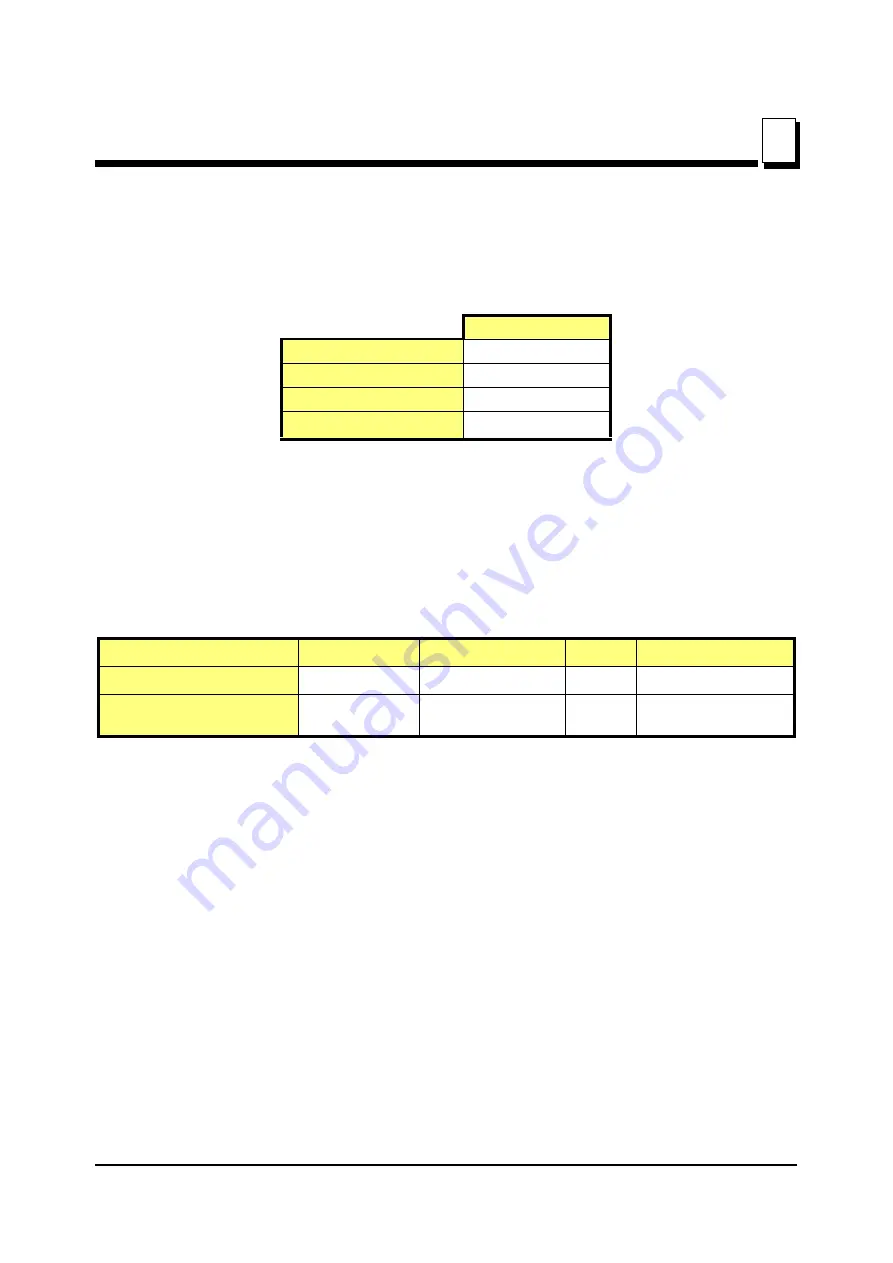
Specifications
Overall Dimensions
Specifications
60HDdoc011304
7-2
8
8.2
Overall Dimensions
See Table 8-1.
The overall dimensions of the LT80HD are listed below.
8.3
Engine/Motor Specifications
See Table 8-2.
The power options available for the LT60HD/70HD/80HD Super sawmills
are listed below.
LT80HD
Length
10,8 m
Width
2,3 m
Height
2,3 m
Weight
1
1
Weight with optional trailer and heaviest engine
option.
2780 kg.
TABLE 8-1
Engine/Motor Type
1
1
Use diesel fuel for D42.
Manufacturer
Model No.
Power
Other Specifications
42HP Diesel
Kubota, Japan
V1505-TE
42KM
4 cylinders, 1498 cm
3
25HP Electric Motor
2
2
The electric motors supplied on Wood-Mizer sawmills carry a rating assigned by the motor manufacturer
for the continuous duty operation of the motor, potentially, 24 hours per day, day after day. This rating is
useful in sizing motors for use in applications like blowers for heating and ventilation that are never cycled
off except for system maintenance.
Indukta SA,
Poland
Sg 160L-2
18,5kW
33,8 A, 2930 RPM
TABLE 8-2