, consult
the “Operation Analysis Chart”, (Table 1), pages 23
and 24 of this instruction. After consulting this chart,
if you are unable to make the proper repairs or adjust-
ments to start the compressor or the particular trouble
continues to hinder the performance of the unit, please
call the nearest YORK District Office. Failure to
report constant troubles could damage the unit and
increase the cost of repairs.
STOPPING THE SYSTEM
The Optiview™ Control Center can be programmed
to start and stop automatically (maximum, once each
day) whenever desired. Refer to Form 160.54-O1. To
stop the chiller, proceed as follows:
1. Push the
COMPRESSOR STOP/RESET
switch.
The compressor will stop automatically. The oil
pump will continue to run for coastdown period.
The oil pump will then stop automatically.
2. Stop the chilled water pump (if not wired into the
Microcomputer Control Center, in which case it
will shut off automatically simultaneously with the
oil pump.) (The actual water pump contact opera-
tion is dependent upon the position of Microboard
jumper J54.)
3. Open the switch to the cooling tower fan motors, if
used.
4. The compressor sump oil heater is energized
when the unit is stopped.
PROLONGED SHUTDOWN
If the chiller is to be shut down for an extended period
of time (for example, over the winter season), the
following paragraphs outline the procedure to be fol-
lowed.
System Operating Procedures