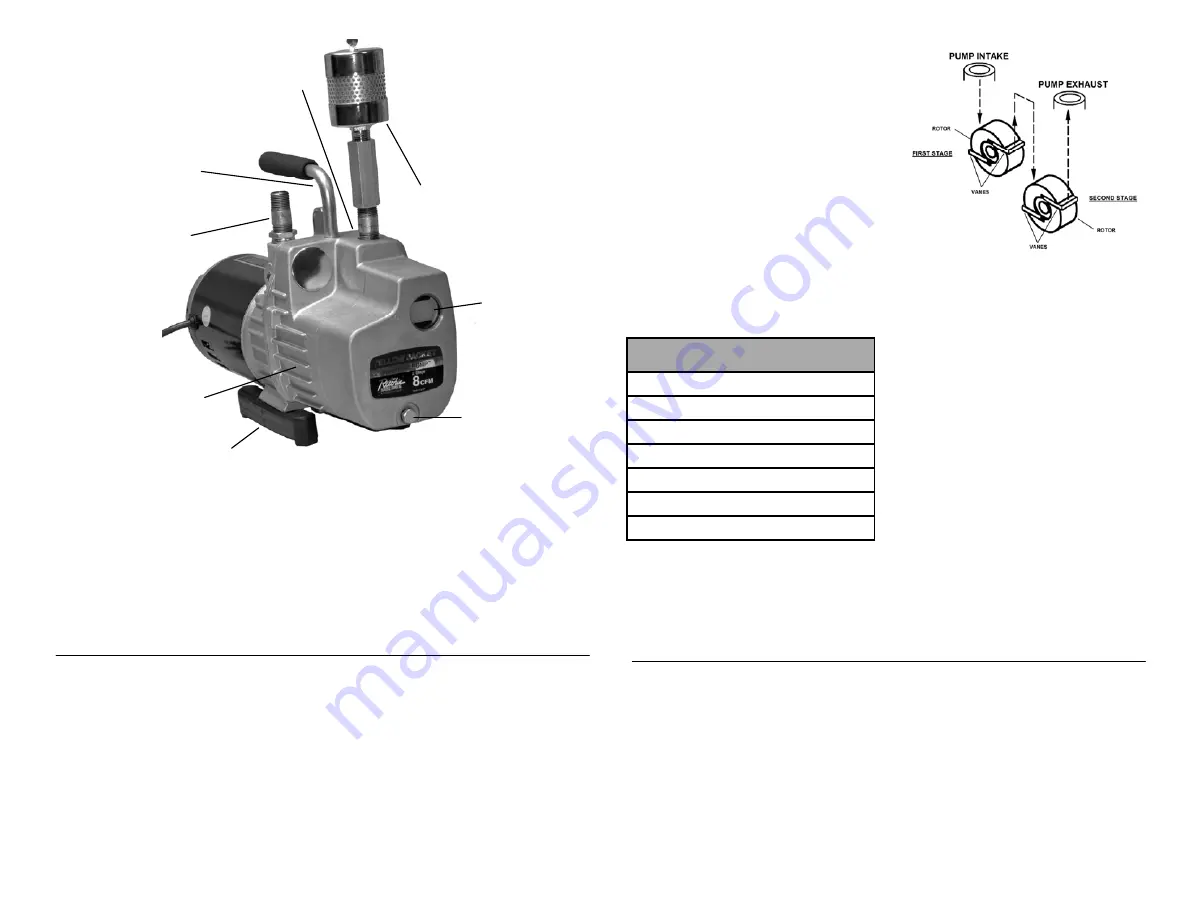
1. Male pipe pump intake. Large hose suggested
for maximum pull down.
2. Gas ballast valve helps remove moisture and
other condensable vapors that have been drawn
into the pump as a result of evacuation. Opening
the ballast allows fresh air to enter the pumping
chamber and keep vapors from combining with
the oil. Vapors escape harmlessly through the
exhaust valve. If combined with oil, vapors can
turn the oil milky white and lower pump per-
formance below specifications.
To operate ballast, turn the valve counter-
clockwise one full turn after evacuation starts.
As the vacuum reading reaches 1000-2000
microns, close the ballast to achieve a deeper
vacuum.
3
1) Male pipe
pump intake
(see below)
Heavy duty high
torque motor for
cold weather
starting.
Longer heat dissipation fins for
a cooler running unit.
Lower operating temperature to
improve efficiency and vacuum.
High resiliency foot pads for
added stability and skid resistance.
Heavy duty metal handle.
Permanently attached to pump
body. Built-in hook hole.
Pump exhaust also doubles as oil fill
port. Use YELLOW JACKET
oil for assurance of a
clean,fast job.
Wide-view
sight glass
for easier
Monitoring
of oil level.
Oil drain valve
for quick draining
and convenient access.
2) Gas ballast valve
(see below)
WARRANTY INFORMATION
Ritchie Engineering guarantees YELLOW
JACKET products to be free of defective material
and workmanship which could affect the life of
the product when used for the purpose for which
it was designed. This warranty does not cover
items that have been altered, abused or returned
solely in need of field service maintenance.
If found defective, we will either replace or repair
at our option products within two years of factory
shipment. Warranty does not cover items that
have been altered, abused (including failure to
use the correct type of vacuum pump oil) or
returned solely in need of field service mainte-
nance.
Returns must be pre-paid.
Warranty does not cover use on lithium bromide
systems.
Features of your New Pump
The 7 Important Steps of Initial Start-Up
The Purpose of the SuperEvac Design
The SuperEvac Pump is a 2-stage rotary vane design
(at right) that increases efficiency and speeds pump
down to 15 microns.
The pump lowers the internal pressure of a refrigera-
tion system until moisture boils into a vapor. As the
moisture is vaporized, it is evacuated by the pump,
helping dehydrate the system. Most technicians try
to achieve between 250 and 1000 microns.
A manometer or electronic vacuum gauge are the
only ways to monitor evacuation progress. Manome-
ter readings are approximate in inches of mercury.
Only an electronic vacuum gauge is accurate enough
to show when you reach the desired micron range.
As the chart shows, only an electronic gauge reads
fine differences to provide assurance that the vac-
uum is low enough to boil the greatest possible
amount of moisture.
How one small drop dampens your profits.
A small drop of moisture can hurt your profits and
reputation.
During new system set-up, protective caps are re-
moved admitting moisture and air into system com-
ponents.
If air – a non-condensable – remains in the system,
it collects on the high side reducing system effi-
ciency. This causes a rise in head pressure. The
discharge valve gets hotter than normal and organic
solids form causing compressor failure.
Moisture in the system can form ice which closes
off openings in expansion valves and cap tubes, and
prevent adequate cooling.
Ultimately moisture and air can produce acids and
sludge which could cause in-warranty failures.
During service and parts replacement, the same
contaminants get in again, and you could be called
back for repairs by a dissatisfied customer.
Moisture and air can even enter through system
leaks. And as the moisture in the air increases, so
does the amount of contamination. The higher the
humidity, the bigger your problem.
A vacuum pump "pulls" air and moisture out of the
system before the system is damaged. The higher
and more complete the vacuum, the more moisture
is removed. That's why your SuperEvac pump is
specifically engineered for high vacuums of 50
microns and better.
Boiling temp
of water
Inches
mercury
Microns
212°F (100°C)
0
760,000
151°F (66°C)
22.05
200,000
101°F (38°C)
27.95
50,000
78°F (26°C)
28.95
25,000
35°F (2°C)
29.72
5,000
1°F (17°C)
29.882
1,000
- 50°F (-46°C)
29.919
50
First stage exhausts into the intake of the second stage
similar to two single stage pumps connected together.
1) Make sure motor is off and name plate volt-
age on motor bottom matches outlet voltage.
2) Remove exhaust filter. Fill with YELLOW
JACKET SuperEvac Pump Oil until oil level
is even with oil level line. Replace exhaust
filter.
3) With the intake port open, switch on the
motor. When pump reaches running speed,
connect the pump to the system.
4) To check the pump's performance, attach a
micron gauge to the intake port, making sure
that the gas ballast valve is closed. Turn on
the pump. The micron gauge will display the
ultimate vacuum reached.
5) Improve cold weather starting by opening
intake and running your pump for 10-15
seconds.
6) Before turning pump off, break vacuum to
atmosphere.
4