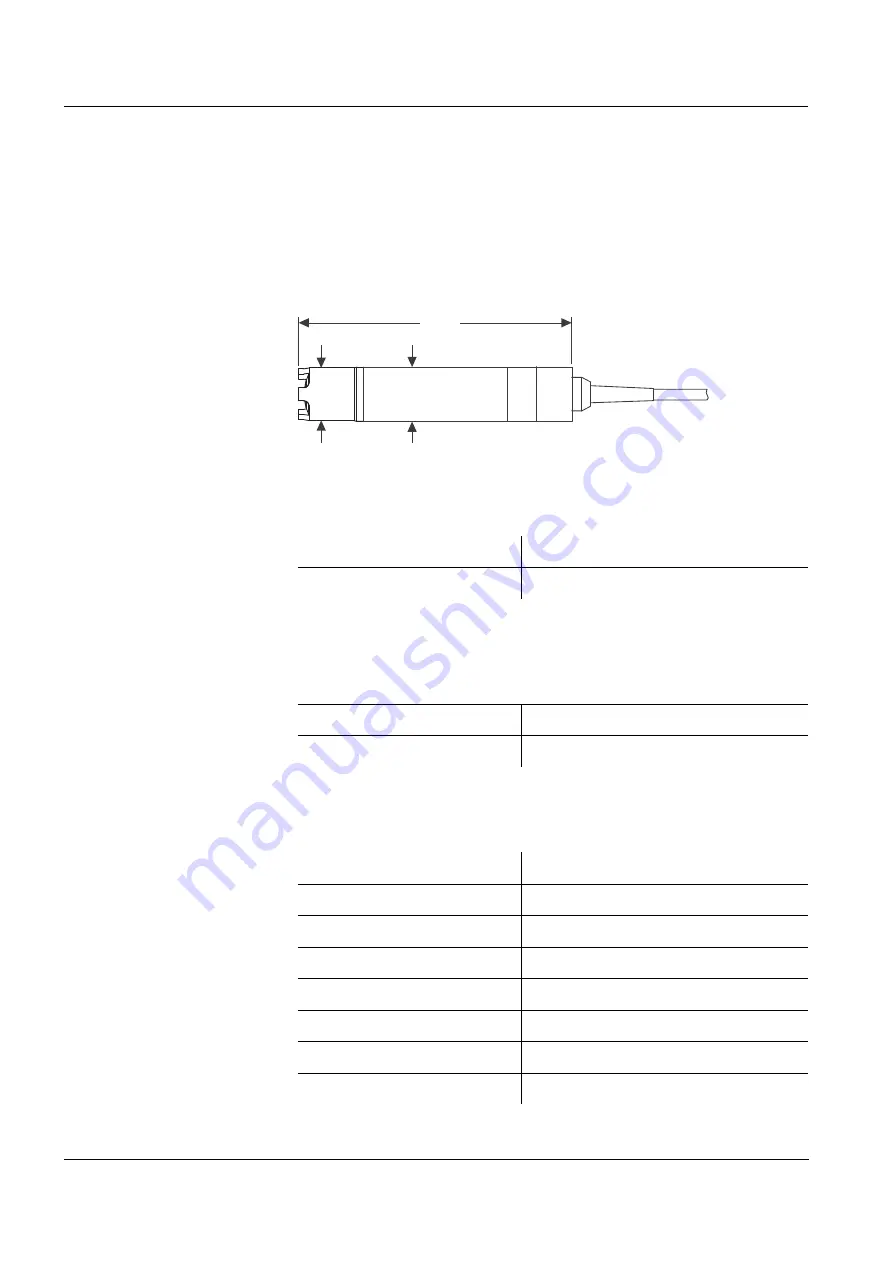
Technical data
TriOxmatic
®
690
34
ba25314e05
09/2020
7
Technical data
7.1
General data
Measuring principle
Membrane-covered amperometric sensor with potentiostatically
operated 3-electrode system
Dimensions
Weight (without sensor
connection cable)
Membrane
Electrolyte
Temperature
measurement
Temperature
compensation
Material
199
38
40
approx. 660 g
Material
Fluorine plastic
Thickness
50 µm
ELY/A
Via integrated NTC, - 5 °C ... + 60 °C
Accuracy
± 0.5 K
Resolution
0.1 K
IMT (integrated membrane temperature compensation)
Shaft
VA steel 1.4571
Membrane cap
Polyoxymethylene (POM)
Membrane
Fluorine plastic
Sensor head
Polyoxymethylene (POM)
Insulator
Epoxy, polyetheretherketone (PEEK)
Plug head connector housing
Polyoxymethylene (POM)
Protective hood
Polyoxymethylene (POM)
Closing head
POM
Содержание 201690
Страница 1: ...OPERATING MANUAL ba25314e05 09 2020 TriOxmatic 690 DISSOLVED OXYGEN SENSOR...
Страница 2: ...TriOxmatic 690 2 ba25314e05 09 2020 Copyright 2020 Xylem Analytics Germany GmbH Printed in Germany...
Страница 38: ...Technical data TriOxmatic 690 38 ba25314e05 09 2020...
Страница 39: ......