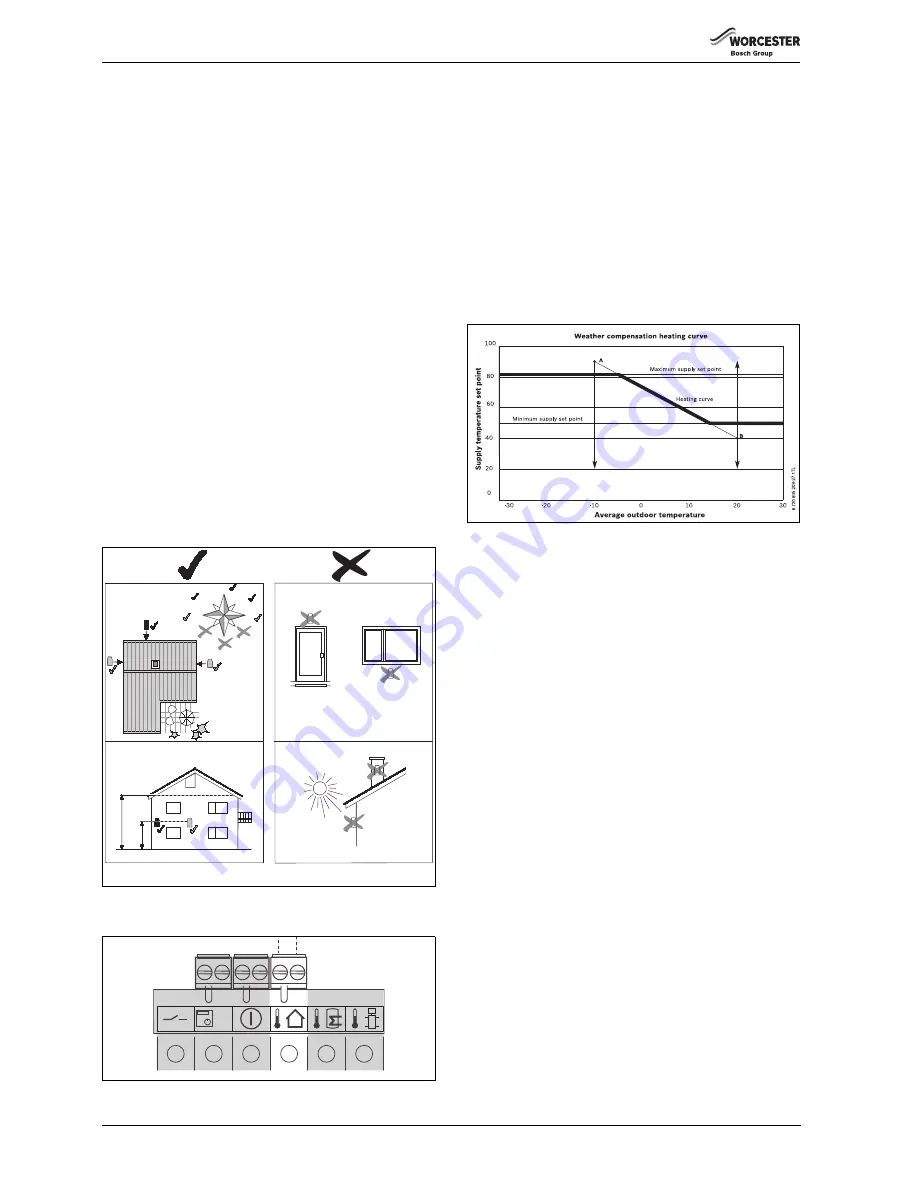
Installation
Greenstar Heatslave II External
ErP -
6 720 813 345 (2014/09)
24
5.11
Weather compensation
The appliance will modulate the CH flow temperature based on the
outside temperature when an outdoor sensor is connected to the
outdoor sensor connection on the control board and the weather
compensation is active.
This is designed for use with a system that has thermostatic radiator
valves and a room thermostat.
The appliance will operate at lower temperatures when there is a lower
heat load because the building is losing less heat due to higher external
temperatures. This means that the appliance is running more efficiently
as it is operating for longer at condensing temperatures.
The weather compensation curve can be adjusted to tune the flow
temperature to suit the particular installation.
The appliance is supplied with the weather compensation deactivated.
Weather compensation activation
The weather compensation is activated via menu 1 of the text display.
▶ Select Menu 1 via ▲ ▼ scroll buttons.
▶ Press OK button.
▶ Select W1 via ▲ ▼ scroll buttons.
▶ Press OK button.
▶ Set W1 to 1 via ▲ scroll button.
▶ Press OK button.
The weather compensation is now active and the appliance will check for
the presence of an outdoor sensor and deactivate the CH flow
temperature modulation if a sensor is not detected. When weather
compensation is activated but an outdoor sensor is not fitted/detected,
the warning triangle and H03 will be displayed on the LCD display.
Fig. 37
Weather compensation sensor optimum siting indicated by black tick.
Fig. 38
The sensor is wired directly into the control box via terminal 4 in the low
voltage terminal strip (
page 22).
The heating curve
The CH flow temperature has an upper limit of 82°C (this can be capped
via the CH control knob setting) and a lower limit of 50°C, (it is
recommended that the CH knob is set to 82°C for the weather
compensation to operate most effectively).
The default settings for the curve are point A = 90°C and point B = 40°C,
this gives a 80°C flow at -4°C outdoor temperature and a 50°C flow at
14°C outdoor temperature which should be suitable for typical systems.
Point A is the projected value for the flow temperature at -10°C outdoor
temperature and point B is the projected value for the flow temperature
at +20°C outdoor temperature, (these values dictate the angle of the
slope only they are not CH flow temperature limits).
Adjusting the heating curve
▶ The weather compensation curve can be adjusted via the text display
by adjusting the projected flow temperature at -10°C (point A), Menu
1 W2 (pA), and 20°C (point B), W3 (pB), enabling the slope as well
as the position of the curve to be adjusted to suit the installation.
▶ Point A and B can be set between 90 and 20°C but point A must
always be greater than point B.
Outdoor sensor error
▶ If during weather compensation the outdoor sensor is open circuit or
closed circuit the CH flow temperature modulation is deactivated and
the CH flow temperature set to the CH control knob setting, a warning
triangle and H03 are displayed on the LCD.
▶ The appliance will monitor the outdoor sensor input and if the sensor
returns to normal then the flow temperature modulation will be
reactivated and the LCD warning triangle and H03 are turned Off,
(there may be a 10 second delay).
Average outdoor temperature
▶ To stop rapid fluctuations the outdoor temperature used for CH flow
temperature modulation is an average value taken over a ten minute
period.
▶ When an outdoor sensor is first detected the sensor value is taken to
be the outdoor temperature, subsequent to this the outdoor
temperature will be adjusted every 10 minutes using an average
outdoor temperature value from the previous 10 minute period.
Frost protection
The normal condition for the appliance is that the weather compensation
frost protection is turned Off.
If required the frost protection is activated via Menu 1 W5 of the text
display, 0 = OFF, 1 = ON.
On Activation of the weather compensation frost protection if the
outdoor temperature is less than 5°C the system frost protection is
activated the same as if an external frost thermostat was activated.
1
/
2
H
(min 2m)
H
N
S
W
E
NW
NE
SW
SE
6 720 805 209-25.1TL
EMS
1
2
3
4
5
6
6 720 805 209-26.1TL