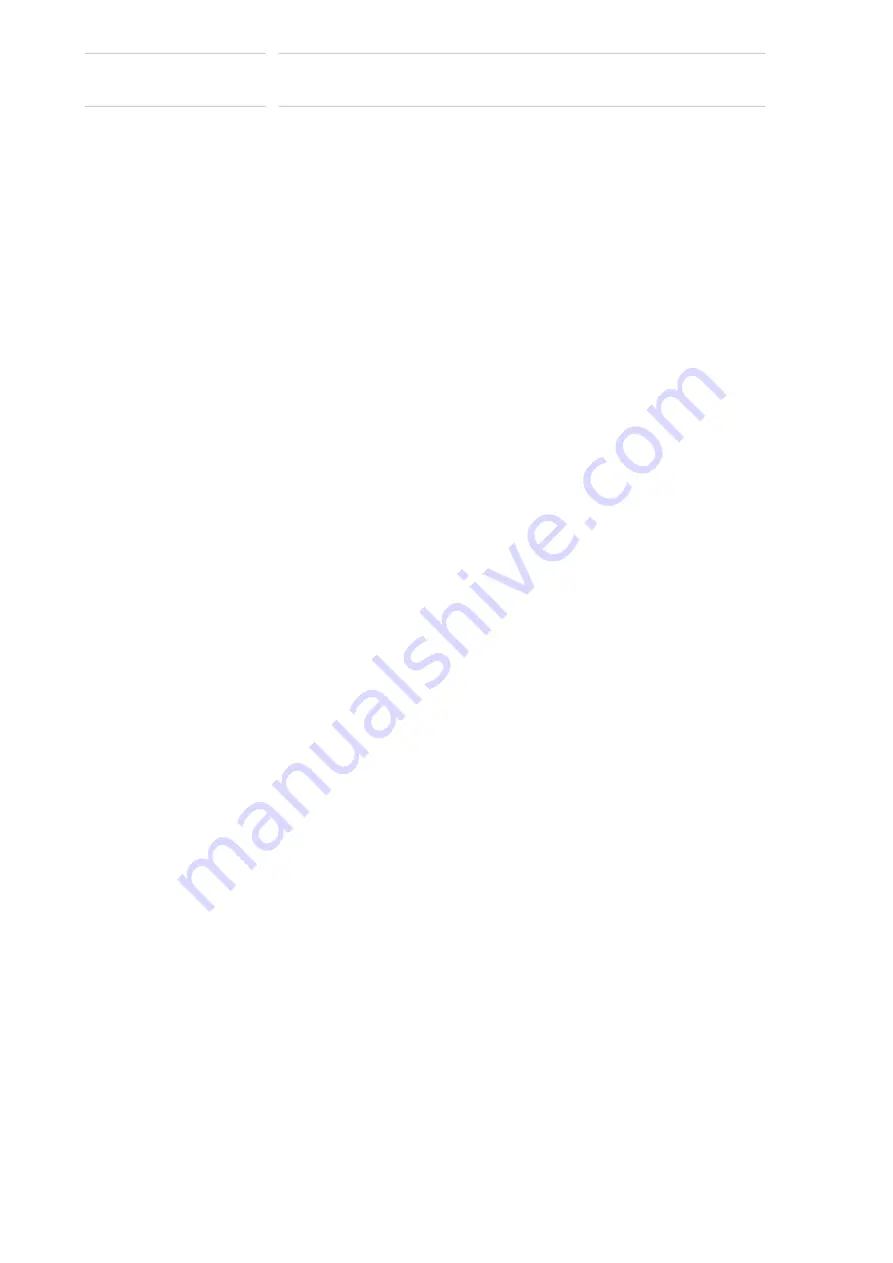
A-4
186638-1CD
186638-1CD
Appendix A
A.1 Glossary
C
GP8 EduCart
Cartesian Topology
A topology, which uses prismatic joints throughout, normally arranged to
be perpendicular to each other.
Cartesian-coordinate Robot
A Cartesian-coordinate Robot is a robot whose manipulator-arm degrees
of freedom are defined by Cartesian Coordinates. This describes motions
that are east-west, north-south and up-down, as well as rotary motions to
change orientation.
Category 3 (Cat3)
Category 3 (Cat 3) means that the safety related parts of the control
system will be designed so that:
• Single faults will not prevent the safety function from working
correctly.
• Single faults will be detected at or before the next demand of the
safety function.
• When a single fault does occur, a safe state shall be maintained until
the detected fault is corrected.
• All reasonably foreseeable faults are detected.
Caution
Indicates a hazardous situation, which if not avoided, could result in minor
or moderate injury. It may also be used without the safety alert symbol as
an alternative to “NOTICE”.
Centrifugal Force
When a body rotates about an axis other than one at it's center of mass, it
exerts an outward radial force called centrifugal force upon the axis, which
restrains it from moving in a straight tangential line. To offset this force,
the robot must exert an opposing torque at the joint of rotation.
Circular Motion Type
A calculated path that the robot executes, and is circular in shape.
Clamp
An end-effector which serves as a pneumatic hand that controls the
grasping and releasing of an object. Tactile, and feed-back force sensors
are used to manage the applied force to the object by the clamp. See
Clamping
The maximum permissible force acting on a body region, resulting from a
robot collision where the period of contact results in a plastic deformation
of a person’s soft tissue.
Clamping Force
When contact can cause a body part(s) to be clamped.
Closed-loop
Control achieved by a robot manipulator by means of feedback
information. As a manipulator is in action, its sensors continually
communicate information to the YRC1000micro Controller, which is used
to further guide the manipulator within the given task. Many sensors are
used to feed back information about the manipulator's placement, speed,
torque, applied forces, as well as the placement of a targeted moving
.
62 of 88