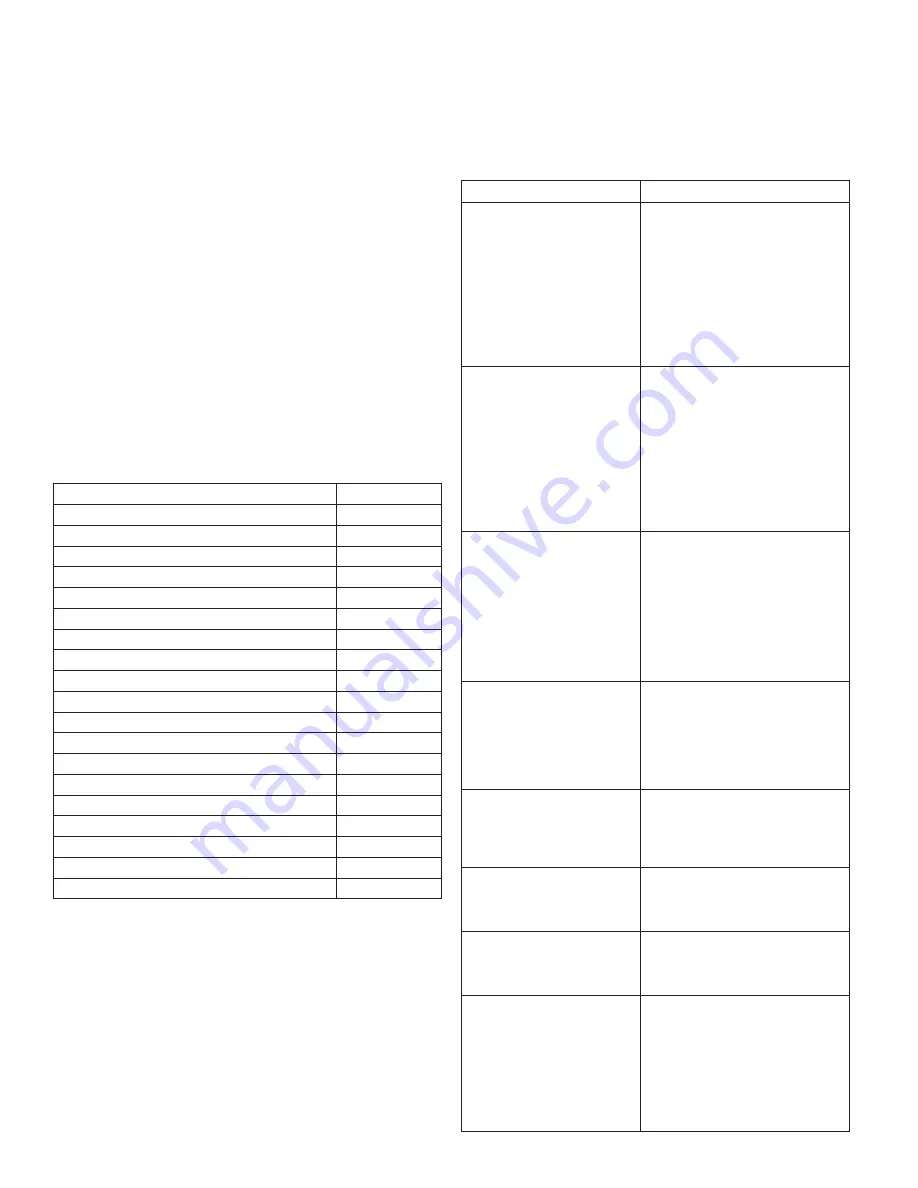
16
OPM-114
REV B
MAINTENANCE
The ultimate aim of a preventive maintenance program is to maintain
the equipment in optimum condition, for the maximum amount of time
during it’s useful life. The detection of faults before they develop into
major problems will decrease downtime. A regular schedule of cleaning
and inspection will help assure trouble-free operation. Personnel
responsible for maintenance should set up a schedule for inspection,
and cleaning at intervals calculated to keep the equipment in good
condition. In making up a schedule, keep the following in mind:
A. New equipment must be carefully monitored until extended operation
has demonstrated that it is performing satisfactorily.
B. Old equipment requires more frequent inspection (and possibly
servicing) than similar equipment that has lower hours.
C. Time spent in cleaning, inspecting and correcting minor defects
before they become major troubles saves time in overhaul and repair.
MAINTENANCE SCHEDULE
SERVICE
INTERVALS
Check Engine Oil Level
Daily
Check Coolant Level and for Leakage
Daily
Check Air Filter
Daily
Check Electrolyte Level in Battery and Clean Terminals
6 Months
Drain Water from Fuel Pre-Filter
150 Hours
Check Belts and Belt Tension
300 Hours
Check Oil Vapor Filter
300 Hours
Change Oil
600 Hours
Change Oil Filters
600 Hours
Change Fuel Filters
600 Hours
Change Fuel Prefilter
600 Hours
Check Exhaust System for Damage
6 Months
Clean Fuel Tank
6 Months
Change Auxiliary Member Belt
1200 Hours
Change Air Filter (depending on conditions)
1200 Hours
Change Coolant
1200 Hours
Change Oil Vapor Filter
2 Years
Clean Turbocharger
1200 Hours
Adjust Play in Valve-Rocker Arms and Pump-Rocker Arms
1200 Hours
* There are additional maintenance items and explanations in the
engine operator’s manual. Read thoroughly before operating this unit.
TROUBLESHOOTING TABLE
NOTE: Before doing any trouble shooting, check the digital display on
the DSE 7310 MKII. Normally, it will tell why the unit has failed. This
will shorten your trouble shooting time and in many cases, prevent the
replacement of parts that may not be defective.
Problem
Possible Causes
Unit will not crank when power fails
Digital genset not in AUTO
Transfer control switch not in
AUTOMATIC position
Incorrect wiring between ATS and genset
Defective control relay in ATS
Fuse(s) blown in the DSE 7310 MKII
Defective DSE 7310 MKII
Loose or dirty battery terminals
Defective starter
Defective start solenoid
Low/dead battery
Engine won’t crank
Low/dead battery
Blown DC fuses
Defective DSE 7310 MKII
Defective key switch
Loose or dirty battery terminals
Defective starter
Defective start solenoid
Locked up engine genset
Defective engine harness
Improper battery voltage to start solenoid,
fuel pump, or fuel solenoid
Engine cranks but will not start
Improper fuel delivery to the unit
Fuel supply shut off
Fuel tank empty
Air in the fuel system
Engine fuel solenoid has not opened
Defective fuel pump
Defective fuel solenoid
Defective engine harness
Improper battery voltage to fuel pump or
fuel solenoid
Engine starts, then stops and alarm
light comes on
Engine oil pressure is low
Engine has high water temperature
Engine has overspeed
Engine has gone into overcrank
No output from AC generator
Loss of speed signal
Loss of run signal
Engine will not come up to speed
after it starts
Insufficient fuel volume getting to the unit
1. Too small of fuel line
2. Fuel racks not open properly
Governor is defective
AC short in generator components
ATS will not transfer to Emergency
Supply (generator)
No AC generator output
Defective ATS control board. See ATS
manual
Circuit breaker open or defective
ATS will not re-transfer to normal
power
Proper power line not available at line
terminals in ATS panel
Defective ATS control board. See ATS
manual
No AC output from generator
Defective diode
Defective voltage regulator
Defective rotor
Defective stator
Defective exciter rotor
Defective exciter stator
AC short in the output leads
Defective/open generator output breaker
Wiring error