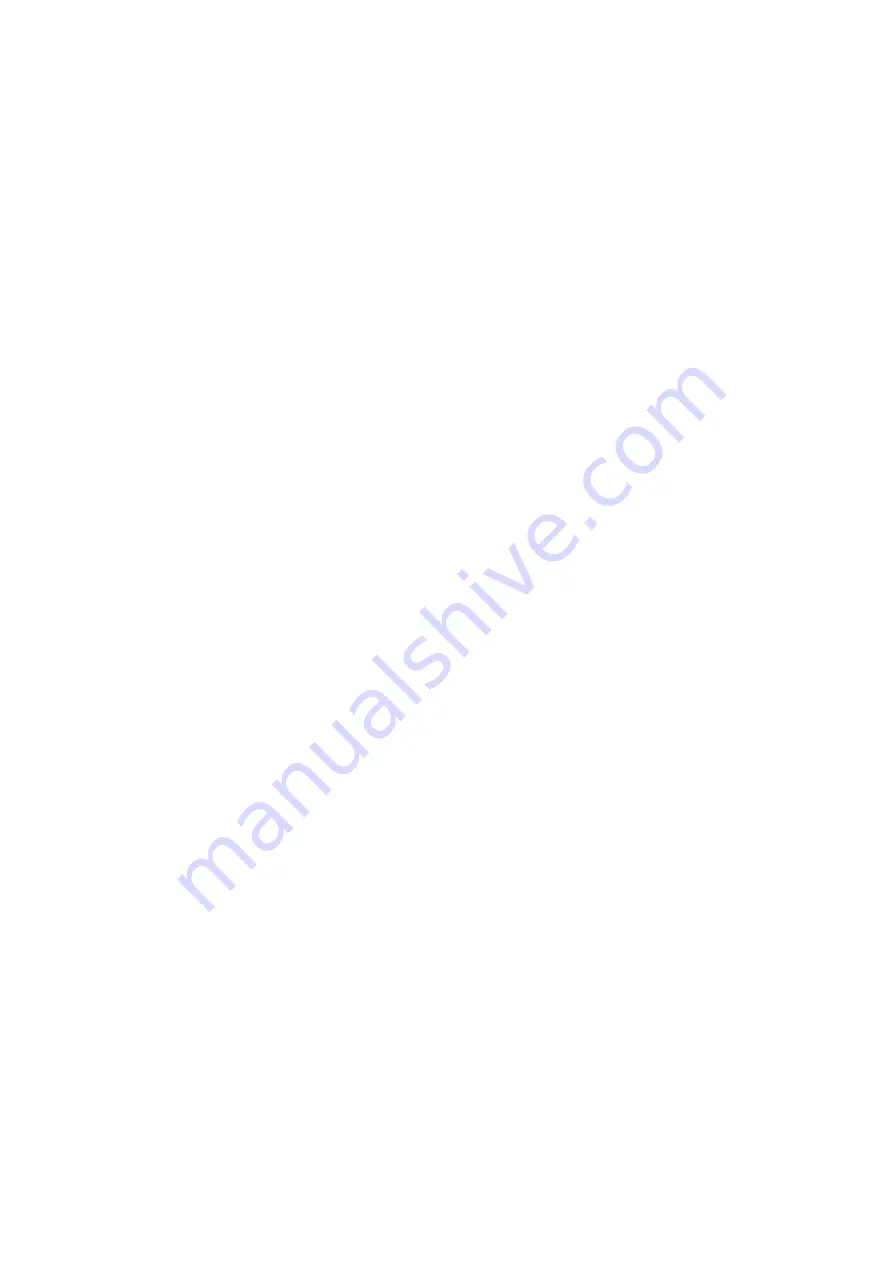
Page 38
normal use. However the user can modify these default settings to allow the engine to run opti-
mally in different conditions.
The usual acceleration setting are set to AUTO which gives the engine a good response but tries to
minimise the risk of over-fuelling in a sudden acceleration. In AUTO mode, the ECU adjusts itself
for optimum running at the current ambient conditions reported by the sensors built into the Hub,
and in extreme cases it also raises the idle speed accordingly.
Leave the acceleration and deceleration in “Auto” mode when using the engine with kerosene and
at ambient temperatures below 25ºC and elevation below 500m. If diesel fuel is used, or ambient
temperature is over 25ºC or altitude is over 500m, then the engine
perhaps
experience difficulties
in accelerating. In these cases, try setting the acceleration to “mild”, “warm” or “hot” to find a
setting where the engine operates normally, “Cold” is the fastest acceleration and “very hot” being
the slowest. You can make the selection while the engine is running to quickly see changes. It is
much better to have an engine respond slightly slower to throttle changes than one that just stop
when asked to accelerate faster than possible in difficult ambient conditions.
Exhaust tubes.
The size and placement of the exhaust tube is not an exact science. The optimum tube diameter
and the gap between the engine exhaust and the tube intake is largely dependent of the airframe.
An slow airframe with big intakes will benefit of larger exhaust diameter and larger gap, to get the
maximum static thrust possible, while a fast airframe, with small intakes, bypass installation, will
benefit of smaller exhaust diameter and smaller gap, to get the maximum efflux speed.
Use an exhaust tube of a diameter equal as shown on the specifications chart, with a gap between
the engine exhaust and beginning of exhaust tube (excluding the bell mouth) of 25mm (1”). Later
you can experiment moving the engine 5mm (0.2”) forward or aft to see if performance is better.
Too larger gap will cause hot gases to recirculate to the engine intake, decreasing performance
and worsening the acceleration. Too short gap will cause extra pipe noise and depression inside
the pipe, in extreme cases the exhaust tube can collapse due the low pressure inside (venture
effect).
Use in gliders and in 3D planes.
If you plan to use your engine in a glider, please consider to de-rate your engine. The typical large
glider use that is running at full power continuously for the entire flight in airframes that easily
weight 4 times the engine thrust is very hard for the engine, as the internal elements like combus-
tion chamber are subjected to maximum temperature and stress all the time, reducing the time
between overhauls. We would recommend using the engine at 80% of its maximum power in
these conditions, or using the 100% for takeoff, but later reducing to 80% during continuous climb.
We don’t recommend using our engines in 3D planes doing fast acrobatics. The gyroscopic forces
that a turbine rotor turning at very high RPM´s apply to the bearings doing a loop in less than 1s
are extremely high and can destroy the bearings or cause the compressor or turbine wheels to rub
to the engine case.
List of ECU message codes
Here is a list of possible messages shown on the data terminal screen and their meaning.
1.
TrimLow:
Indicates that the signal received from the transmitter corresponds to the low-
ered trim, that is to say, engine OFF.