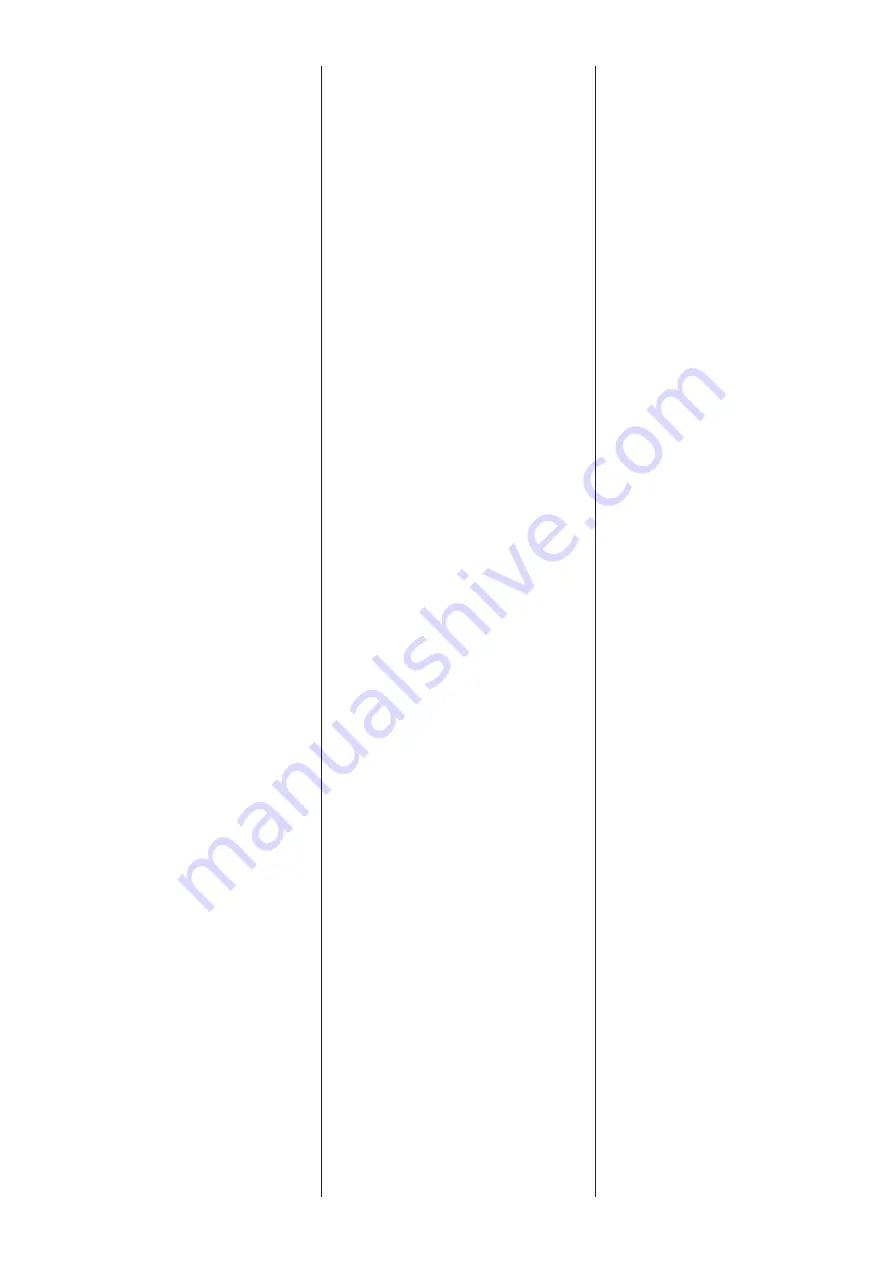
4
ing or deflection of the load. The tackles
should be used in connection with a spread-
er beam.
- Make sure that the hook of the crane or hoist
corresponds to shape and size of the
suspension eye (Fig. 5) of the load hoisting
tackle.
- The accident prevention act and safety reg-
ulations for load hoisting tackle valid in the
country of operation are to be strictly adhered
to at all times.
- If defects are found or malfunctions ob-
served, stop using the load hoisting tackle
immediately.
INCORRECT OPERATION
- Do not exceed the rated lifting capacity
(W.L.L.).
Attention:
The references given in Fig. 3,
4 and table 1, 2 with regard to shape and
material of the lifted product, should be strict-
ly observed.
- Do not tamper with lifting tackle.
- Ensure that the load centre of gravity is
located vertically below the suspension eye
in order to avoid loosening or tilting of the
load.
- Do not use the load hoisting tackle for trans-
portation of people.
- Do not lift or transport loads while person-
nel are in the danger zone.
- When transporting loads, make sure that the
load does not swing or come into contact
with obstacles.
- Do not lift or transport more than one lifting
object at a time.
- Do not magnetize the load hoisting tackle
before it has been attached to the load.
- Do not demagnetize the load hoisting tackle
unless the load has been fully lowered down
and the safe ground contact has been con-
trolled.
- Do not use the load hoisting tackle close to
strong electro-magnetic fields.
- Do not use the load hoisting tackle close to
medical units like e.g. cardiac pacemakers
or insulin pumps, as the magnetic field could
affect the function mode.
- Do not lift or transport a load unless the hand
lever of the load hoisting tackle has been
properly locked.
- Do not allow the load hoisting tackle to fall
from a great height.
INSPECTION BEFORE INITIAL
OPERATION
A competent person must inspect each load
hoisting tackle prior to initial operation. This
inspection is visual and functional and shall
establish that the tackle is in a safe condition
resp. that any defects found can be corrected
before operation commences. A service
engineer, a representative of the manufacturer
or the supplier, can make the inspection,
although the company can assign its own
suitably trained personnel.
INSPECTION BEFORE STARTING
WORK
- Prior to operation, the hand lever (Fig. 5),
which can be removed for transport purpos-
es, has to be screwed to the load hoisting
tackle.
- Ensure that the load surface, where the hoist-
ing tackle is to be attached, is free from
grease, paint or other coatings, dirt, scale
and ice and even so that the contact between
load and pole pieces is not obstructed.
Attention:
Any gap resp. any obstacle be-
tween load surface and pole pieces of the
magnet will lead to a reduction of capacity
(also refer to air gap in Fig. 3).
- Inspect the pole pieces for even surfaces
and parallelism.
- Check the entire load hoisting tackle for dam-
age, cracks or deformations.
- The hand lever must be screwed in safely
and easily movable.
- The locking feature of the hand lever must
be functional in the “ON” position and lock
the hand lever safely.
- Make sure that the weight of the load does
not exceed the maximum capacity (W.L.L.)
of the load hoisting tackle.
- Refer to Fig. 3 and observe the air gap which
has possibly resulted from coatings or other
obstacles.
- Round material, pipes, stainless steel and
castings will cause capacity reduction which
must be taken into consideration (Fig. 3, 4,
table 1, 2).
- If the pole pieces cannot be attached in full
size due to the type or shape of the lifting
material, e.g. on punched plate or corrugat-
ed sheet, the maximum capacity must be
reduced by the portion of areas which are
not in contact with the pole pieces.
- The load material must be rigid enough that
it cannot take off the pole pieces by deflec-
tion; for large size plates we recommend the
use of several load hoisting tackles in con-
nection with a spreader beam.
USING THE HOISTING TACKLE
- Place the load hoisting tackle in
demagnetized lever position “OFF” onto the
load material (Fig. 1, Fig. 2).
Attention:
Take care of good contact with
the surface of the load material and consid-
er capacity reduction possibly resulting from
an air gap and material (Fig. 3, 4, table 1,
2).
- Place hand lever in “ON” position and en-
gage safely in the locking mechanism.
The load hoisting tackle is now magnetized
and the load can be lifted.
Attention:
During lifting and transport op-
erations strictly observe the safety rules giv-
en under “CORRECT OPERATION” and “IN-
CORRECT OPERATION”.
- After completion of the lifting resp. transport
operation, make sure that the load has been
lowered down safely and cannot slip.
- Release the hand lever by pulling the locking
lever and turn to “OFF” position.
- The load hoisting tackle is now demag-
netized and can be removed from the load.
DISPOSAL
Plastic parts and non-metallic parts have to
be removed and disposed separately.
INSPECTIONS AND SERVICE
Inspections are to be made by a competent
person at least once annually unless adverse
working conditions dictate shorter periods. The
tackle is to be inspected for damage, wear,
corrosion or other irregularities and all safety
devices have to be checked for completeness
and effectiveness.
Repairs may only by carried out by specialist
workshops that use original TIGRIP spare
parts.
Inspections are instigated by the user.