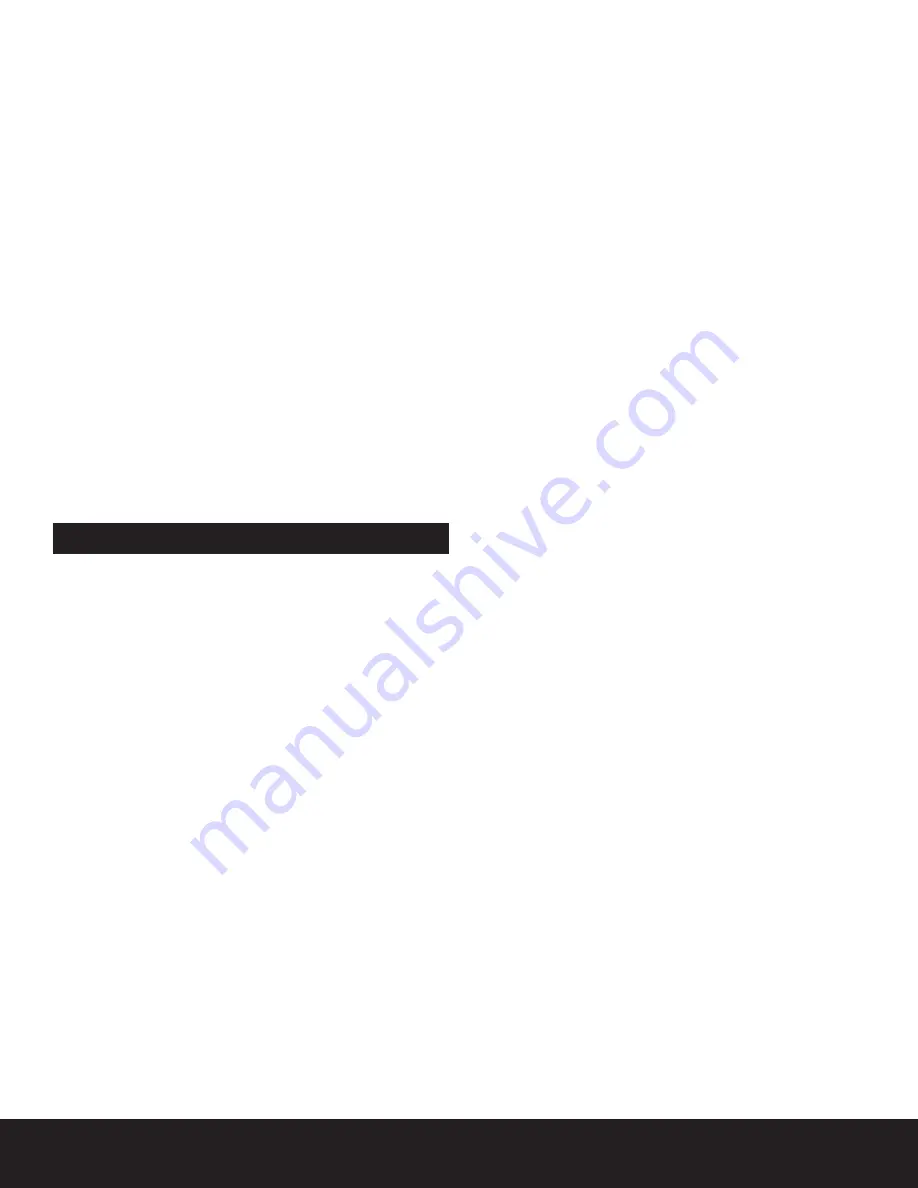
3
• Have a vapor barrier.
• Have gaskets wherever the door meets the kiln; this
will give a good, airtight fit.
• Have a scraper type weather strip to reduce air
leakage if door sill is not present.
• Close tightly against the gasket using turnbuckles,
tarp straps, lag studs with wing nut, etc.
Remember: There will be considerable expansion and
contraction during kiln use, plan door construction
accordingly.
While outside electronic moisture meters can be
used to avoid entering the kiln, during the drying
cycle,
Wood-Mizer
strongly recommends regular
checks inside the kiln to visually inspect the
surface or end checks, mold, stain and to check
with a hand held meter.
Step 4: Cover Thermax with one or two layers of
6 mil polyethylene, then enclose with ½” CDX or
marine grade plywood.
Step 5: Coat CDX interior surface with “mobile home
or metal roofing aluminum paint”
Paint is an asphalt based coating with powdered
aluminum and fiber for strength, available in
hardware stores. Re-coat as necessary every year.
Step 6: Finish exterior walls to suit your tastes, but
avoid galvanized steel or other ferrous sidings.
Once you have completed construction of the kiln
chamber install the following air deflectors and
baffles to control the airflow within the chamber.
• Corner deflector typically made of plywood used to
help turn the airflow.
• Hinged baffle that falls from the fan wall, to be held
up during load with a nylon rope. Hinged baffles
compensate for different load sizes, and allow for
shrinkage of the board pile.
• Baffle that closes in the open space for lumber that
does not fill the entire width. This baffle can be fixed
or portable.
Do not underestimate the effect of this baffling, as
correct baffling will pay off in more even drying and
faster drying. This more than offsets the extra time
and effort to correctly place the baffles.
Please reference Figure 1-2 for more information on
deflectors and baffles.
Please reference Figure 1-1 for more information on
construction.
Step 1: Build all walls, ceilings and floors with a 2” x
4” framework, with blue or pink Styrofoam (extruded
polystyrene) friction fitted between the studs.
Step 2: Cover the interior face of the studs with a 1”
layer of Celotex Thermax (or for better results two
overlapped ½” layers).
Celotex Thermax is foil faced polyisocyanurate
(urethane) board which is orange or yellow in
color and is available in 4’ x 8’ sheets of various
thicknesses. Celotex Thermax is a trade name and
similar and acceptable products are available under
other trade names.
If you want to use spray foam insulation, urethane
based only applied at 2.2lb/cu ft. Fiberglass is never
recommended.
Step 3: Caulk joints and nail heads with high
temperature silicone (optional: apply aluminum tape
over silicone)
Construction Guidelines
Wood-Mizer
KD150 12/22/17
Содержание KD150 Series
Страница 2: ...KD150 12 22 17 ...
Страница 6: ...Service Log Issue Description Date Servicer KD150 12 22 17 ...
Страница 15: ...9 Figure 1 5 Kiln Chamber Wall Details Wood Mizer KD150 12 22 17 ...
Страница 16: ...10 Figure 1 6 Kiln Chamber Front Elevation Wood Mizer KD150 12 22 17 ...
Страница 17: ...11 Figure 1 7 Kiln Chamber Door Framing Wood Mizer KD150 12 22 17 ...
Страница 18: ...12 Figure 1 8 Kiln Chamber Door Section E Wood Mizer KD150 12 22 17 ...
Страница 19: ...13 Figure 1 9 Kiln Chamber Door Section F Wood Mizer KD150 12 22 17 ...
Страница 21: ...15 Figure 1 11 Door Gasket Installation GASKETS AND DOOR KITS AVAILABLE Wood Mizer KD150 12 22 17 ...
Страница 47: ...41 Notes Wood Mizer KD150 12 22 17 ...