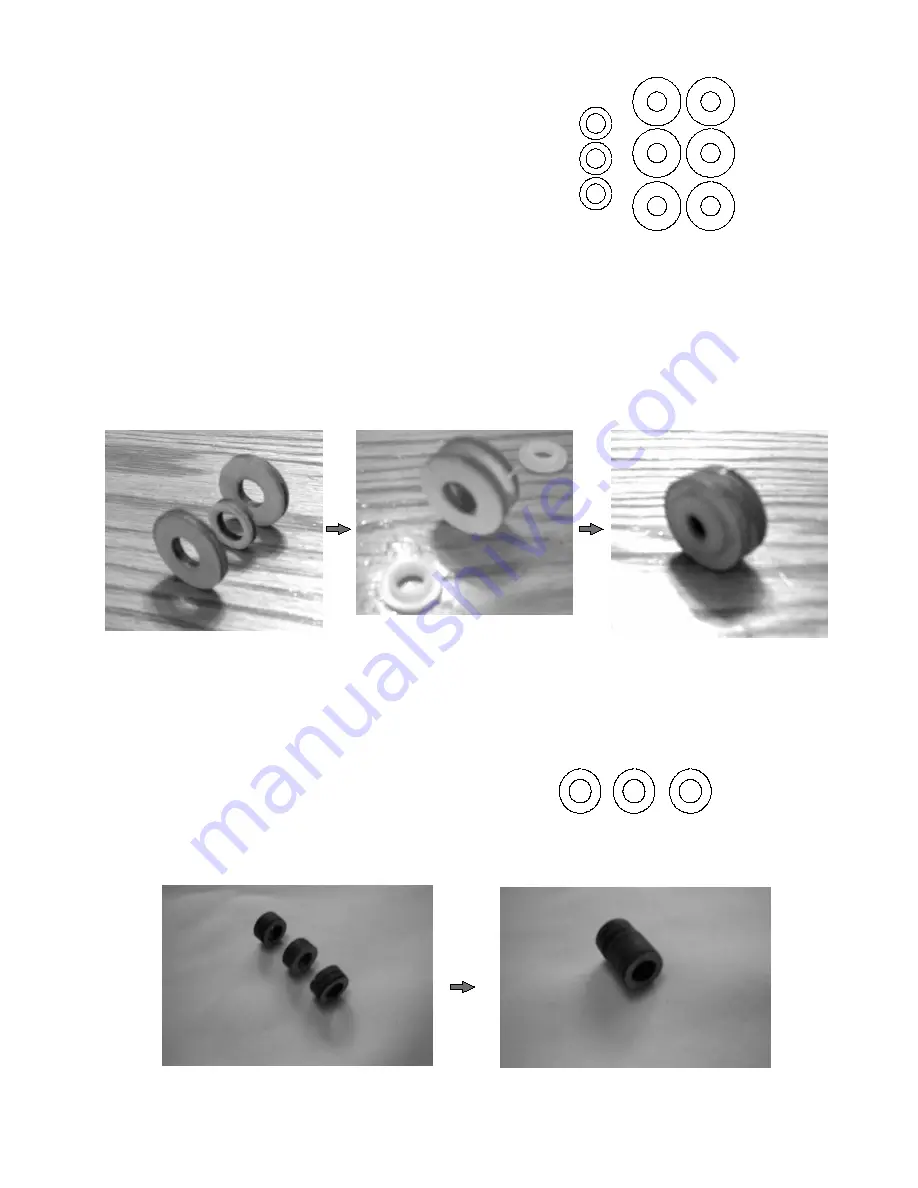
7
48
51
51
Pulley Wheel Assembly
Parts (for three identical pulley wheels)
3 - Pulley hubs (#51)
6 - Pulley wheel sides (#48)
6 - Nylon shoulder washers
Assembly Procedure
1) Glue together the three pulley pieces with the smaller diameter pulley hub (#51) sandwiched
between the two larger pulley wheel sides (#48) with all three holes aligned. After the glue has dried,
the pulley edges can be sanded and finish applied. Next, apply a small amount of glue around the rim
of the hole in both pulley faces and insert a nylon shoulder washer. It might be necessary to either
press the washer firmly into place or to tap it into place with a hammer. Be sure the washer seats
completely into the hole. Repeat this process twice to make a total of three identical pulley wheels.
Hour Pipe
Parts
3 - Hour pipe sections (#37)
Assembly Procedure
Glue together the three hour pipe sections (#37). Clear any glue squeeze out from the center.
Содержание The Tranquility Clock
Страница 1: ...The Tranquility Clock Copryight 2014 Jeffrey A Schierenbeck ...
Страница 43: ...42 ...
Страница 44: ...43 Part Locator To be removed from the manual ...