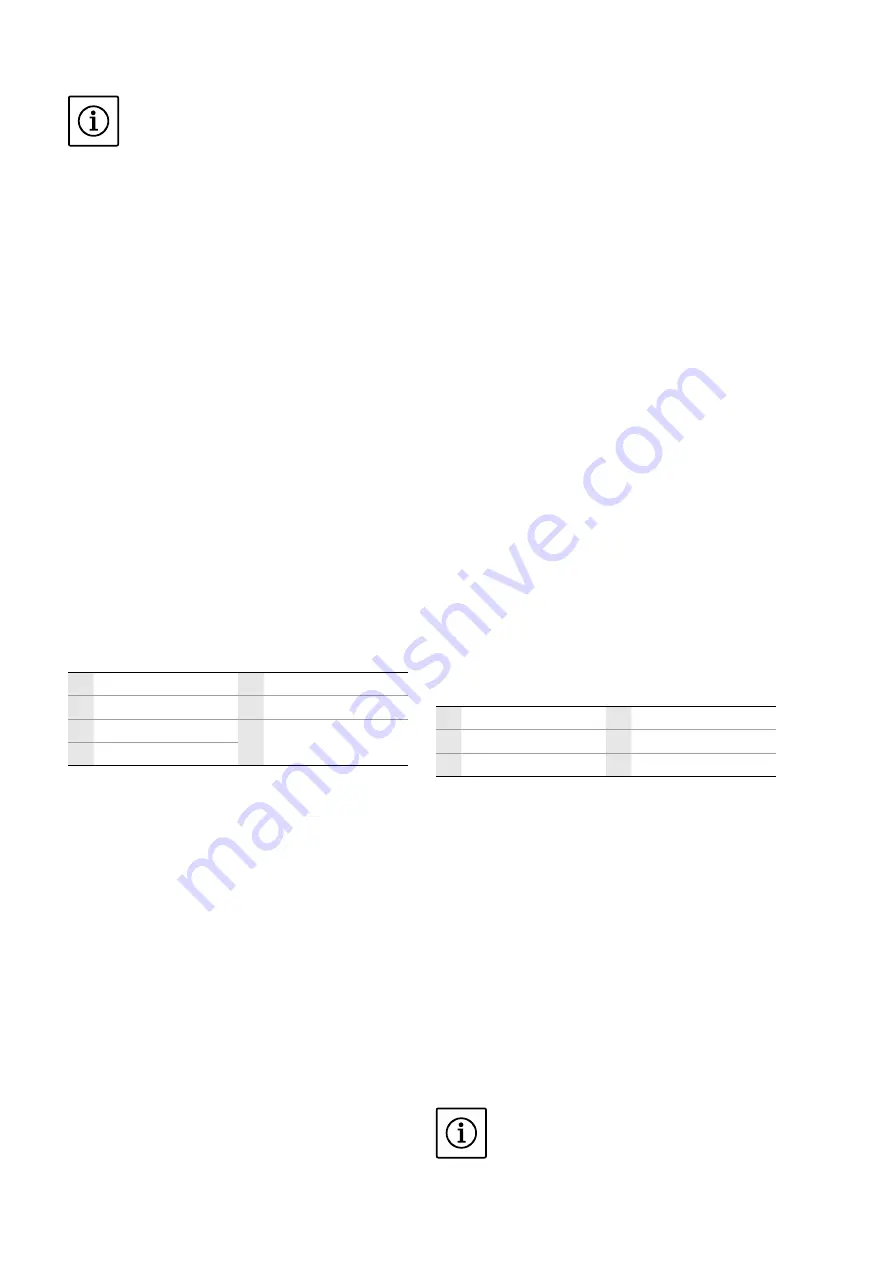
34
WILO SE 03/2016 V06 DIN A4
English INSTALLATION
NOTE
• The pressure pipe must have DN 80 or DN 100 in
areas where DIN EN 12050‑1 applies!
• According to EN 12056‑4, the flow rate at the
duty point in the pressure pipe must be between
0.7 m/s and 2.3 m/s.
• Reducing the pipe diameter in the pressure pipe
is not permitted.
The following information must be observed
when connecting the pressure pipe:
• The pressure pipe must be self-supporting.
• The pressure pipe must be connected so it is free
from vibration, noise‑insulated and flexible.
• The connection as well as all unions must be
absolutely leak-tight.
• A
max. tightening torque of 5 Nm
is permitted
when using pipe clamps.
• The pressure pipe must be routed where it is
protected from frost.
• To avoid any backflow from the main public sew-
er, install the pressure pipe as a loop. The bottom
edge of the pipe loop must be above the locally
defined backflow level at its highest point.
• A non-return valve with ventilation device must
be fitted directly after the pressure port. This
allows the pressure pipe to be drained if the unit
is subsequently removed.
• A gate valve must be fitted directly after the
non-return valve. The pressure pipe is then
mounted on this using flange connectors.
Fig. 3: Connecting the pressure pipe
1 Lifting unit
5 Pressure pipe
2 Pressure port
6 Flange connector
3 Non-return valve
7
Flexible connecting
hose
4 Gate valve
1. Route the pressure pipe so it is perpendicular to
the pressure port. Please refer to the installation
plan in the catalogue for the precise dimensions
of the lifting unit.
2. Install the supplied non-return valve on the pres-
sure port.
3. Install the gate valve on the non-return valve.
4. Push the flexible connecting hose over the dis-
charge pipeline.
5. Plug the flange connector into the flexible con-
necting hose and mount on the gate valve.
To ensure that the system is installed acousti-
cally isolated at the discharge pipeline, there
must be a distance of 40–60 mm between end
discharge pipeline and the end of the flange
connector.
If the distance is too small, the discharge pipe
or the flange connector must be shortened. If
the distance is too large, the hose section can-
not be properly secured.
6. Align the flexible connecting hose to the centre
and use the enclosed pipe clasp to attach to the
flange connector and to the discharge pipeline.
Max. tightening torque: 5 Nm
Connecting the DN 100 main inlet
The inlet can be on both sides and the rear end,
according to choice.
In addition, there are markings on the reservoir for
direct connection
• of a stand-alone toilet at a height of 180 mm
• and a wall-mounted toilet at a height of 250 mm.
Fig. 4: Free inlet surfaces
The following information must be observed
when connecting the inlet pipe:
• The inlet is only allowed to be within the marked
areas.
If the inlet is outside the marked areas
• then the unit
could leak
.
• there
could be backflow
into the connected
inlet pipes.
• The inlet must be routed so it is self-draining.
Furthermore, an inlet surge must be prevented, as
must any air intake.
An inlet surge and/or air intake can cause mal-
functions of the lifting unit!
• The min. connection height is 180 mm.
An inlet at less than this height can lead to
backflow in the inlet pipe!
• The connection as well as all unions must be
absolutely leak-tight.
• A gate valve must be installed in the inlet before
the reservoir!
• Pipe clamps are allowed to be tightened to a
max.
tightening torque of 5 Nm
.
Fig. 5: Connecting the inlet
1 Reservoir wall
4 Inlet pipe
2 Hole saw
5 Pipe clamp
3 Inlet seal
1. Route the inlet to the reservoir and mark the inlet
connection on the reservoir.
2. Use the supplied hole saw to cut the hole for the
inlet into the reservoir wall. The following points
must be observed when doing this:
• Comply with the dimensions of the inlet surfaces
• Maximum rotation speed of the drill: 200 rpm
• Make sure the excess material in the drill bit is
removed completely:
• If the excess material removal is reduced, the
material will heat up excessively and melt.
Interrupt the drilling process, allow the material
to cool and clean the hole saw!
• Reduce the speed of the drill.
• Vary the feed pressure when drilling.
• Check the hole diameter: DN 100 = 124 mm
NOTE
Drill the connection for the inlet carefully. The
subsequent impermeability of the connection
depends on this!