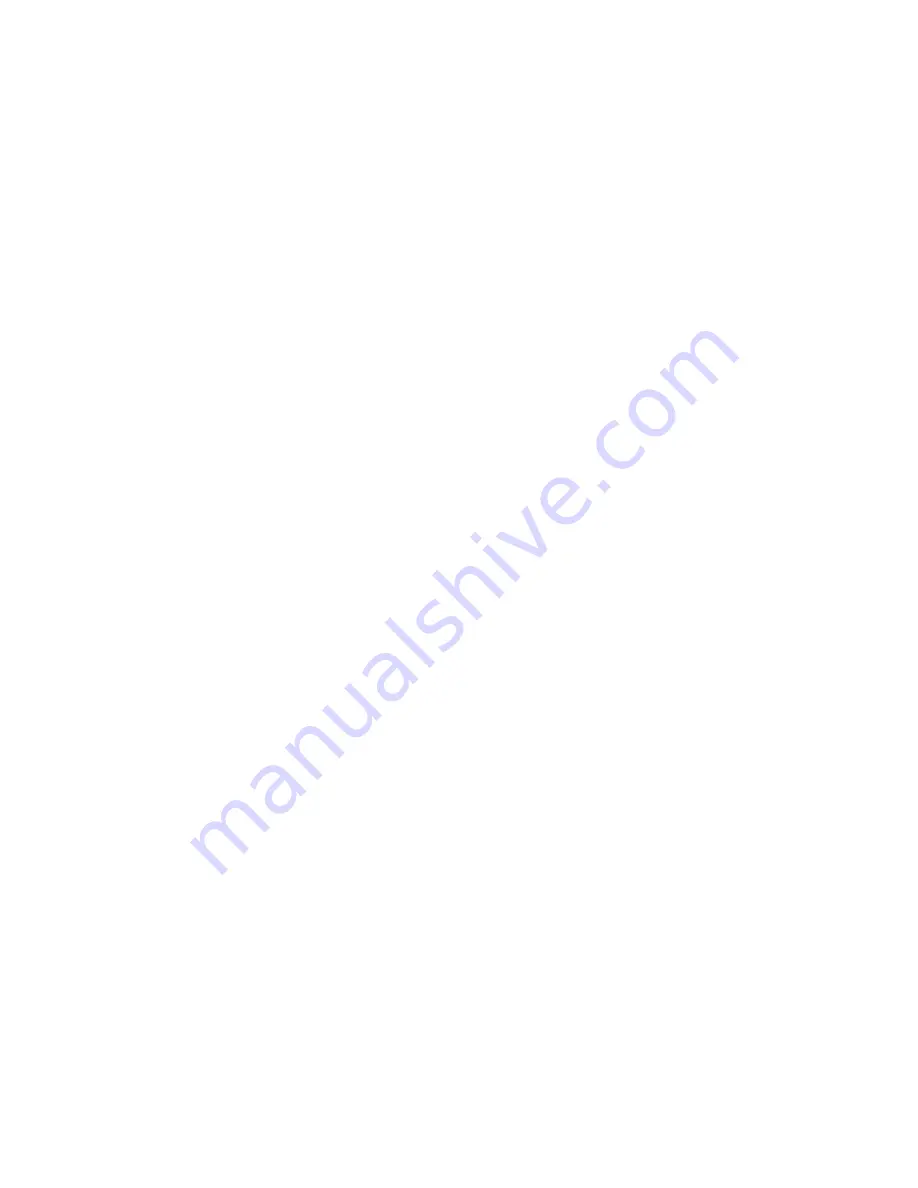
Installation and operating instructions Wilo-Rexa FIT
47
TROUBLESHOOTING AND POSSIBLE SOLUTIONS
English
• Secure moving parts to prevent injury.
• Unsanctioned changes to the pump are made at
the operator's own risk and release the manufac-
turer from any warranty obligations.
Fault: Pump does not start
1. Electricity supply interrupted, short-circuit or
earth fault in the cable and/or motor winding
•
Have the motor and wires checked by a special
-
ist and replaced if necessary
2.
Fuses, the motor protection switch and/or moni
-
toring devices are triggered
•
Have a specialist inspect the connections and
correct them as necessary.
• Have the motor protection switches and fuses
installed or adjusted according to the technical
specifications, and reset monitoring equip
-
ment.
•
Check that the impeller runs freely. If necessary
clean it and ensure it runs freely again
3.
The sealing chamber control (optional) has inter
-
rupted the power circuit (operator-related)
•
See fault: Mechanical seal leaks, sealing cham
-
ber control reports a fault or switches the pump
off
Fault: The pump starts, but the motor protec-
tion switch triggers shortly after commission-
ing
1.
The thermal trigger on the motor protection
switch is incorrectly set
•
Have a specialist compare the setting of the
trigger with the technical specifications and
correct it as necessary
2. Increased power consumption due to major volt-
age drop
• Have an electrician check the voltage on each
phase and rewire if necessary
3.
Two-phase operation
•
Have a specialist inspect the connection and
correct it as necessary
4.
Excessive voltage differences on the three phases
•
Have a specialist inspect the connection and
the switching system and correct as necessary
5. Incorrect direction of rotation
• Swap the 2 phases of the mains supply
6.
Impeller slowed by accumulation, clogging and/or
solid matter, increased current consumption
• Switch off the pump, secure it against being
switched back on again and free the impeller or
clear the suction port
7.
The fluid is too dense
• Contact the manufacturer
Fault: Pump is running but not pumping
1.
No fluid available
•
Open inlet for tank or slide valve
2. Intake blocked
• Clean the supply line, slide valve, suction piece,
suction port or suction strainer
3. Impeller blocked or slowed
• Switch off the pump, secure it against being
switched back on again and free the impeller
4.
Faulty hose/piping
• Replace defective parts
5. Intermittent operation
• Check switching system
Fault: The pump runs, but not within the speci-
fied operating parameters
1. Intake blocked
• Clean the supply line, slide valve, suction piece,
suction port or suction strainer
2. Slide valve in the pressure pipe closed
•
Fully open the slide valve
3. Impeller blocked or slowed
• Switch off the pump, secure it against being
switched back on again and free the impeller
4. Incorrect direction of rotation
• Replace two phases on the mains supply
5. Air in the system
• Check the pipelines, pressure shroud and/or
hydraulics, and vent if necessary
6. Pump pumping against excessive pressure
• Check the slide valve in the pressure pipe and
open it completely if necessary, use a different
impeller, consult the plant
7. Signs of wear
• Replace worn parts
8.
Faulty hose/piping
• Replace defective parts
9.
Inadmissible levels of gas in the fluid
• Contact the manufacturer
10.
Two-phase operation
•
Have a specialist inspect the connection and
correct it as necessary
11.
Excessive decrease in the water table during
operation
• Check the supply and capacity of the system,
and inspect the level control settings and
functionality
Fault: The pump does not run smoothly and is
noisy
1. Pump is operating in an inadmissible range
• Check the operational data of the pump and
correct if necessary and/or adjust the operating
conditions
2. Suction port, suction strainer and/or impeller
clogged
• Clean the suction port, suction strainer and/or
impeller
3. Impeller stiff
• Switch off the pump, secure it against being
switched back on again and free the impeller
4.
Inadmissible levels of gas in the fluid
• Contact the manufacturer
5.
Two-phase operation
•
Have a specialist inspect the connection and
correct it as necessary
6.
Incorrect direction of rotation
• Replace two phases on the mains supply
7. Signs of wear
• Replace worn parts
8. Defective motor bearing
• Contact the manufacturer