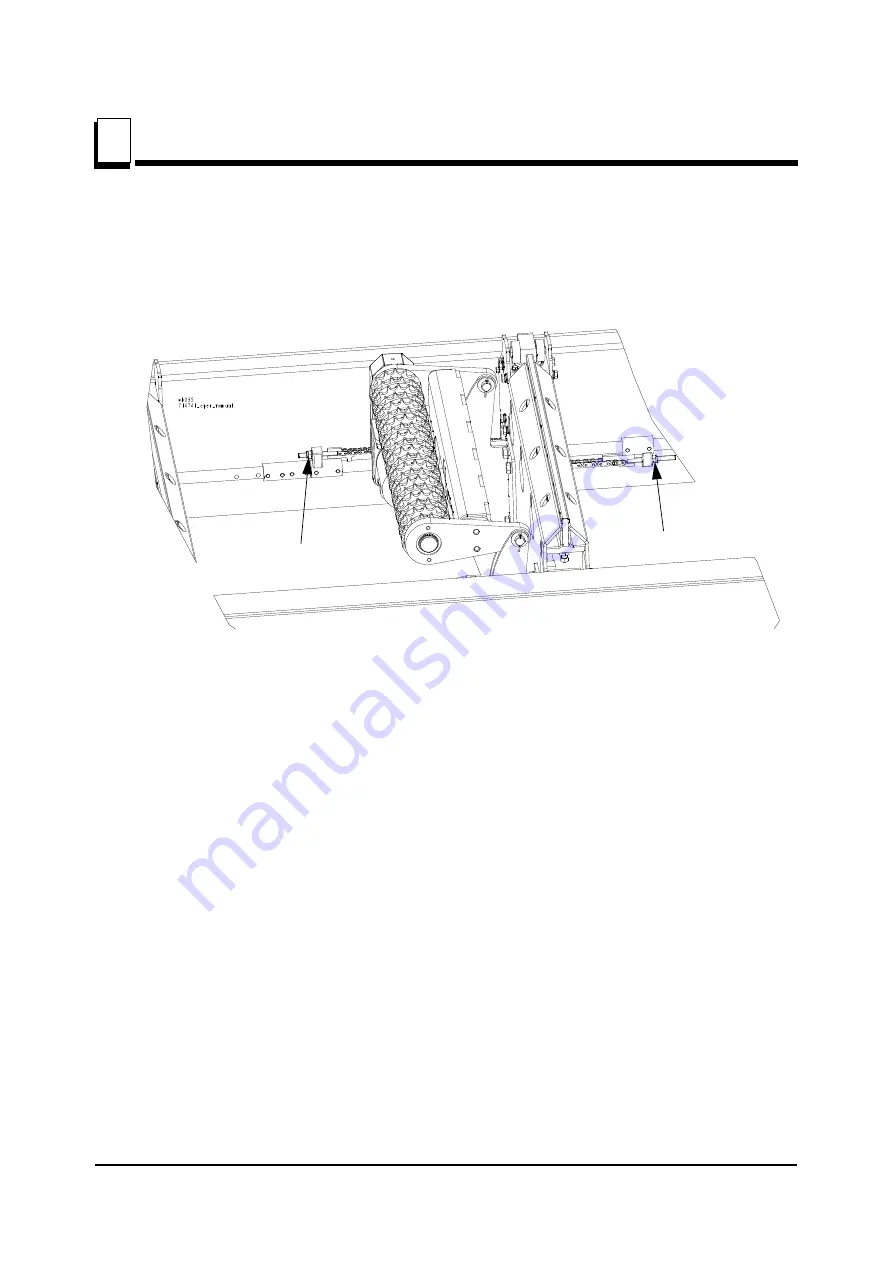
Alignment
Adjustment of the Side Supports
6
6-16
doc013119
Alignment
6.1.20
Adjustment of the Side Supports
Adjust the side supports so they stop at the upper and lower limits at the same moment.
See Figure 6-21.
To adjust the side support, use the adjustment nuts shown below.
Adjust both chains evenly so they do not have slack.
FIG. 6-21
Adjustment Nut
Adjustment Nut
Содержание Titan WB2000-EC
Страница 1: ......
Страница 2: ......
Страница 30: ...Setup Operation Sawmill Setup 4 4 4 EGdoc013119 FIG 4 3 WB2000 hes_017_A Lifting brackets...
Страница 64: ...Maintenance Cleaning and Maintenance 5 5 3 EGdoc013119 Debarker in out drive belt cover See Figure 5 2 FIG 5 2...
Страница 65: ...Maintenance Cleaning and Maintenance EGdoc013119 5 4 5 Blade drive belt cover See Figure 5 3 FIG 5 3...