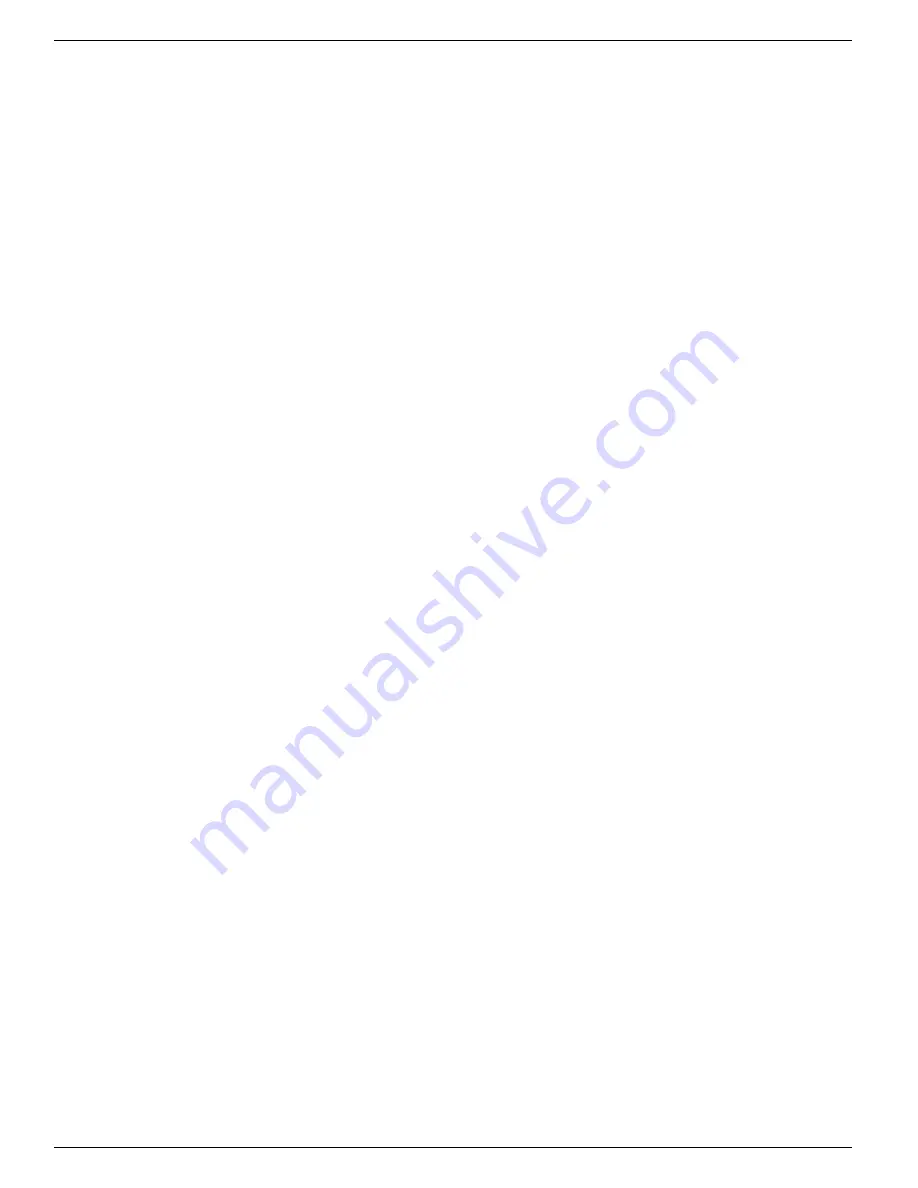
10
TROUBLESHOOTING
The following is intended as a guide to determine why the feeder may not be operating as intended. Please note that
there can be system and installation issues that can affect the operation of the feeder. This includes but is not limited to
the following:
• Piping not installed properly
• Priming and foaming of boiler water
• Faulty check valve in return header
• Delay in condensate returning to boiler
• Tankless coil leaking
Boiler is getting too much water.
a)
Cause:
There is something preventing the valve
(cartridge poppet) from completely closing.
Test:
Perform broken union test.
Solution:
Remove and inspect cartridge. Clean or
replace as necessary.
b)
Cause:
By-pass valve is leaking.
Test:
Perform broken union test.
Solution:
Repair or replace valve.
c)
Cause:
Float chamber clogged with sediment.
Test:
Open blow-down valve. If there is little or no
water flow, the chamber may be clogged with sediment.
Solution:
Remove bottom of float chamber. Clean
sediment from chamber, float and bellows mechanism.
Replace control if necessary.
d)
Cause:
Float has filled with water.
Solution:
Replace float.
e)
Cause:
Equalizing piping is plugged.
Solution:
Clean or replace piping.
f)
Cause:
Water supply is above 150 psi.
Solution:
Install pressure reducing valve to reduce
water pressure.
Boiler is not getting enough water.
a)
Cause:
There is something preventing the valve
(cartridge poppet) from fully opening.
Test:
Perform broken union test.
Solution:
Remove and inspect cartridge. Clean or
replace as necessary.
b)
Cause:
Strainer clogged with sediment.
Test:
Perform broken union test.
Solution:
Remove and inspect strainer. Clean or
replace as necessary.
c)
Cause:
Float chamber clogged with sediment.
Test:
Open blow-down valve. If there is little or no
water flow, the chamber may be clogged with sediment.
Solution:
Remove bottom of float chamber and clean
sediment from chamber, float and bellows mechanism.
Replace control if necessary.
d)
Cause:
Feed line between valve and boiler is partially
plugged.
Test:
Perform broken union test. With union broken,
there should be water flowing through the piping from
the boiler.
Solution:
Clean or replace piping.
e)
Cause:
Feed line between valve and city water supply
is plugged.
Solution:
Clean or replace piping.
f)
Cause:
Water supply pressure is less than boiler
pressure.
Solution:
Reduce boiler pressure or convert to pumped
return.