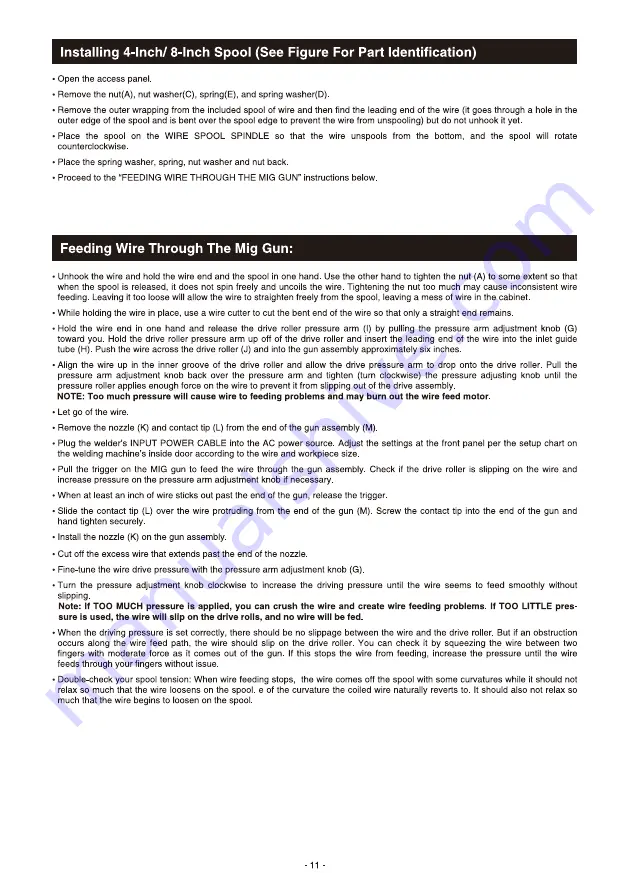
Installing
4-lnch/ 8-lnch Spool (See Figure For Part Identification)
• Open the access panel
• Remove the nut(A), nut washer(C),
spring(E), and spring washer(D)
• Remove the outer wrapping from the included spool of wire and then find the leading end of the wire (it goes through a hole in the
outer edge Of the spool and is bent over the spool edge to prevent the wire from unspooling)
but do not unhook it yet
• Place the
spool
on the WIRE
SPOOL
SPINDLE
so that the
wire
unspools
from the
bottom,
and
the spool
will
rotate
counterclockwise
• Place the spring washer, spring, nut washer and nut back
• Proceed
to the "FEEDING
WIRE
THROUGH
THE
MIG GUN"
instructions
below.
Feeding Wire Through
The Mig Gun:
• Unhook the wire and hold the wire end and the spool in one hand. Use the other hand to tighten the nut (A) to some extent so that
when the spool is released, it does not spin freely and uncoils the wire. Tightening the nut too much may cause inconsistent
wire
feeding. Leaving it too loose will allow the wire to straighten freely from the spool, leaving a mess of wire in the cabinet.
• While holding the wire in place, use a wire cutter to cut the bent end Ofthe wire so that only a straight end remains
• Hold the wire end in one hand and release the drive roller pressure arm (l) by pulling the pressure
arm adjustment
knob (G)
toward you. Hold the drive roller pressure arm up off of the drive roller and insert the leading end of the wire into the inlet guide
tube (H). Push the wire across the drive roller (J) and into the gun assembly approximately
six inches.
• Align the wire up in the inner groove of the drive roller and allow the drive pressure arm to drop onto the drive roller. Pull the
pressure arm adjustment
knob back over the pressure arm and tighten (turn clockwise)
the pressure
adjusting
knob until the
pressure roller applies enough force on the wire to prevent it from slipping out of the drive assembly.
NOTE: Too much pressure
will cause wire to feeding
problems
and may burn out the wire feed motor.
• Let go of the wire
• Remove the nozzle (K) and contact tip (L) from the end Ofthe gun assembly (M)
• Plug the welder's INPUT POWER CABLE into the AC power source. Adjust the settings at the front panel per the setup chart on
the welding machine's
inside door according to the wire and workpiece size
• Pull the trigger on the MIG gun to feed the wire through the gun assembly
Check if the drive roller is slipping on the wire and
increase pressure on the pressure arm adjustment
knob if necessary.
• When at least an inch of wire sticks out past the end of the gun, release the trigger.
• Slide the contact tip (L) over the wire protruding from the end Of the gun (M) Screw the contact tip into the end Of the gun and
hand tighten securely
• Install the nozzle (K) on the gun assembly
• Cut off the excess wire that extends past the end of the nozzle.
• Fine-tune the wire drive pressure with the pressure arm adjustment
knob (G)
• Turn the pressure adjustment
knob clockwise
to increase the driving
pressure
until the wire seems to feed smoothly without
slipping
Note: If TOO MUCH pressure
is applied,
you can crush
the wire and create wire feeding
problems.
If TOO LITTLE pres-
sure is used, the wire will slip on the drive rolls, and no wire will be fed.
• When the driving pressure is set correctly, there should be no slippage between the wire and the drive roller. But if an obstruction
occurs along the wire feed path, the wire should slip on the drive roller. You can check it by squeezing the wire between two
fingers with moderate force as it comes out of the gun. If this stops the wire from feeding, increase the pressure until the wire
feeds through your fingers without issue
• Double-check
your spool tension: When wire feeding stops,
the wire comes off the spool with some curvatures while it should not
relax so much that the wire loosens On the spool
e of the curvature the coiled wire naturally reverts to It should also not relax so
much that the wire begins to loosen on the spool.
.11