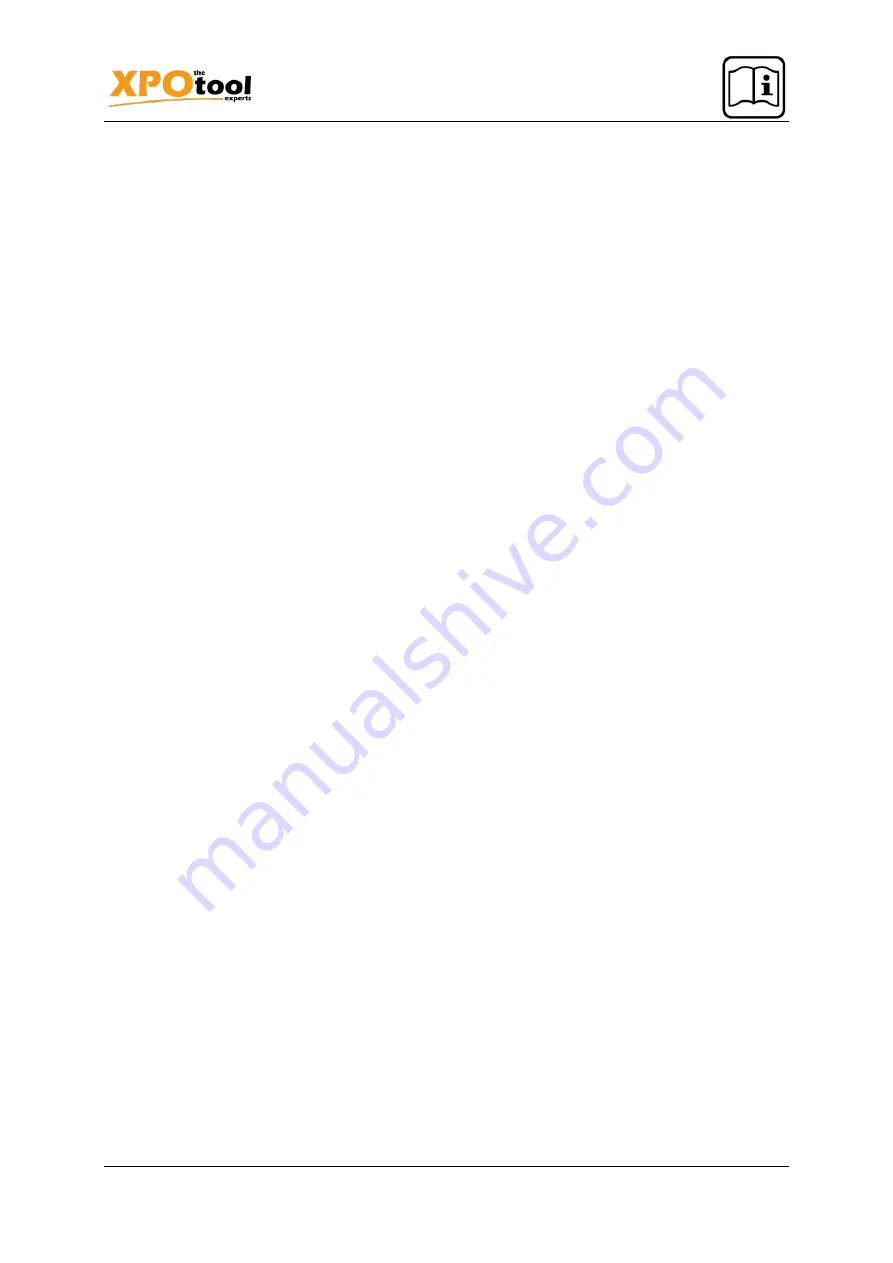
https://www.XPOtool.com
Item 63369
Page 9
The Tool Experts
09 2022-1
Choice of abrasive
The abrasive chosen influences a lot the time needed for cleaning a surface. The abrasives comprise
e.g., silicon, aluminium oxide, shore sand, and beach sand. However, shore and beach sand contain
residues of shells, corals, and other organic material, even after washing, that absorb humidity easier
than do the other materials. For this reason, the humidity inside shore and beach sands more often
provokes obstructions of the sandblaster.
Filling the tank with abrasive
1.
Check the abrasive to know if it is dry and cannot obstruct the sand dosing valve
(18B),
sand
outlet tube
(2),
hose
(24),
and other components.
2.
Put on protective clothes and protective equipment.
3.
Turn the air valve
(18)
to the shut-off (horizontal) position.
4.
Open the shut-off valve
(18C)
(vertical position).
5.
Make sure that the gauge
(15)
does not show any pressure.
6.
Remove the filler cap
(12)
on the upper side of the tank.
7.
Set in the hopper
(29)
and fill in the abrasive. Make sure that there is enough material for the
work to be done. Yet, if there is a lot to be done, only fill ¾ the tank and re-fill if necessary.
Note!
If the abrasive contains 90–100
% of water, the water separator cannot absorb the entire
humidity from a ¾ full tank. It is preferable to reduce the quantity of abrasive and to re-fill it more
often and to empty the water separator more often. Thus, the tank bottom or line will be less
susceptible for being obstructed.
8.
Close the filler cap
(12)
when the good quantity of abrasive is inside the tank.
9.
Close the shut-off valve
(18C),
then open the air valve
(18).
10.
Check if there is a leakage on the cap when you begin to pressurise the tank with the help of
the compressor.
Maintenance
1.
Protect your air compressor against damages that could be provoked by the sand blasting. It is
best to place the compressor in another room and to use a long hose to generate the pressure
needed for your work. You can also place the compressor downwind of your sandblaster. The
greater the distance between the compressor and sandblaster, the better. Apart from that, you
should respect the normal maintenance steps of your compressor.
2.
Several parts of the sandblaster wear out more quickly than others. The components that need
special attention are those that guide the air-abrasive mixture, e.g., the sand hose
(24),
fittings,
shut-off valve
(18C),
and nozzles
(27).
3.
If air is leaking from one of these components, immediately interrupt your work and find the
component to be repaired or replaced. A new sand hose
(24)
has 2 layers inside, and its walls
are ¼″ thick. When sand is guided through the hose, the walls of that will become thinner. You
may check the hose and other components exposed to the abrasive by pressurising the system
and by closing the shut-off valve
(18C).
Put your hand loosely onto the hose and pass it slowly
on the hose, fittings, and nozzles. Thus, you will be able to detect leaking spots. You can also
find the spots of the hose where its wall has become very thin. They can be found because of
the bubbles formed inside the hose. If you detect such a bubble, immediately buy a new hose.
In case one of these bubbles tears, the abrasive gets out on the side of the hose under a 4.5
bar
(65
psi) pressure or higher.
Prerequisites to the air supply
When sandblasting, a larger amount of air under a larger pressure is needed. The efficiency of your
sandblaster can be impaired by the use of too small an air hose, by the use of too little an air pressure,
or by the use of too large a nozzle.