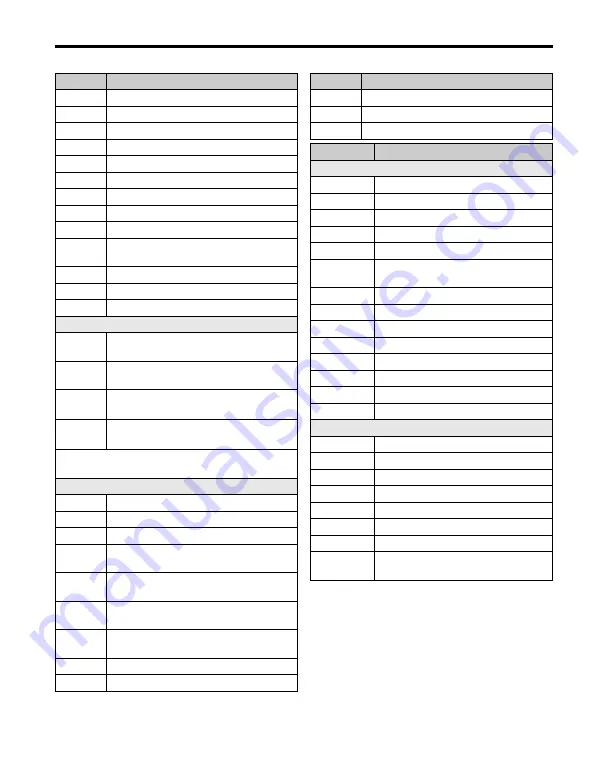
7 Parameter Table
YASKAWA Europe
TOEP C710606 50B - AC Drive L1000V - Quick Start Guide
EN 43
U2-05
Output Current at Previous Fault
U2-06
Motor Speed at Previous Fault
U2-07
Output Voltage at Previous Fault
U2-08
DC Bus Voltage at Previous Fault
U2-09
Output Power at Previous Fault
U2-10
Torque Reference at Previous Fault
U2-11
Input Terminal Status at Previous Fault
U2-12
Output Terminal Status at Previous Fault
U2-13
Drive Operation Status at Previous Fault
U2-14
Cumulative Operation Time at Previous
Fault
U2-15
Soft Starter Output at Previous Fault
U2-16
Motor q-Axis Current at Previous Fault
U2-17
Motor d-Axis Current at Previous Fault
Fault History
U3-01 to
U3-04
First to 4th Most Recent Fault
U3-05 to
U3-10
5th to 10th Most Recent Fault
U3-11 to
U3-14
Cumulative Operation Time at 1st to 4th
Most Recent Fault
U3-15 to
U3-20
Cumulative Operation Time at 5th to 10th
Most Recent Fault
* The following faults are not recorded in the error log:
CPF00, 01, 02, 03, Uv1, and Uv2.
Maintenance Monitors
U4-01
Cumulative Operation time
U4-02
Total number of Run commands
U4-03
Cooling Fan Operation Time
U4-04
Cooling Fan wear as a percentage of
expected lifetime.
U4-05
Capacitor wear as a percentage of expected
lifetime
U4-06
Soft Start relay wear as a percentage of
expected lifetime.
U4-07
IGBT wear as a percentage of expected life-
time.
U4-08
Heatsink temperature in °C.
U4-09
LED Check.
Monitor
Description
U4-10
kWH, lower 4 digits.
U4-11
kWH, upper 4 digits.
U4-13
Peak hold current.
DI/DO Sel
Description
Digital Input Function Selections (H1-
)
3
Multi-Step Speed Reference 1
4
Multi-Step Speed Reference 2
5
Multi-Step Speed Reference 3
F
Through Mode (Not Used)
14
Fault Reset
20 to 2F
External Fault Settings (NO/NC, Detec-
tion Always/During Run)
50
Nominal Speed
51
Intermediate Speed
52
Releveling Speed
53
Leveling Speed
54
Inspection Speed
55
Rescue Operation
56
Motor Contactor Feedback
79
Brake Feedback
Digital Output Function Selections (H2-
)
0
During RUN
6
Drive Ready
E
Fault
F
Not Used
50
Brake Control
51
Output Contactor Control
58
Safe Disable Status
1
Inverse logic for any of the digital output
functions.
Monitor
Description