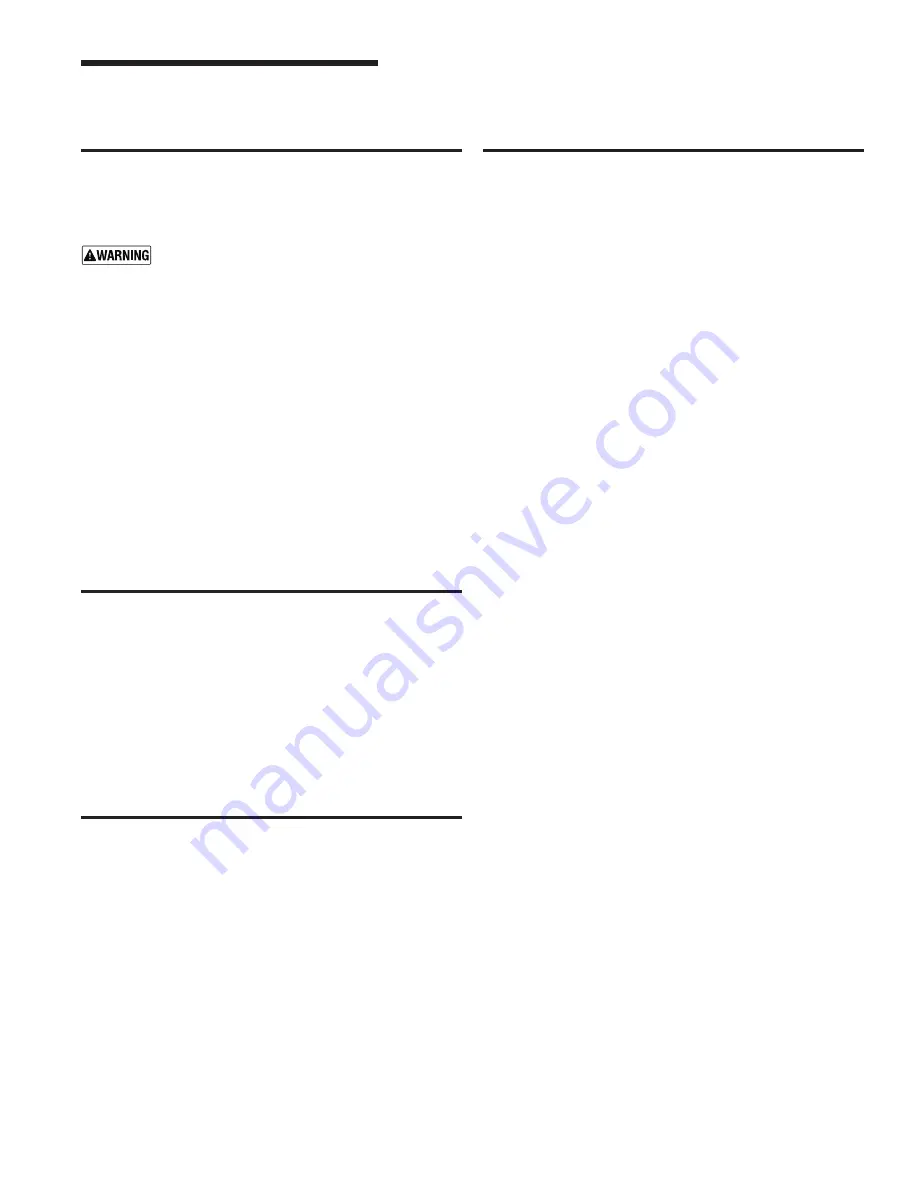
29
Part Number 550-142-785/0812
GWI
Series 2
Gas-Fired Water Boilers –
Boiler Manual
11 Service and maintenance
continued
Inducer motor
1. With boiler power OFF
, place a few drops of S.A.E. 20 motor
oil in each of the two motor oiling cups.
Use only S.A.E. 20 motor oil to lubricate inducer
motor. Do not use universal household oils. Motor
could be damaged, resulting possible severe prop-
erty damage.
Oiled-bearing circulators
1. The circulator shipped with the GWI boiler is water-lubricated.
No oiling is required.
2. Check other circulators in the system. Oil any circulators
requiring oil, following circulator manufacturer’s instructions.
Over-oiling will damage the circulator.
Temperature sensor
1. The temperature sensor may accumulate deposits on the
probe surface. Annual inspection and cleaning of the probe
will improve boiler performance.
Disconnect power, unplug harness from sensor.
a. Drain boiler water to a level below the sensor.
b. Remove sensor from boiler.
c. Wipe any built up contaminates from probe and insulator
surfaces.
d. Reinstall sensor into boiler.
❏
Service
❏
Start-up
1. Perform start-up procedures of
Section 7, pages 18–20,
including procedure to verify operation of burners on page 20.
2. Verify cold fill pressure is correct and that fill system is working
properly.
3. Verify antifreeze level (if used) is at the right concentration
and that inhibitor level is correct.
4. Check gas piping, per manual
Sections 5 and 7
, verifying no
indications of leakage and all piping and connections are in
good condition.
5. Read the “Operating instructions” (
page 26
).
6. Start the boiler following the “Operating instructions” (
page 26
).
❏
Check/test
Gas piping
1. Sniff near floor and around boiler area for any indication of a
gas leak.
2. Test gas piping using bubble test, per Section 5, page 16
of
this manual, if there is any indication of a leak.
Cold fill and operating pressures
1. While the system is cold, note the pressure reading on the
boiler pressure/temperature gauge. Verify that cold fill pressure
is correct.
2. Watch the pressure as the boiler and system heat up to en-
sure pressure rise is normal. Too high a rise would indicate a
waterlogged or undersized expansion tank.
Air vents and air elimination
1. Inspect automatic air vents (if used). Also inspect air separa
-
tors to ensure they are operational.
2. The cap must be unscrewed one turn to allow air to escape.
3. If the air vent is leaking, remove cap and briefly push valve
— then release to clean the valve seat.
4. Replace cap by twisting all the way onto valve and then un-
screwing one turn.
Limit controls and cutoffs
1. Inspect and test the boiler limit control. Verify operation by turn
-
ing control set point below boiler temperature. Boiler should
cycle off. Return dial to original setting.
2. Inspect and test additional limit controls or low water cutoffs
installed on system.
Expansion tank
1. Expansion tanks provide space for water to move in an out as
the heating system water expands due to temperature increase
or contracts as the water cools. Tanks may be open, closed
or diaphragm or bladder type. See Section 4, page 13
of this
manual for suggested locations of expansion tanks and air
eliminators.
Open-type
— located above highest radiator or baseboard
unit, usually in the attic or closet. Has a gauge glass and
overflow pipe to a drain.
Closed-type
— welded gas tight and located above boiler.
Tank is partially filled with water, leaving an air cushion for
expansion.
• Make sure this type of tank is fitted with a tank fitting,
such as the B & G Tank-Trol or Taco Taco-Trol. This fitting
reduces gravity circulation of air-saturated tank water
back to the system and prevents the air from bubbling up
through the water as it returns from the system.
• Do not use automatic air vents in systems with closed-
type tanks. The air will escape from the system instead of
returning to the tank. Eventually, the tank will waterlog and
no longer control pressurization. The boiler relief valve will
weep frequently.
Diaphragm- or bladder-type — welded gas tight with a rub-
ber membrane to separate the tank pressurizing air and the
water. May be located at any point in the system, but most
often found near the boiler.
• Systems with this type of expansion tank require at least
one automatic air vent, preferably located on top of an air
eliminator, as shown in examples in manual
Section 4,
page 13.
2. If relief valve has tended to weep frequently, the expansion
tank may be waterlogged or undersized.
Closed-type tank — tank is most likely waterlogged. Install
a tank fitting if not already installed. Then check fill level per
fitting manufacturer’s instructions. If fill level is correct, check
tank size against manufacturer’s instructions. Replace with a
larger tank if necessary.
Diaphragm- or bladder-type — first, check tank size to be sure
it is large enough for the system. If size is too small, add ad
-
ditional tank(s) as necessary to provide sufficient expansion. If
tank size is large enough, remove tank from system and check
charge pressure (usually 12 psig for residential applications).
If tank won’t hold pressure, membrane has been damaged.
Replace tank.
❏
Check/test