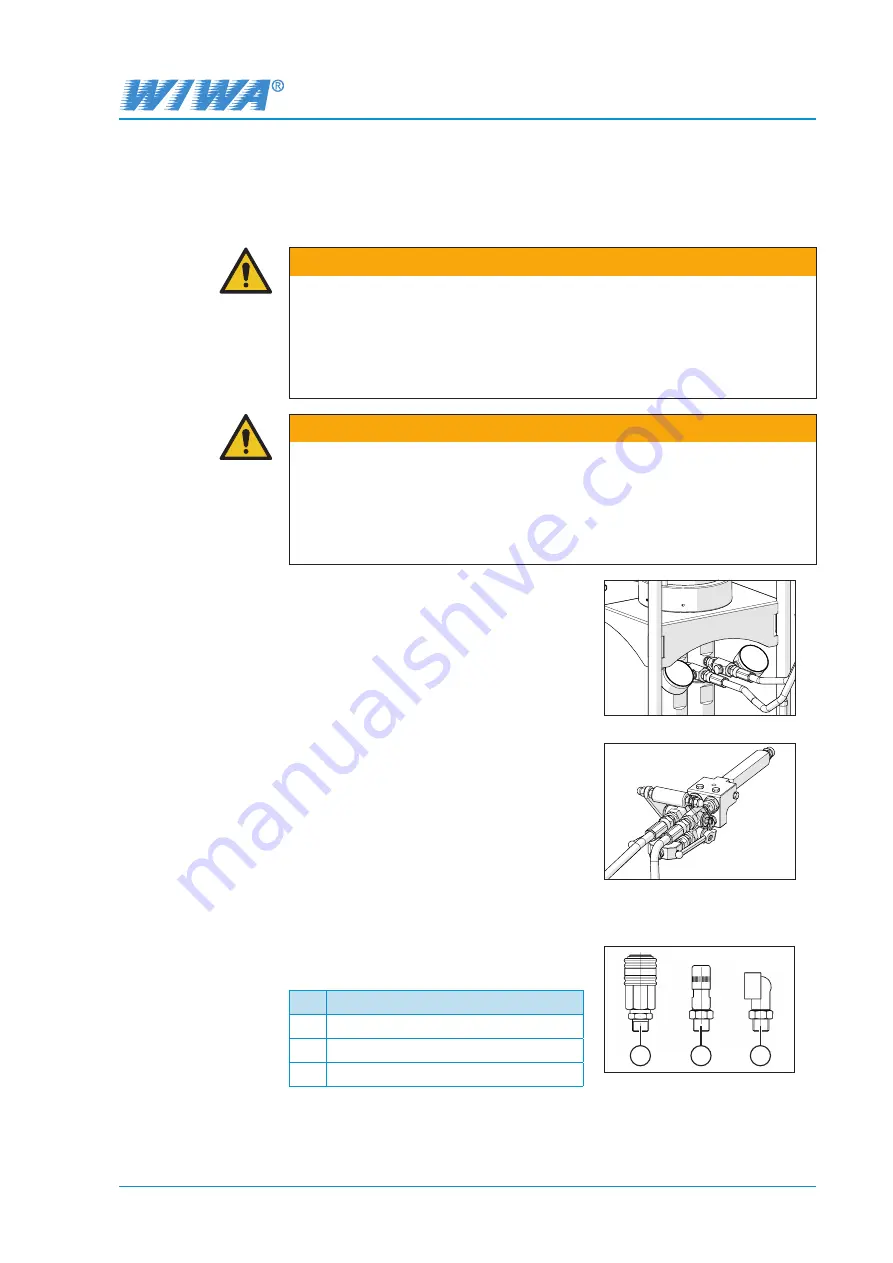
Original operation manual
2K GEL UNIT
23
2KGel_14025_25015_BAoDB_en_1701 • rs
Transport, installation, and assembly
4.3.1 Installing the material hose and mixing unit
If the machine is delivered with WIWA material hoses and a WIWA mixing unit,
observe and follow the information in this chapter.
WARNING
Parts that are not designed for the maximum permissible working pressure
of the machine may rupture and cause serious injury.
➤
Prior to installation, check the maximum permissible working pressure of
the material hoses and the mixing unit. It must be greater than or equal
to the maximum working pressure of the machine stated on the type
plate.
WARNING
If the connections for the hoses are subjected to strain, these may be torn
out. The material escaping under high pressure may cause injuries and
damage to property.
➤
If tensile forces are anticipated on the hose connections (for example
due to the positioning of the mixing unit), it is necessary to utilize strain
relief!
1.
Close the material hoses at the material
outlet of the associated fluid pump.
Observe the color coding during the
component assignment.
A
B
Fig. 13: Connecting the material hoses
2.
Connect the material hoses to the
mixing unit.
Fig. 14: Connecting the mixing unit
B
A
3.
Install the coupling piece for the packer on the static mixer
of the mixing unit.
The selection of the coupling piece is
dependent on the type of packer used.
No. Coupling piece
1
Coupling G
¼
" I
2
Nozzle M10x1 IG
3
Slide coupling M10x1
Fig. 15: Coupling pieces for packer
1
2
3