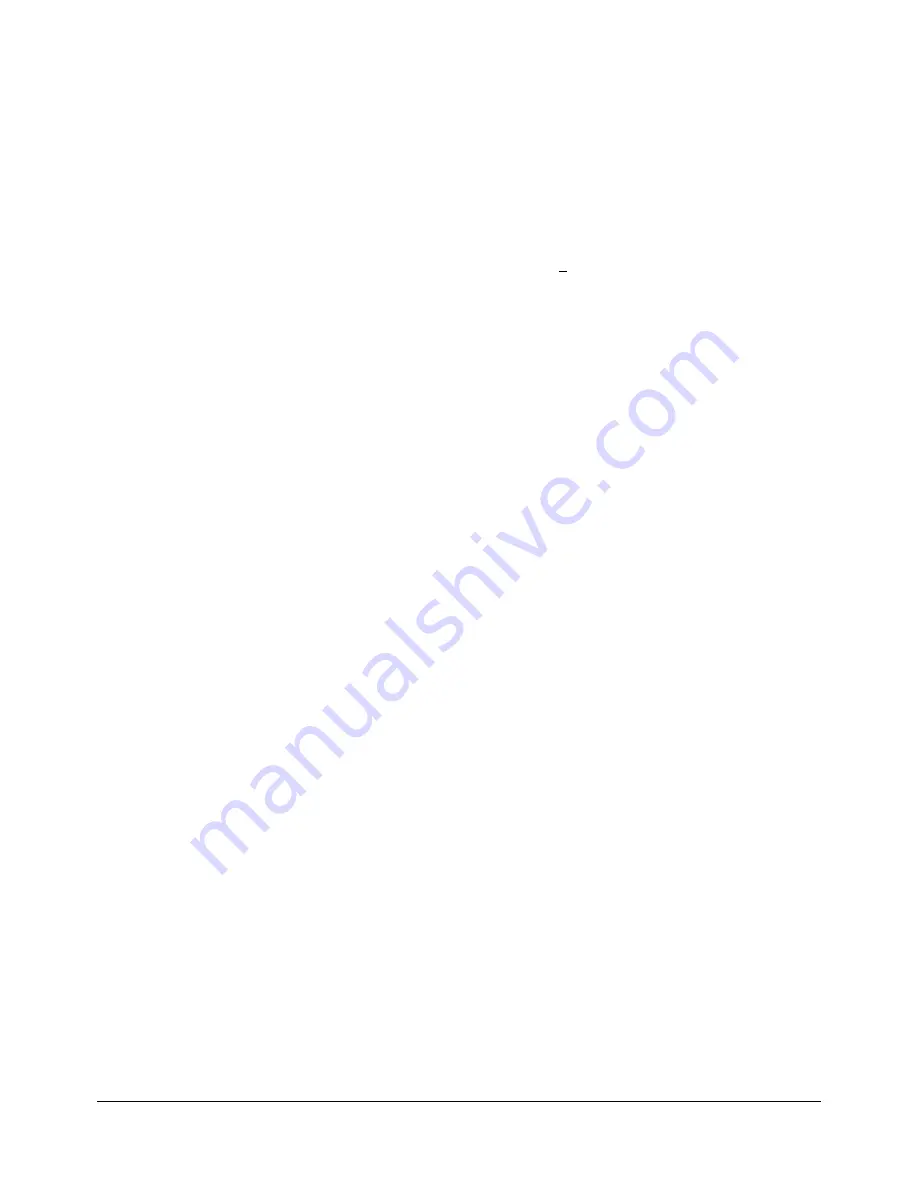
© Wikora GmbH
Page 11
As of November 2013
Errors excepted.
11 Maintenance and wear parts
According to the regulations for gas operated burner units the end user has to have the appliance checked every year by a
qualified specialist. Only original spare parts are to be used. The following work needs to be done:
1.
Check safety anode for wear and tear. When heavy wear occurs, a new original safety anode is to be fitted to
protect the tank against corrosion.
2.
Check ignition safety valve: Close gas stop cock for 20 – 45 seconds. The safety pilot should audibly close after the
gas stop cock has been closed.
3.
Clean gas filter at the entrance of the control fittings
4.
Clean pilot burner and main burner. (Removal and fitting of burner units can be found on page 9 „Conversion to other
gas types“
5.
Clean baffle plate (6), fire tube and combustion chamber with a brush.
6.
Rinse vessel with fresh water
7.
Check temperature limiter in water or similar. It needs to switch off at 92 + 3 C
8.
Check the plastic pipes for cold and warm water as well as possibly circulation connections and exchange when
damaged.
9.
When cleaning is finished, prepare the appliance for use. Check safety valve at the cold water supply by venting and
check all gas and water carrying devices on tightness. Put the appliance into operation. Check gas setting (see page
8 section „gas regulation).
10. Check flue gas evacuation.
12 User Information
The boiler is a quality appliance. It is tested and approved according to the current regulations regarding energy efficiency,
presser safety and operational safety. It can be adjusted to natural gas and liquid gas and has an increase pressure safety
(10bar). It has a long life expectancy. This is because the high quality enamel application takes place directly at the already
welded boiler which guaranties an all round protection against corrosion
.
Installation, calibration and commissioning must
only to be undertaken by a registered and qualified specialist, approved by
the gas board. Any fault can be identified according to the fault-identification list. The specialist will inform the customer on
how the appliance is used and how it works. The customer is also to be informed of the importance of regular maintenance
and that this is a decisive factor as to how long the appliance will last. Openings necessary to allow air circulation around the
site of installation must not to be reduced nor closed. Exhaust parts must not be altered in any way. The customer is not
permitted to undertake any alterations or maintenance issues.
The boiler temperature can be regulated with the temperature control button (20). High temperatures are only to be run for
short periods of time (lime scale build up). Chose a setting between 4 and 5, about 60° C for an economic and hygienic (e.g.
legionella) running. In buildings with long pipe works – e.g. hospitals, old people’s homes, hotels and blocks of flats – the
water temperature has to be set at 60° C. This also applies to installations with more than one boiler, should they have a
combined water volume of more than 400 liters.
In frosty weather or if frost is expected, the appliance is either to be kept running or emptied completely.
12.1
Commissioning and handling
See point 6.
12.2
Care
A damp cloth is sufficient to clean the outer parts. Please avoid using any abrasive or solvent cleaning agents. Before putting
the tank into operation but also during operation, the functional capacity of the safety valve must by checked at regular
intervals by venting. When working correctly, water will run out at full blast.
12.3
Maintenance
The end user has to have the appliance cleaned and checked on its impeccable functioning annually by a qualified and
registered specialist and according to the regulations regarding gas-operated appliances. Occurring defects must be repaired
immediately. Before any intervention make sure that the stop cocks for gas and water are closed.
Any maintenance work to be carried out can be found in section 11. Should it not be possible to establish the cause of any
fault, inform customer services, the sales representative or the company with all findings. Please indicate in that case the
technical data on the performance sticker.
13 Faults
A member of our customer service team is always happy to assist you with any fault. However, should the fault lie with the user
or the installer, then the costs have to be passed on. This also applies during the period when the appliance is still covered
under warranty. In case of warranty the company will cover the costs raised by customer services.