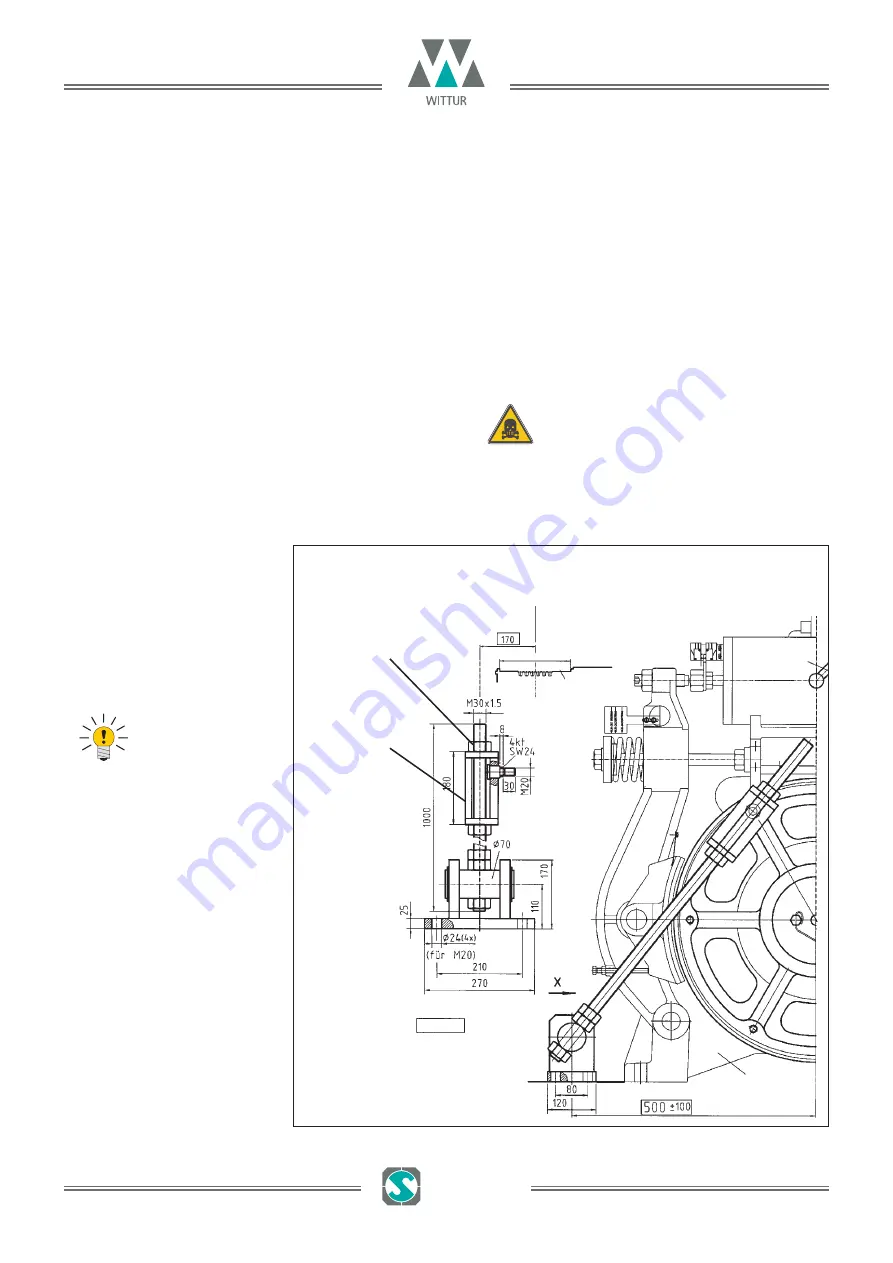
Gearless Lift Machine
WSG-18 and WLG-18
Operating Instructions
Seite/page
20
Datum/date
14.02.2006
Stand/version
0.17
Änderungen vorbehalten!
Subject to changes without notice!
MADE BY
SAD GmbH
A MEMBER OF WITTUR
9.6. Emergency evacuation
The lift design engineer must always provide for an elec-
tric return motion control (EN 81-1 /12.5.2) since a hand
wheel cannot be used with this gearless machine because
of its high torque.
Should a failure occur with the car at rest, the car can be
moved with the drive connected to the mains or to an
uninterruptible power supply (UPS) or mechanically
under its own load with the emergency brakes temporar-
ily released.
These brakes are released electrically either from the
mains or using a UPS. They can, however, also be released
manually.
The manual releasing of the shoe brake can be performed
by using the release lever.
A mechanical return motion device
can be fitted at the operator's own
responsibility if the lift needs to be
moved manually in case of a
breakdown or if the car is caught
by a safety device. The use of the
return motion device is shown in
the drawing.
Bolt the bearing
block to a cross-
beam at the recom-
mended spacing. The
cross-beam is firmly
connected to the lift
machine. When fit-
ting the device, a
switching command
"electrical supply dis-
connected" must be
activated.
The specific conditions resulting
from the different traction sheave
types and brake arrangements
must be taken into account in
regard to the arrangement of the
return motion device.
Then screw the threaded bolt into
an appropriately positioned
threaded hole in the traction
sheave using a spanner. While
releasing the brake magnets, either
electrically or using the brake lever plates, the slide block
can be displaced by turning the corresponding nuts. This
turns the traction sheave. The bolt can then be moved to
a new hole in the traction sheave, if required.
The lift must be braked when changing the
bolt.
Return motion device
Note
Danger
nut (1) SW 36
slide-block (2)
center of tr
action
sheave
traction sheave
lift machine
(left or right)
Recommendation
for mounting the
return motion
device
manual
release lever