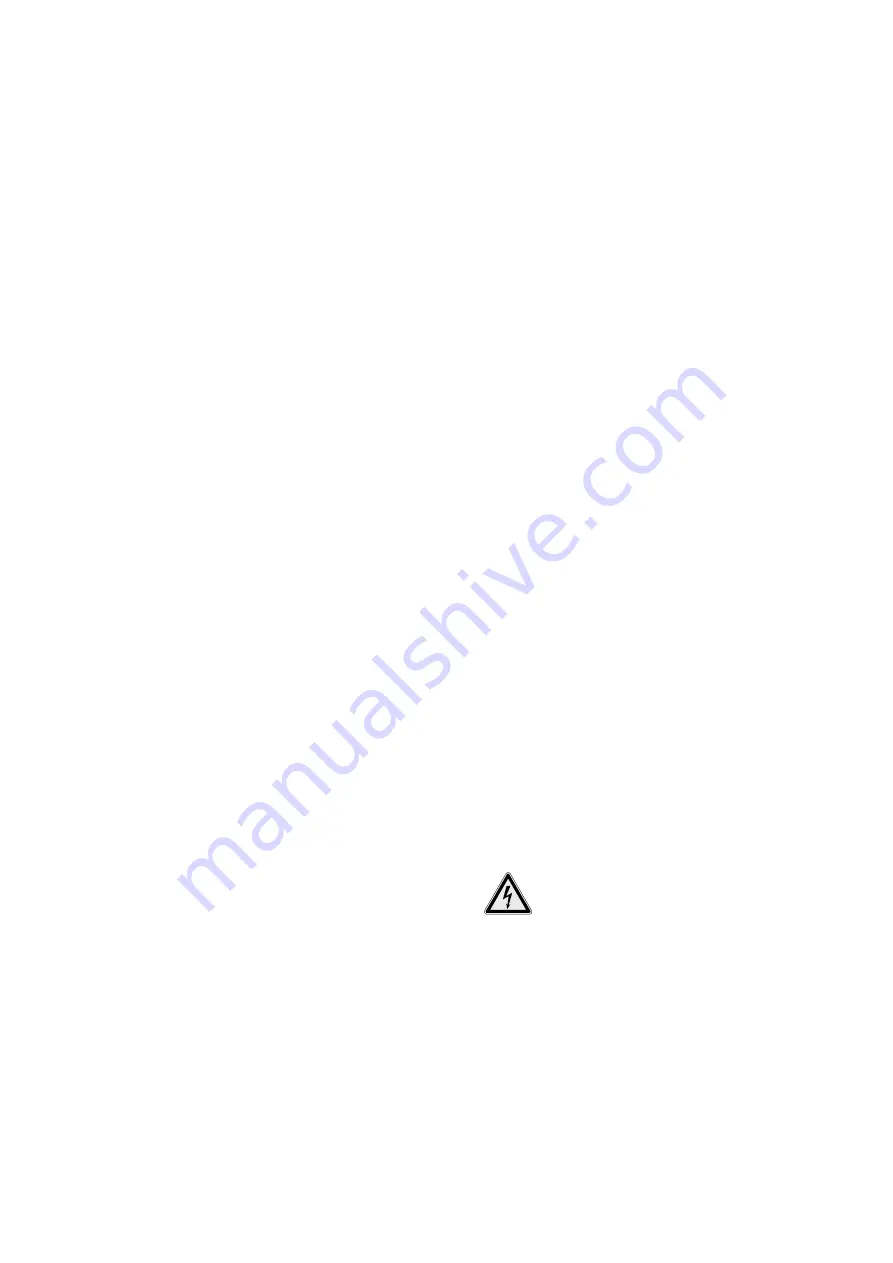
Installation and operating instructions Wilo-Drain TMT 32M 33
COMMISSIONING
English
Motor compartment monitor
• The motor compartment monitor must be con-
nected via an evaluation relay. We recommend
the “NIV 101/A” relay for this. The threshold is
30 kΩ. When the threshold is reached, the unit
must switch off.
5.6. Motor protection and activation types
5.6.1. Motor protection
The minimum requirement for motors with a free
cable end is a thermal relay/motor protection
switch with temperature compensation, differ
-
ential triggering and an anti-reactivation device
in accordance with VDE 0660 or the appropriate
national regulations.
If the pump is connected to electrical systems
in which faults frequently occur, we recommend
installing additional protective devices provided
by the customer (overvoltage, undervoltage or
phase failure relays, lightning protection etc.).
We also recommend installing a residual-current
device (RCD).
Local and national regulations must be observed
when connecting the pump.
5.6.2. Activation types
Direct activation
At full load, the motor protection should be set
to the rated current shown on the rating plate.
At partial load, we recommend that the motor
protection be set 5% above the current measured
at the duty point.
Soft start activation
•
At full load, the motor protection should be set to
the rated current at the duty point. At partial load,
we recommend that the motor protection be set
5% above the current measured at the duty point.
• The current consumption must be below the rat-
ed current throughout the entire operation.
•
Due to the upstream motor protection, starting or
stopping should be completed within 30 seconds.
•
To avoid power dissipation during operation,
bypass the electronic starter (soft start) once
normal operation is reached.
5.6.3. Operation with frequency converters
Operation on a frequency converter is
not
pos-
sible.
6. Commissioning
The “Commissioning” section contains all the im
-
portant instructions for the operating personnel
for starting up and operating the pump.
The following conditions must be adhered to and
monitored:
• Type of installation
•
Operating mode
• Minimum water submersion/max. immersion
depth
These general conditions must also be checked
after a lengthy period without operation, and
any defects detected must be repaired!
Always keep this manual either by the pump
or in a place specially reserved for it, where it is
accessible for the entire operating personnel at
all times.
In order to prevent damage or serious injury when
commissioning the pump, the following points
must be observed:
•
Commissioning of the pump may only be carried
out by qualified and trained personnel in accord
-
ance with the safety instructions.
• All persons working on or with the pump must
have received, read and understood this operating
and maintenance manual.
• All safety devices and emergency cut-outs must
be connected and checked to ensure that they
work properly.
• Electrical engineering and mechanical adjust-
ments must be made by qualified personnel.
•
The pump is suitable for use under the specified
operating conditions.
• The work area of the pump is not a recreational
area and is to be kept free of people! No persons
are allowed in the work area during start-up or
operation.
•
When working in sumps, a second person must be
present for safety reasons. Adequate ventilation
must be ensured if there is danger of poisonous
gases forming.
6.1. Electrical system
Connect the pump and install the power supply
cables as described in the “Installation” section
and in accordance with the VDE guidelines and
applicable national regulations.
The pump must be properly protected and
grounded.
Observe the direction of rotation. If the direction
of rotation is incorrect, the pump will not perform
as specified and may be damaged.
Make sure all monitoring devices are connected
and have been tested.
ELECTRICAL hazard!
Electrical current can cause fatal injuries if not
handled correctly! All pumps with free cable
ends (i.e. without plugs) must be connected
by a qualified electrician.
6.2. Rotation control
The pump is checked and adjusted in the factory
to ensure that the direction of rotation is correct.
The connection must be made according to the
wiring labels.
A test run must be performed under general op-
erating conditions!
6.2.1. Checking the direction of rotation
The direction of rotation must be checked with a
rotating field tester by a local electrician. For the