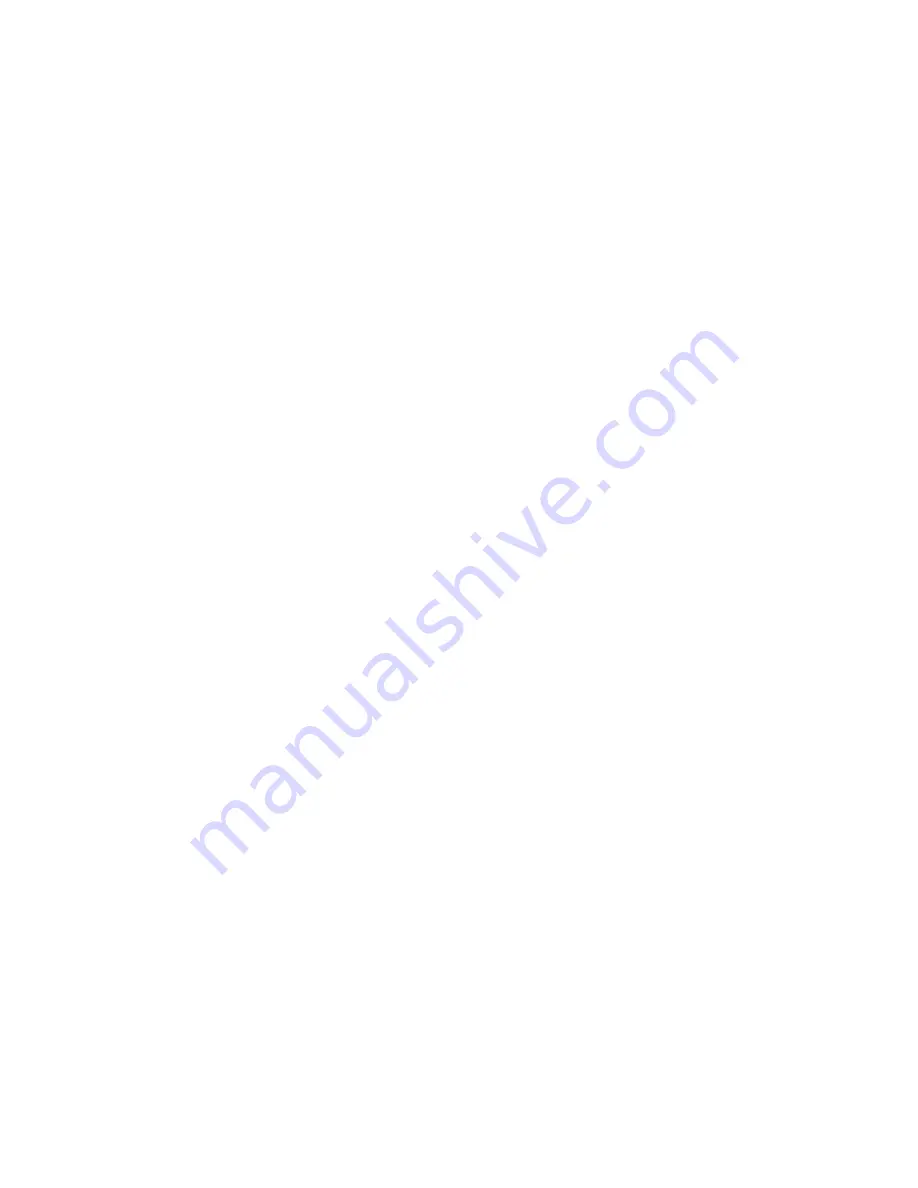
48
YORK INTERNATIONAL
VACUUM TESTING
After the pressure test has been completed, the vacuum
test should be conducted as follows:
1. Connect a high capacity vacuum pump, with indi-
cator, to the system charging valve as shown in
Fig. 22 and start the pump. (See “Vacuum Dehydra-
tion”.)
2. Open wide all system valves, including the purge
and gauge valves. Be sure all valves to the atmo-
sphere are closed.
3. Operate the vacuum pump in accordance with
VACUUM DEHYDRATION until a wet bulb tempera-
ture of +32°F (0°C) or a pressure of 5 mm Hg is
reached. See Table 3 for corresponding values of
pressure.
4. To improve evacuation circulate hot water (not to
exceed 125°F, 51.7°C) through the cooler and con-
denser tubes to thoroughly dehydrate the shells. If
a source of hot water is not readily available, a
portable water heater should be employed. DO NOT
USE STEAM. A suggested method is to connect a
hose between the source of hot water under pres-
sure and the cooler head drain connection, out the
cooler vent connection, into the condenser head
drain and out the condenser vent. To avoid the pos-
sibility of causing leaks, the temperature should be
brought up slowly so that the tubes and shell are
heated evenly.
5. Close the system charging valve and the stop valve
between the vacuum indicator and the vacuum
pump. Then disconnect the vacuum pump leaving
the vacuum indicator in place.
6. Hold the vacuum obtained in Step 3 in the system
for 8 hours; the slightest rise in pressure indicates
a leak or the presence of moisture, or both. If, after
8 hours the wet bulb temperature in the vacuum
indicator has not risen above 40°F (4.4°C) or a pres-
sure of 6.3 mm Hg, the system may be considered
tight.
NOTE: Be sure the vacuum indicator is valved off
while holding the system vacuum and be
sure to open the valve between the vacuum
indicator and the system when checking
the vacuum after the 8 hour period.
7. If the vacuum does not hold for 8 hours within the
limits specified in Step 6 above, the leak must be
found and repaired.
VACUUM DEHYDRATION
To obtain a sufficiently dry system, the following in-
structions have been assembled to provide an effec-
tive method for evacuating and dehydrating a system
in the field. Although there are several methods of de-
hydrating a system, we are recommending the follow-
ing, as it produces one of the best results, and affords
a means of obtaining accurate readings as to the ex-
tent of dehydration.
The equipment required to follow this method of dehy-
dration consists of a wet bulb indicator or vacuum
gauge, a chart showing the relation between dew point
temperature and pressure in inches of mercury (vac-
uum), (see Table 3) and a vacuum pump capable of
pumping a suitable vacuum on the system.
OPERATION
Dehydration of a refrigerant system can be obtained
by this method because the water present in the sys-
tem reacts much as a refrigerant would. By pulling down
the pressure in the system to a point where its satura-
tion temperature is considerably below that of room
temperature, heat will flow from the room through the
walls of the system and vaporize the water, allowing a
large percentage of it to be removed by the vacuum
pump. The length of time necessary for the dehydra-
tion of a system is dependent on the size or volume of
the system, the capacity and efficiency of the vacuum
pump, the room temperature and the quantity of water
present in the system. By the use of the vacuum indi-
cator as suggested, the test tube will be evacuated to
the same pressure as the system, and the distilled
water will be maintained at the same saturation tem-
perature as any free water in the system, and this tem-
perature can be observed on the thermometer.
If the system has been pressure tested and found to
be tight prior to evacuation, then the saturation tem-
perature recordings should follow a curve similar to
the typical saturation curve shown as Fig. 22.
The temperature of the water in the test tube will drop
as the pressure decreases, until the boiling point is
reached, at which point the temperature will level off
and remain at this level until all of the water in the shell
is vaporized. When this final vaporization has taken
place the pressure and temperature will continue to
drop until eventually a temperature of 35°F (1.7°C) or
a pressure of 5 mm Hg. is reached.
When this point is reached, practically all of the air
has been evacuated from the system, but there is still
a small amount of moisture left. In order to provide a