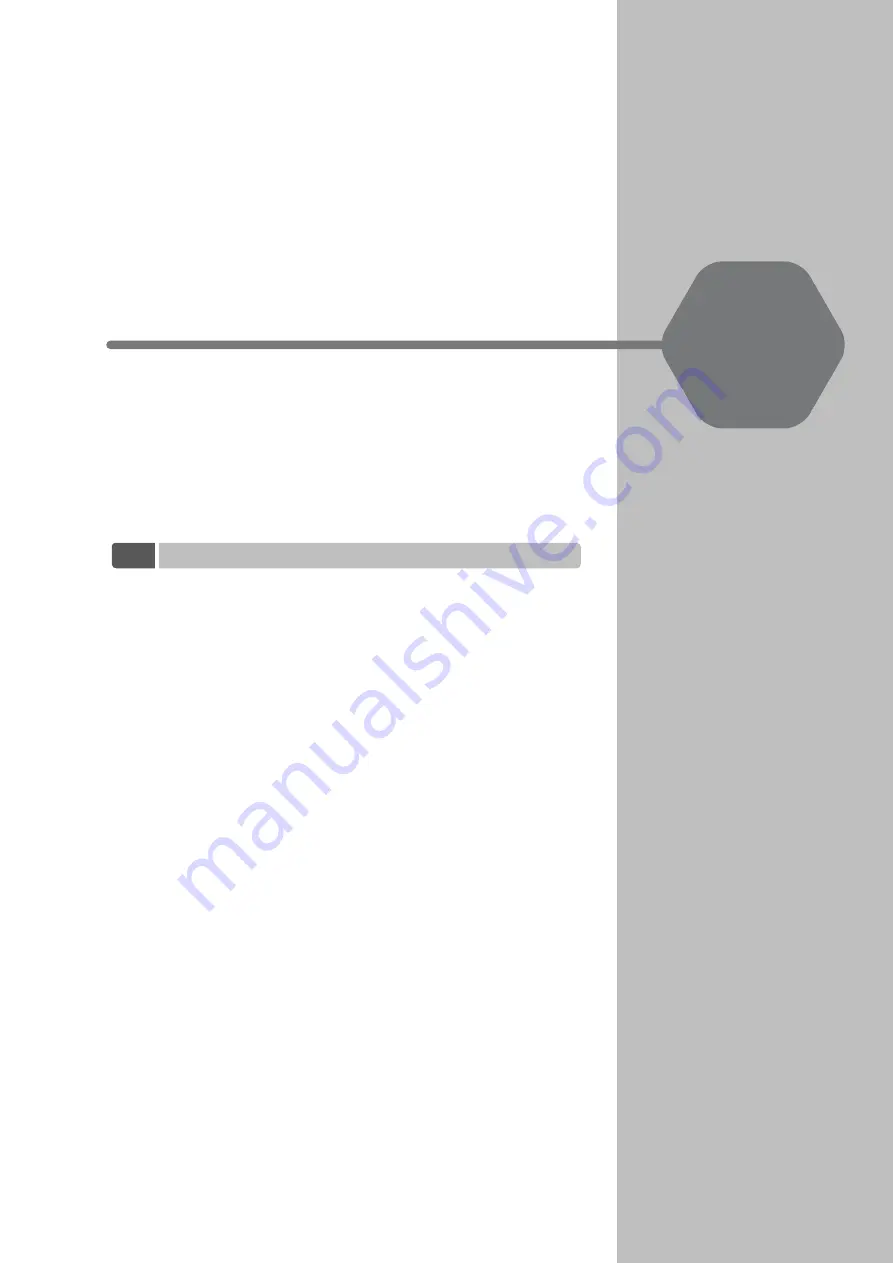
This chapter provides the EMC installation conditions for
SERVOPACKs that have the HWBB function.
EMC Installation Conditions . . . . . . . . . . . . 3-2
-7W . . . . . . . . . . . . . . . . . . . . . . . . . . . . . . . . . . 3-2
-7C . . . . . . . . . . . . . . . . . . . . . . . . . . . . . . . . . . 3-3
SERVOPACK
Installation
3