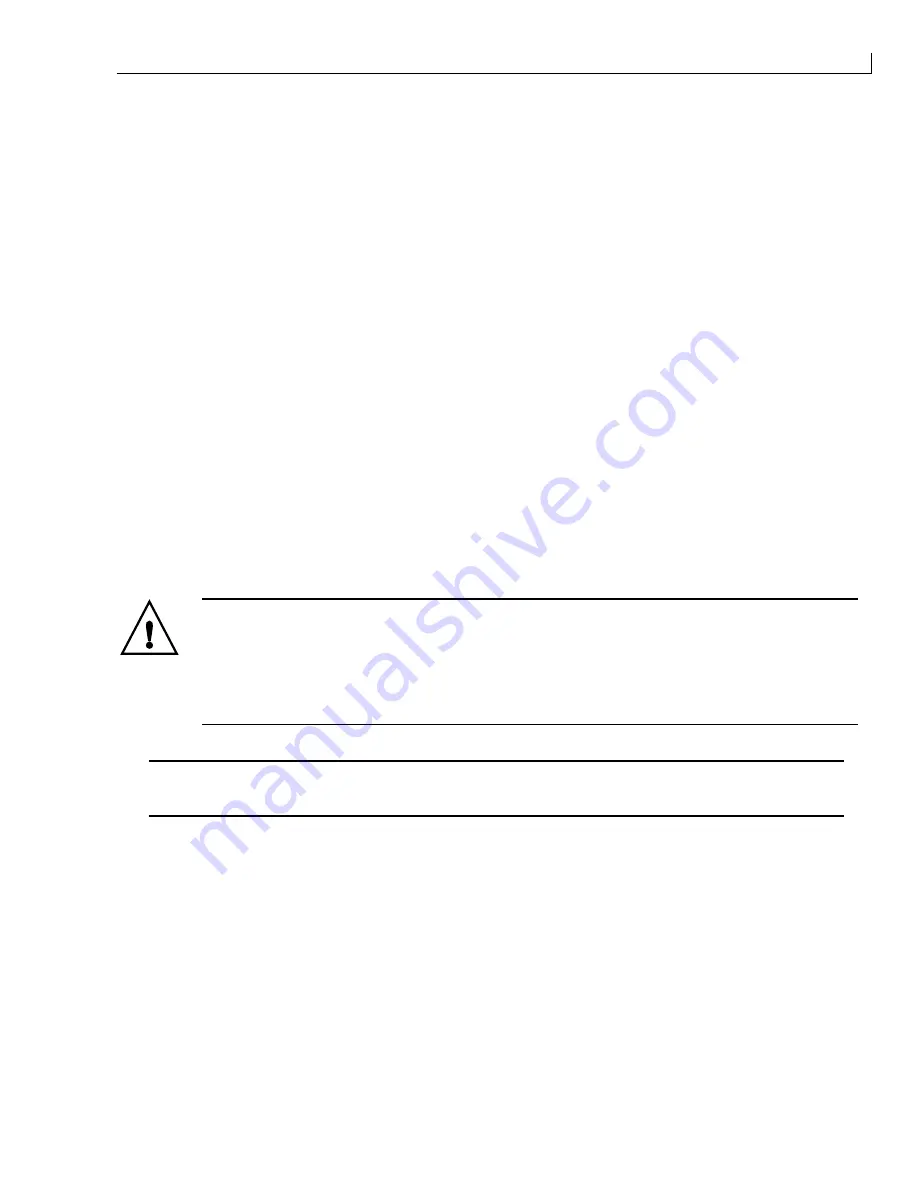
Disassembly and Assembly: Introduction
Issue 2
109
Part No. 306-0430-102
D
ISASSEMBLY AND
A
SSEMBLY
Introduction
This section contains complete instructions for the removal and installation of the components and
sub-assemblies listed below:
Component
Page
Component
Page
I/O Board
110
Flush Pump
126
CPU Board
112
Solenoid Valves
127
Power Supply Unit
113
Fan
128
PSU Fuses
115
Fan Failure Card
129
LCD/Backlight Assembly
115
EHT Module
130
Keypad
116
Head Manifold
131
Ink or Top Up Reservoir Sensor
117
Phase Detector
133
Mains Inlet Connector
119
EHT Block
135
Mains Switch
120
Nozzle Assembly
137
Fluid Management System
121
RS232 Jumper
139
Ink System Pump
123
Umbilical
141
WARNING - LETHAL VOLTAGES
Lethal voltages are present within this equipment when it is connected to the mains
electrical supply. Only trained and authorised personnel may carry out maintenance work.
Observe all statutory electrical safety codes and practices. Unless it is necessary to run
the printer, disconnect the printer from the mains electrical supply before removing the
covers or attempting any service or repair activity, otherwise death or
personal injury may result.
Caution - Electrostatic Sensitive Devices
The
printed circuit boards contain static sensitive devices. A suitably grounded, antistatic wrist strap
must be worn when working on or handling printed circuit boards.
Содержание 430
Страница 1: ...430 Ink Jet Printer Service Manual THE WORLD S CODING AND LABELLING COMPANY ...
Страница 7: ...430 Ink Jet Printer Service and Maintenance Manual vi Issue 2 Part No 306 0430 102 ...
Страница 17: ...430 Ink Jet Printer Service and Maintenance Manual xvi Issue 2 Part No 306 0430 102 ...
Страница 31: ...430 Ink Jet Printer Service and Maintenance Manual 14 Issue 2 Part No 306 0430 102 ...
Страница 61: ...430 Ink Jet Printer Service and Maintenance Manual 44 Issue 2 Part No 306 0430 102 ...
Страница 161: ...430 Ink Jet Printer Service and Maintenance Manual 144 Issue 2 Part No 306 0430 102 ...
Страница 181: ...430 Ink Jet Printer Service and Maintenance Manual 164 Issue 2 Part No 306 0430 102 ...
Страница 200: ... ...
Страница 202: ... ...