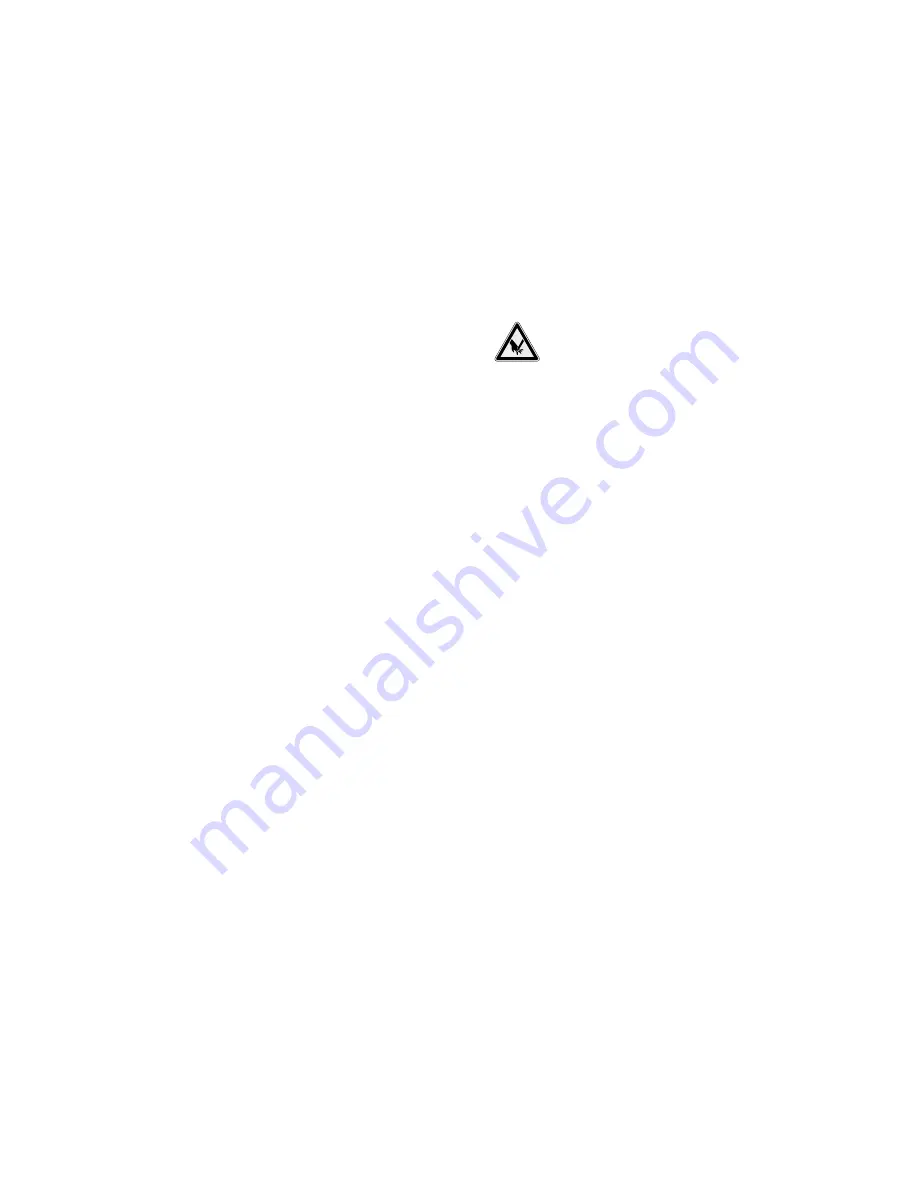
Installation and operating instructions Wilo-Rexa FIT
37
INSTALLATION
English
poisonous or asphyxiating gases forming, the
necessary precautions must be taken.
• Depending on the ambient conditions in opera-
tion, the unit planner must select the sump size
and motor cooling time accordingly.
•
Ensure that lifting equipment can be fitted
without any trouble, since this is required for
assembly and removal of the pump. It must be
possible to reach the pump safely in its operating
and storage locations using the lifting equip-
ment. The machine must be positioned on a firm
bearing surface. For transporting the pump, the
load-carrying equipment must be secured to the
lifting eyelets provided. When using chains, they
must be connected with a shackle to the lifting
eyelets or the carrying handle. Lifting gear must
be technically approved.
• Power supply cables must be laid out in such
a way that safe operation and trouble-free
assembly/dismantling are possible at all times.
The pump must never be carried or dragged by
the power supply cable. Check whether the cable
present is long enough for its cross-section and
its installation type.
• When using switchgears, the corresponding
protection class must be observed. In general,
switchgears are to be installed outside poten-
tially explosive areas in such a way that they are
protected from flooding.
• Structural components and foundations must
be sufficiently stable to allow the product to be
anchored securely and functionally. The operator
or the supplier is responsible for the provision of
the foundations and their suitability in terms of
dimensions, stability and strength!
• If the motor housing is to be taken out of the
fluid during operation, the operating mode for
non-immersed operation should be followed.
To keep dry motors sufficiently cooled in S3
mode, they must be flooded completely before
being switched back on if the motor has been
taken out of the fluid!
•
Never let the pump run dry. The water level must
never fall below the minimum. Therefore, we
recommend installing a level control system or
a dry-running protection system where there are
great variations in the level.
•
Use guide and deflector plates for the fluid intake.
If the water jet reaches the surface of the water,
air will be introduced into the fluid, which can
accumulate in the pipe system. This can result in
inadmissible operating conditions and to deacti-
vation of the entire system.
• Check that the available planning documentation
(installation plans, layout of the collector tank,
intake ratios) is complete and correct.
• Please observe all regulations, rules and legal
requirements for working with and underneath
heavy suspended loads. Wear appropriate protec-
tive clothing/equipment.
• Please also observe the applicable national acci-
dent prevention regulations and trade association
safety provisions.
5.3.1. Maintenance work
After a storage period of more than 6 months, the
following maintenance work must be carried out
before installation:
• Rotate impeller
• Check oil level in the sealing chamber
Rotate impeller
1.
Position the pump horizontally on a firm surface.
Make sure that the pump cannot fall over and/
or slip.
2. Carefully and slowly reach into the hydraulics
housing from below and rotate the impeller.
BEWARE of sharp edges!
Sharp edges can form on the impellers and
hydraulic opening. There is a risk of injury!
Wear the necessary protective clothing, such
as protective gloves.
Check oil level in sealing chamber
The sealing chamber has a hole for draining and
filling the chamber.
1.
Position the pump horizontally on a firm surface
with the screw plug facing upward.
Make sure that the pump cannot fall over and/
or slip.
2.
Unscrew the screw plug (see Fig. 7).
3.
The oil should reach up to about 1 cm below the
hole for the screw plug.
4. If there is not enough oil in the sealing chamber,
top it up. To do so, follow the instructions under
"Oil change" in the "Maintenance and repair"
chapter.
5. Clean the screw plug, replace the joint ring, if
necessary, and screw it back in.
5.3.2. Stationary wet well installation
A suspension unit must be installed for wet
well installation. This must be ordered from the
manufacturer separately. The pipe system on the
pressure side is connected to this.
The connected pipe system must be self-sup-
porting, i.e. it may not be supported by the
suspension unit.
The collector tank must be laid out so that the
suspension unit can be installed and operated
without difficulty.
If the motor emerges during operation, the
following operating parameters must be strictly
observed.
•
The
max. fluid temperature and ambient tem
-
perature
is
40 °C
.
•
Details for "Non-immersed operating mode"