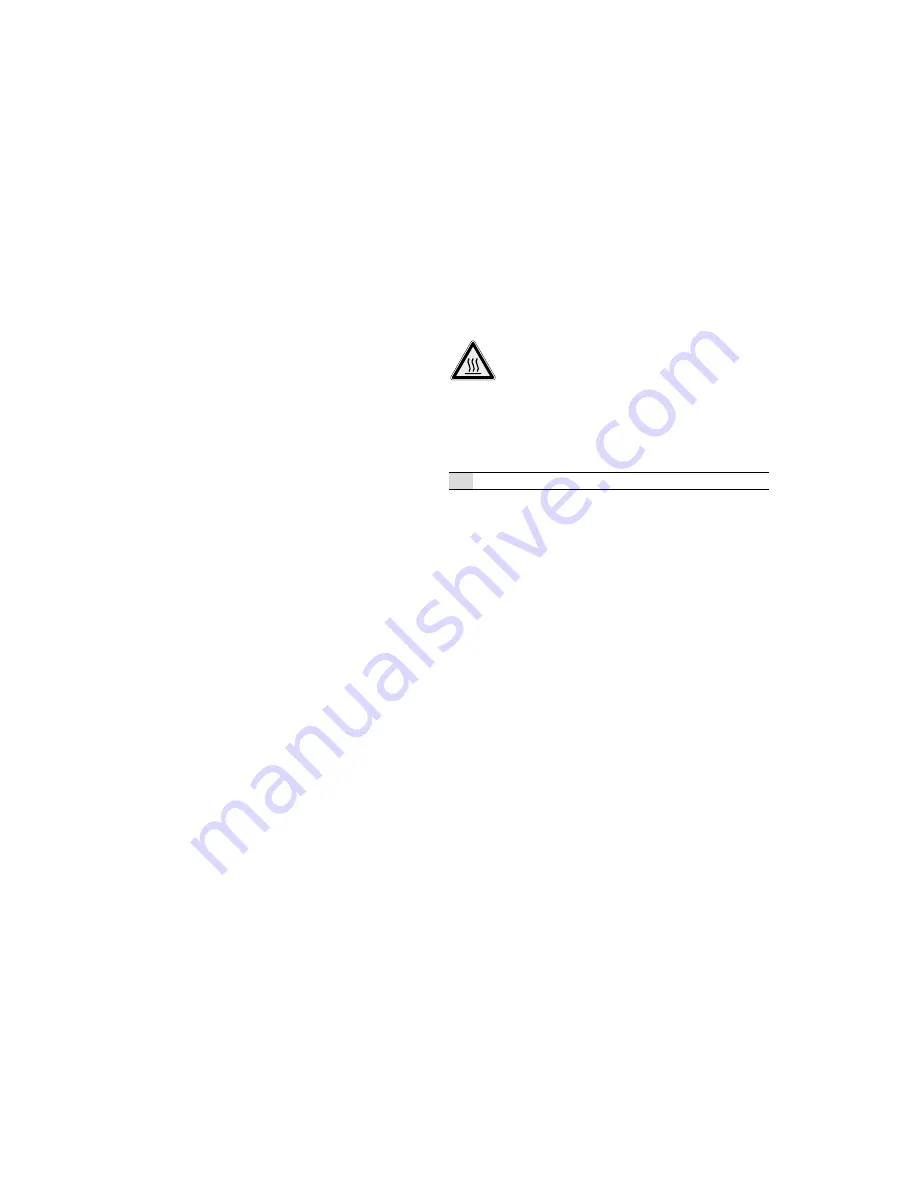
46
WILO SE 10-2014 V05 DIN A4
English
TROUBLESHOOTING AND POSSIBLE SOLUTIONS
or malfunctions in the impeller, bearings and/or
motor, which can be rectified. Larger voltage fluc
-
tuations strain the motor winding and can cause
the pump to break down. Regular inspections
can therefore largely prevent major secondary
damage and reduce the risk of total breakdown.
We recommend the use of remote monitoring for
regular inspections. Please contact Wilo customer
service.
8.3. Maintenance work
Before carrying out maintenance work:
• Disconnect the pump from the power and secure
it against being switched on inadvertently.
• Allow the pump to cool down and clean it thor-
oughly.
• Make sure that all the operationally-relevant
parts are in good condition.
8.3.1. Visual inspection of the power supply cable
The power supply cables must be checked for
blisters, cracks, scratches, abrasion and/or crush-
ing. If any damage is detected, the pump must be
decommissioned immediately and the damaged
power supply cable must be replaced.
The cables may only be replaced by Wilo
customer service or an authorised or certified
service workshop. The pump may only be start
-
ed up again once the damage has been properly
remedied.
8.3.2. Visual inspection of accessories
Accessories must be checked to ensure they are
properly fitted and function correctly. Loose and/
or faulty accessories must be repaired or replaced
immediately.
8.3.3. Visual inspection of coating and housing for
wear
The coatings and housing parts must not show
any signs of damage. If there is visible damage
to the coatings, repair the coating accordingly.
If there is visible damage to housing parts, con
-
tact Wilo customer service.
8.3.4. Functional inspection of safety and monitoring
devices
Monitoring devices include the temperature sen-
sors in the motor, humidity electrodes, overload
relay, overvoltage relay, etc.
• Motor protection, overvoltage relay and other
triggers can generally be triggered manually for
test purposes.
•
To check the pencil electrode or the temperature
sensor, the pump has to be cooled to the ambient
temperature and the electrical connection for the
monitoring equipment has to be disconnected in
the switchgear. The monitoring equipment can
then be checked with an ohmmeter. The follow
-
ing values should be measured:
•
Bimetallic strip: Value = “0” passage
•
Pencil electrode: This value must approach
infinity. If the value is low, there is water in the
oil. Also observe the instructions of the option-
al evaluation relay.
If there are larger deviations, consult the man-
ufacturer.
8.3.5. Inspection of the switchgear/relays used
See the relevant installation and operating in-
structions for a description of the individual work
steps for inspecting the switchgear/relay. Faulty
devices must be replaced immediately as they
provide no protection to the pump.
8.3.6. Oil change in sealing chamber
The sealing chamber has a hole for draining and
filling the chamber.
RISK of injury from hot and/or pressurised oil!
After the pump is switched off, the oil is still
hot and pressurised. This can cause the screw
plug to be ejected and hot oil to escape. There
is a risk of injury or burns! First allow the oil to
cool down to ambient temperature.
Fig. 7.: Screw plugs
1 Screw plug
1.
Position the pump horizontally on a firm surface
with the screw plug facing upward.
Make sure that the pump cannot fall over and/
or slip.
2. Carefully and slowly unscrew the screw plug.
Attention: the oil may be pressurised! This can
cause the screw to be ejected at speed.
3. Empty out oil by rotating the pump until the hole
points downwards. Collect the oil in a suitable
container and dispose of it in accordance with the
requirements in the "Disposal" chapter.
4. Rotate the pump back until the hole is pointing
upwards again.
5. Pour the new oil in through the hole for the screw
plug. The oil should reach up to about 1 cm below
the hole. Note the recommended oils and filling
quantities.
6.
Clean the screw plug, replace the joint ring and
screw it back in.
9. Troubleshooting and possible solutions
In order to prevent damage or serious injury while
rectifying pump faults, the following points must
be observed:
•
Only attempt to rectify a fault if you have quali
-
fied staff. This means that each job must be car
-
ried out by trained specialist staff. For example,
electrical work must be performed by a trained
electrician.
• Always secure the pump against an accidental
restart by disconnecting it from the mains. Take
appropriate safety precautions.
•
Always have a second person on hand to ensure
the pump is switched off in an emergency.