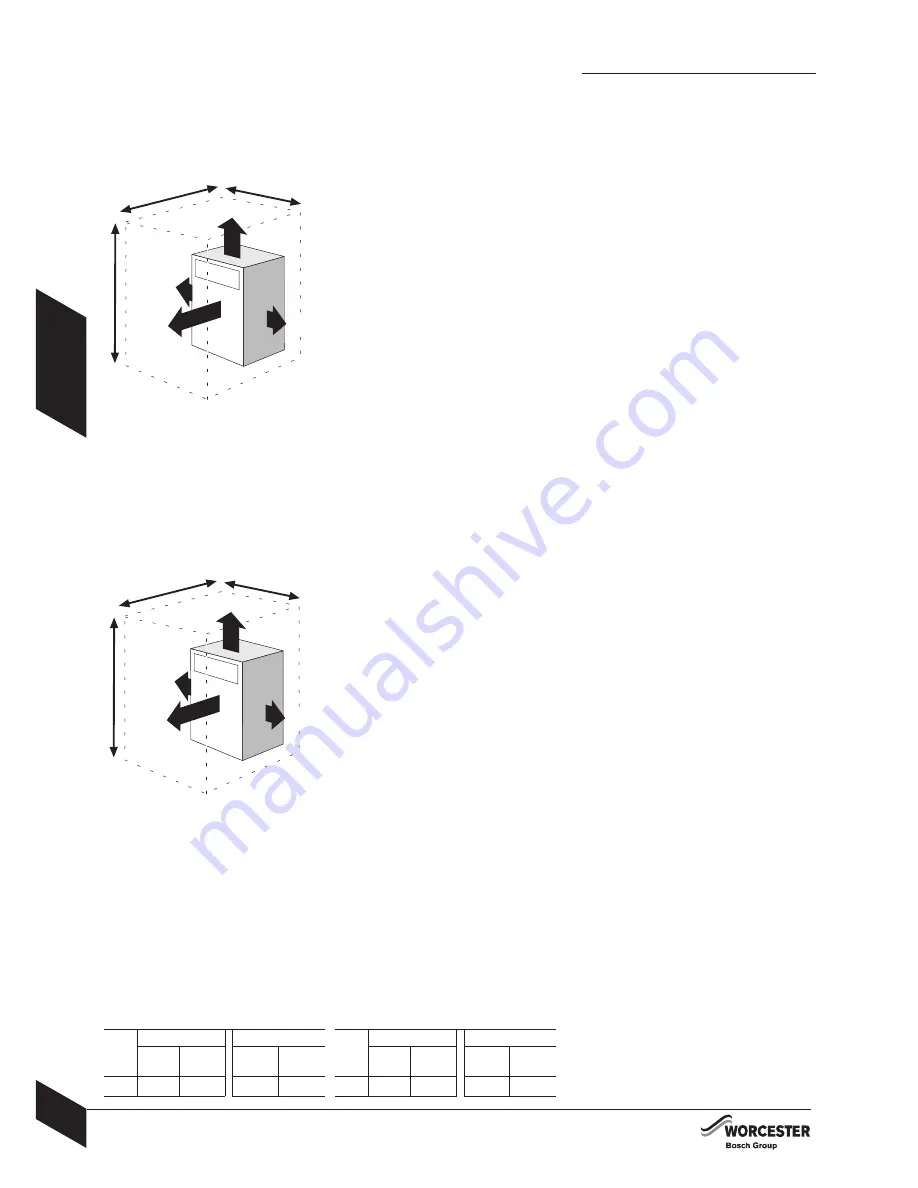
PR
E-
IN
S
TA
LL
AT
IO
N
INSTALLATION & SERVICING INSTRUCTIONS FOR WORCESTER BOSCH
12
BOILER LOCATION & CLEARANCES
8-716-106-252a (03.05)
BOILER LOCATION &
CLEARANCES
This boiler is only suitable for installing internally
within a property at a suitable location onto a
fixed rigid non-combustible surface of the same
size as the boiler and capable of supporting the
boiler weight.
The boiler must be installed on a flat level surface
to ensure condensate does not enter the primary
heat exchanger.
The boiler is not suitable for external installation
unless a suitable enclosure is provided.
Roof space installations must fully conform to
BS5410 part 1 section 4.6.9
Open flue model (CF):
In order to ensure clean and efficient combustion
an adequate supply of air must be delivered to
the combustion chamber.
To provide sufficient air a suitable inlet must be
provided into the room or space in which the
boiler is situated, minimum size 110cm² for
18/25kW appliances.
An air brick or other form of continuous air supply
may have to be built into the installation in order
to ensure an adequate supply of air.
If the appliance is to be installed in a confined
space or compartment two air vents are required,
one at high level and one at low level.
The minimum free area of each vent is shown
opposite and depends whether the air is taken
from another room or from outside the building.
Where the air is taken from another room that
room must contain an air inlet as described
above.
Room sealed balanced flue model (RS):
The appliance does not require a separate vent for
combustion air.
Installation in cupboards or compartments require
permanent vents for cooling purposes, one at
high level and one at low level, either direct to
outside air or to a room.
Both vents must pass to the same room or be
on the same wall to the outside air.
The minimum air vent free area is given in the table
opposite.
a: INSTALLATION CLEARANCES:
Diagram (a) shows the minimum space
recommended to
install
the boiler only.
b: SERVICE CLEARANCES:
Diagram (
b
) shows the minimum space required to
service
the boiler only.
The appliance is suitable for an under worktop
installation providing that the worktop above the
boiler (min.10mm clearance) is removable for
maintenance and the front of the boiler is not
enclosed.
* Remove the flue 'knock-out' panel sections if this
clearance is less than 75mm.
600mm
300mm
100mm
100mm
720mm
1200mm
11
55mm
a: RECOMMENDED
INSTALLATION CLEARANCES
b: SERVICE CLEARANCES
600mm
300mm
5mm*
5mm*
720mm
1200mm
11
55mm
Conventional flue:
Room Sealed flue:
MINIMUM AIR VENT AREA (cm²) FOR APPLIANCES INSTALLED IN A COMPARTMENT:
Internal
1
ventilation
High
Level
Low
Level
kW
External
2
ventilation
High
Level
Low
Level
18/25220
330
110
220
18/25220
220
110
110
Internal
1
ventilation
High
Level
Low
Level
kW
External
2
ventilation
High
Level
Low
Level
1
Internal air to and from a space/room inside the building.
2
External air to and from directly outside the building