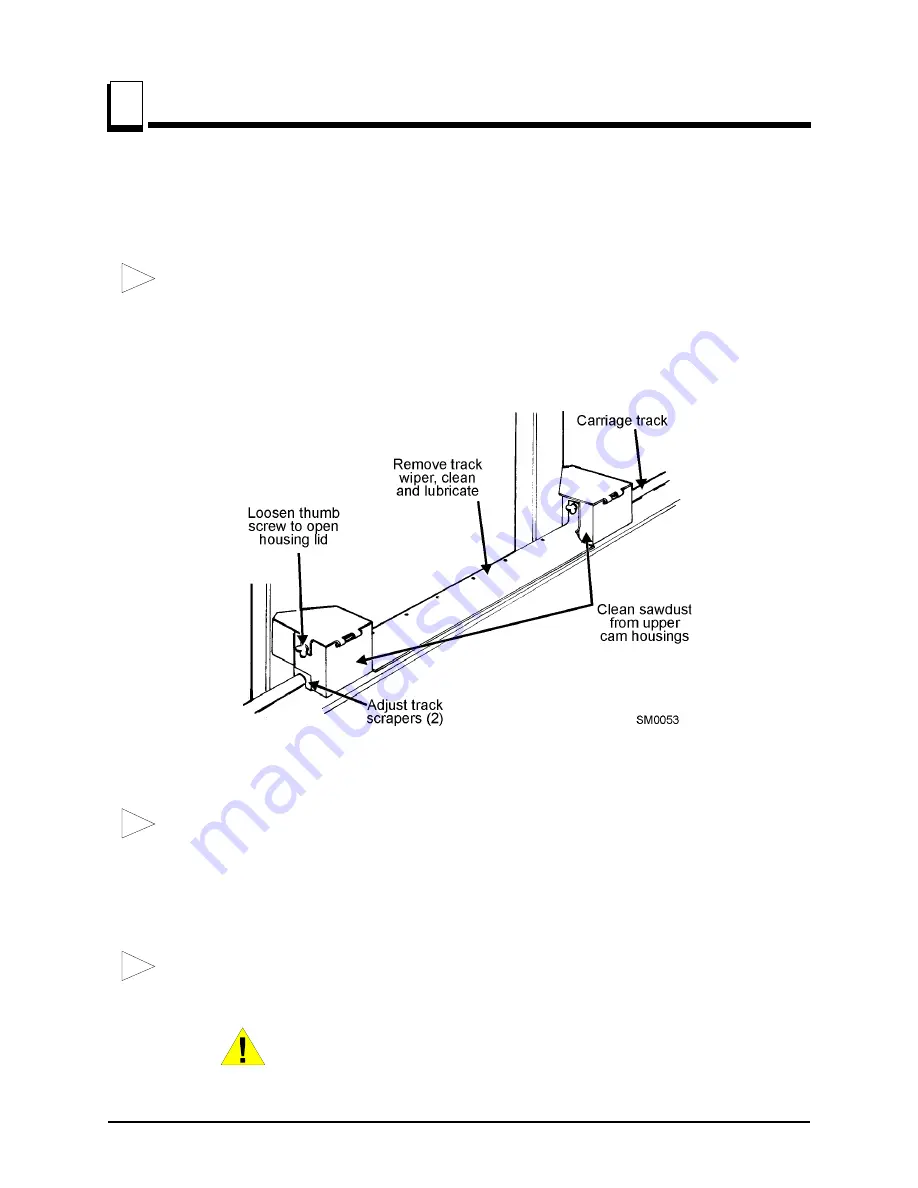
Maintenance
Carriage Track, Wiper & Scrapers
3
3-4
3087doc041610
Maintenance
3.4
Carriage Track, Wiper & Scrapers
See Figure 3-3.
1.
Clean the upper and lower track rails to remove any sawdust and sap buildup every eight
hours of operation. Lubricate the lower track rail by wiping it with Dexron III ATF.
NOTE:
Apply a rust inhibitor such as Sherwin-Williams P.D.R.P #710 when the sawmill is
not in use. Use a clean, dry cloth and a light lubricant such as WD-40 to remove the pro-
tection coat before operating the sawmill.
2.
Remove sawdust from the upper cam housings. Loosen the thumb screws on the upper
cam housing covers and open. Brush any sawdust buildup from the housings.
3.
Check the track scrapers as needed. Make sure the scrapers fit firmly against the rail. If a
track scraper needs to be adjusted, loosen the thumb screw, push the scraper downward
until it fits firmly against the rail, and retighten the thumb screw.
4. Rev. AL+:
Clean and lubricate the track wiper every twenty-five hours of operation.
Unbolt the wiper, remove it from the sawmill, and remove any sawdust buildup. Soak the
felt wiper with Dexron III transmission fluid, 10W30 motor oil or 3-in-1 turbine oil. Replace
the wiper.
NOTE:
The track oiler/wiper can be retrofitted to sawmills before revisions AL.
CAUTION!
Reinstall the wiper so that it lightly touches the
track rail. If the wiper presses too firmly against the rail, it
can cause the power feed to bind.
FIG. 3-3
8
8
25
Содержание 1987 LT30
Страница 5: ...3087doc041610 v V I N LOCATIONS 1989 V I N DESCRIPTION 1989 ...
Страница 6: ......
Страница 10: ......
Страница 68: ......
Страница 110: ......