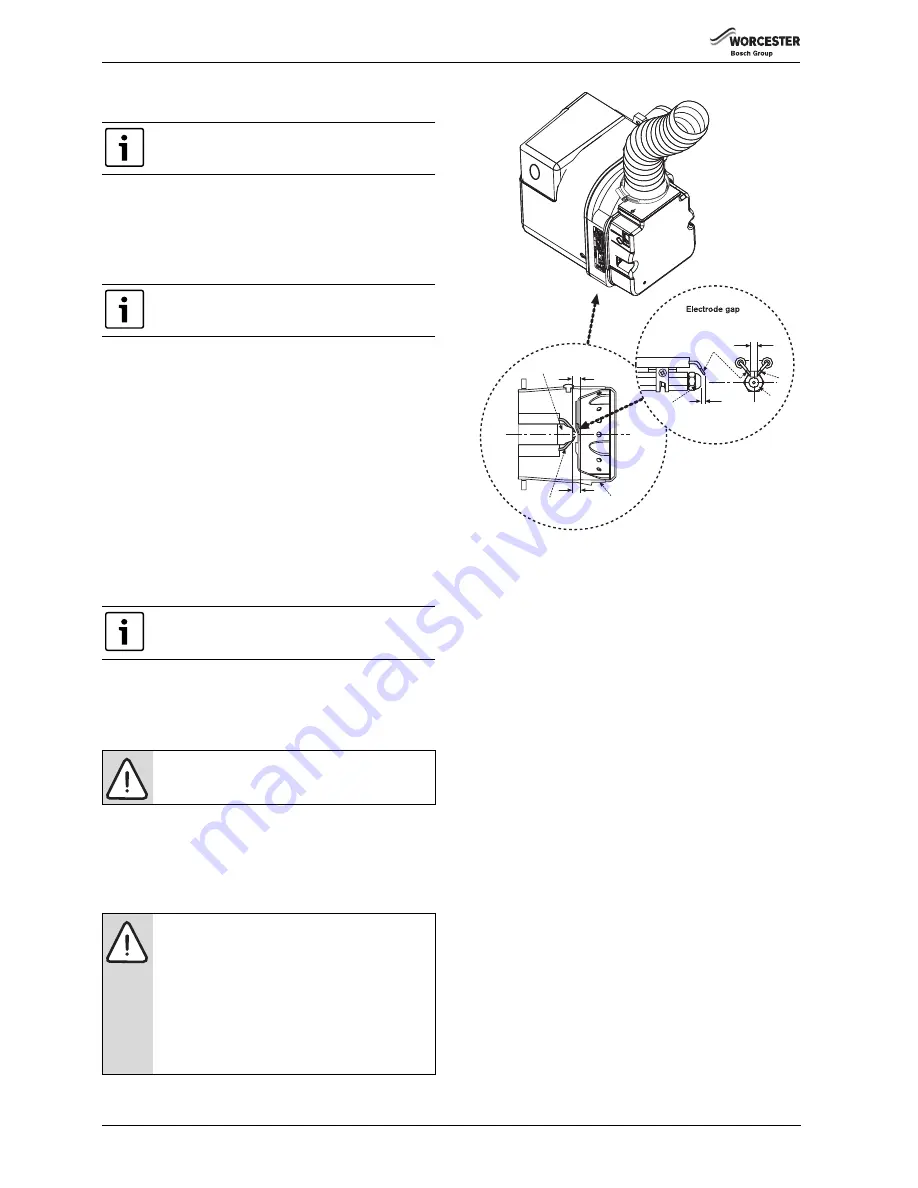
Installation
Greenstar Heatslave II External
ErP -
6 720 813 345 (2014/09)
20
Water connections
▶ Ensure all pipework is clean.
▶ Align water pipework and connect
▶ Check that all unused sockets have been capped.
Oil supply connections
▶ Route the oil supply pipe [W] along either side of the boiler as
required and connect to the isolating valve [G] and ensure the valve
is closed.
▶ Connect the flexible oil hose [H] to the isolating valve [G].
Condensate connection
▶ Connect 21.5 mm polypropylene pipe [L] (not supplied) to the
condensate waste pipe flexible push fit connector [K] and terminate
to waste.
▶ Do not use any solvents, adhesives or lubricants when pushing the
pipe into the rubber connector [K].
▶ Ensure that the condensate pipe runs away from the boiler at a
constant fall of 52mm (min.) for every metre.
▶ Seal all condensate pipe joints.
▶ Carefully pour 500ml of water into the condensate collection [U] to
fill condensate trap.
▶ Check the water is running away and the condensate pipework joints
are water tight.
▶ Check the flue manifold seal is undamaged and seated correctly.
▶ Refit flue manifold access cover [T] and secure with screws [S].
Pressure relief connection
▶ Connect the pressure relief pipe [N] to a copper discharge pipe
(15mm Ø min.).
5.7
Oil burner and pump
Oil burner
1. Check that the nozzle (A) and the electrode (B) alignment settings
are correct as shown in figure 30.
▶ Ensure that the nozzle (A) is aligned centrally within the combustion
head (C).
▶ Inspect for any visible defects.
Fig. 30 Nozzle and electrode alignment
Oil pump
Connecting the oil pump for a single pipe system:
▶ The pump is factory set for single pipe operation with the flexible oil
pipe fitted.
▶ Check connections before use.
Converting the oil pump for a double pipe system:
1. Check the inlet pipe connection (1).
▶ Unscrew return plug (2).
▶ Screw in by-pass screw (3) which is attached to the oil pump.
2. Connect the flexible oil pipe return hose (not supplied) to the oil
pump and return pipe fixing and tighten to secure (for routing see
figure 29).
That surplus water may be present due to factory testing.
Replace flexible hose at annual service to prevent
possible oil leakage.
The condensate trap must be correctly filled to prevent
the possibility of potentially harmful flue products
escaping via the condensate pipework.
CAUTION: MAINS SUPPLIES
▶ Isolate the oil & water mains supply before starting
any work and observe all relevant safety precautions.
NOTICE: IMPORTANT INFORMATION
▶ Before removing or fitting a nozzle (A), loosen screw
(6 figure 31) and move the electrodes (B) forward.
After refitting check that the electrode gaps are
correct, as shown in figure 30.
▶ Whenever replacing the combustion head, ensure
that the photocell is lined up with the sight hole.
▶ The 12/18 model has a brass deflection washer and
locating circlip behind the nozzle. These must be in
place for the correct operation of the burner.
A
B
C
A
B
A
B
1.
5mm
2.0 - 2.5mm
3.5 - 4.0mm
5mm
6720805460-38.1Wo