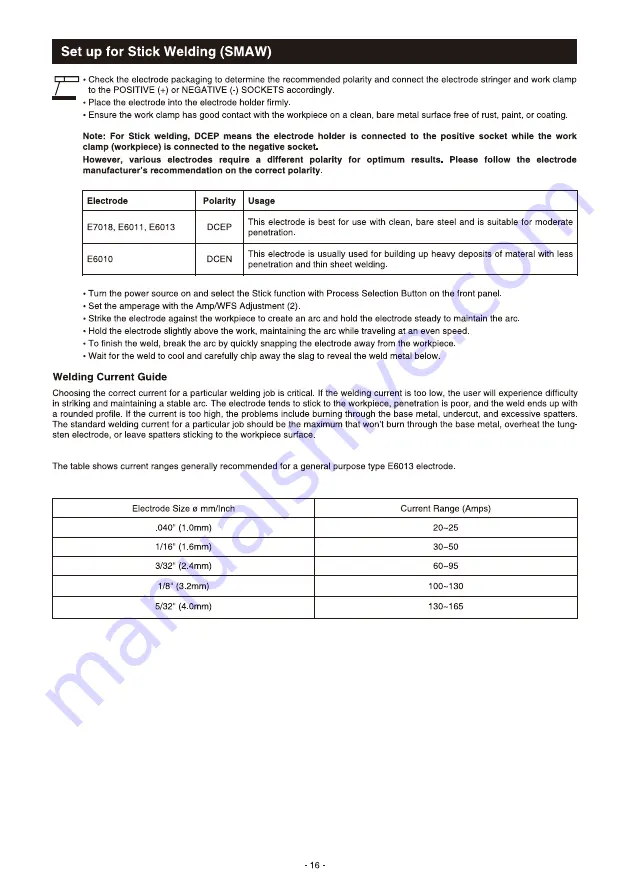
• Turn the power source on and select the Stick function with Process Selection Button on the front panel
• Set the amperage with the Amp/WFS Adjustment
(2)
• Strike the electrode against the workpiece to create an arc and hold the electrode steady to maintain the arc
• Hold the electrode slightly above the work, maintaining the arc while traveling at an even speed
• To finish the weld, break the arc by quickly snapping the electrode away from the workpiece
• Wait for the weld to cool and carefully chip away the slag to reveal the weld metal below.
Welding
Current
Guide
Choosing the correct current for a particular welding job is critical. If the welding current is too low, the user will experience difficulty
in striking and maintaining a stable arc. The electrode tends to stick to the workpiece, penetration is poor, and the weld ends up with
a rounded profile. If the current is too high, the problems include burning through the base metal, undercut, and excessive spatters.
The standard welding current for a particular job should be the maximum that won't burn through the base metal, Overheat the tung-
sten electrode, or leave spatters sticking to the workpiece surface.
The table shows current ranges generally recommended
for a general purpose type E6013 electrode.
Set up for Stick Welding
(SMAW)
• Check the electrode packaging to determine the recommended
polarity and connect the electrode stringer and work clamp
to the POSITIVE (+) or NEGATIVE (-) SOCKETS accordingly
• Place the electrode into the electrode holder firmly
• Ensure the work clamp has good contact with the workpiece on a clean, bare metal surface free of rust, paint, or coating
Note:
For Stick welding,
DCEP means
the electrode
holder
is connected
to the positive
socket
while
the work
clamp (workpiece)
is connected
to the negative
socket.
However,
various
electrodes
require
a different
polarity
for
optimum
results.
Please
follow
the
electrode
manufacturer's
recommendation
on the correct
polarity.
20-25
30-50
60-95
100-130
130-165
Electrode
E7018, E6011, E6013
E6010
Polarity
Usage
This
electrode
is best
for use with clean,
bare
steel
and is suitable
for moderate
DCEP
penetration
This electrode is usually used for building up heavy deposits of materal with less
DCEN
penetration and thin sheet welding
Electrode
Size ø mm/lnch
040" (1 Omm)
1/16"
(1 6mm)
3/32"
(2 4mm)
(3.2mm)
5/32" (4 Omm)
.16
Current Range (Amps)